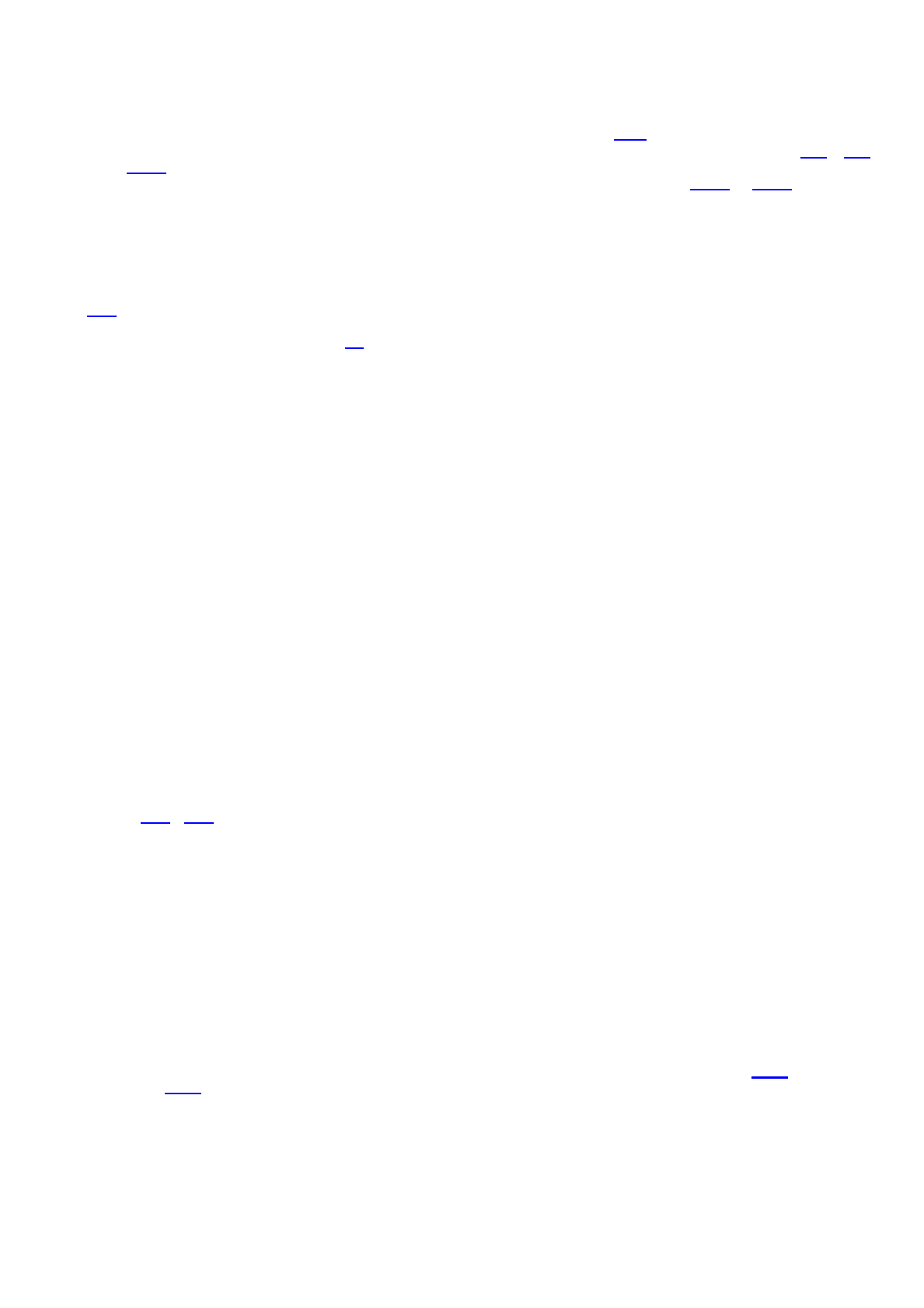
анализ результатов технических освидетельствований, осмотров, гидравлических испытаний и обследований
трубопровода, а также данных о повреждениях, ремонтах и реконструкциях.
При отсутствии необходимых сведений в документации на трубопровод допускается использовать информацию, полученную
опросом обслуживающего персонала.
8.8.6 Программы контроля трубопроводов после отработки назначенного (или дополнительно назначенного) срока службы,
включающие методы, объёмы, элементы и зоны контроля, приведены в п. 5.6.8
настоящего стандарта. Программы
конкретизированы применительно к различным группам трубопроводов по параметрам рабочей среды (таблицы 5.26
5.29 в
п.п. 5.6.8.8
). Необходимость проведения исследований металла на вырезках из трубопроводов определяется
специализированной организацией, за исключением обязательных случаев, указанных в п.п. 5.6.8.6
д), 5.6.8.6е) настоящего
стандарта.
8.8.7 Установленные по результатам анализа технической документации данные по материалам и технологии изготовления
деталей и элементов трубопроводов с учётом параметров эксплуатации должны быть сопоставлены с требованиями
соответствующих нормативных документов (Правил Государственного надзорного органа, технических условий) в части их
удовлетворения этим требованиям.
8.8.8 Выявленные по результатам контроля отклонения в размерах и форме элементов, а также дефекты металл
(коррозионные язвы, деформации, дефекты сварки и др.) не должны выходить за пределы требований норм оценки качества - п.
7.2.5
настоящего стандарта.
8.8.9 Контрольный расчёт на прочность элементов трубопровода от действия внутреннего давления выполняют в
соответствии с положениями подраздела 6.3
настоящего стандарта. Работоспособность элемента будет считаться обеспеченной
при выполнении условия:
(S
f
)
min
≥ S
R
+ с
2
,
где S
f
- фактическая толщина стенки, S
R
- расчётная толщина стенки, с
2
- эксплуатационная прибавка.
Рекомендуется в расчётах принимать с
2
= 0,5 мм для трубопроводов, работающих при температуре выше 350 °С и с
2
= 1,0 мм
- для остальных трубопроводов.
В качестве основных элементов трубопровода, подлежащих контрольному расчёту на прочность, следует принимать прямые
трубы, колена, тройники и переходы.
8.8.10 Для трубопроводов с температурой эксплуатации выше 250 ° С при выявлении отклонений и дефектов в ОПС и
отклонений от проекта в трассировке требуется проведение поверочного расчета с учётом всего комплекса нагружающих
факторов (на прочность и самокомпенсацию).
8.8.11 Поверочный расчёт на циклическую прочность выполняется для гибов трубопроводов питательной воды (установок
среднего давления), а также для гибов остальных трубопроводов, если по результатам их контроля на внутренней поверхности
металла обнаружены дефекты коррозионно-механического происхождения. Расчёт на циклическую прочность выполняется с
учётом коррозионного фактора среды.
8.8.12 При интенсивной местной или общей коррозии металла трубопровода (фактическая средняя скорость коррозии
превышает 0,1 мм/год) следует выполнить расчёт на прочность по минимальной фактической толщине стенки с учётом её
последующего утонения на конец планируемого
срока эксплуатации.
Если по результатам такого расчёта нормативные условия прочности не выполняются для каких-либо элементов,
поражённых локальной (язвенной) коррозией, допускается производить расчёт по фактической среднеинтегральной толщине
стенки элемента. В этом случае выбор расчётной методики и выполнение расчётов относится к компетенции
специализированной организации.
8.8.13 Необходимость проведения определенного вида расчета и его методика могут быть уточнены в каждом конкретном
случае специализированной организацией.
8.8.14 Возможность, сроки и условия дальнейшей эксплуатации трубопроводов следует определять по результатам контроля
и расчетов на прочность.
Необходимым условием возможности дальнейшей безопасной эксплуатации трубопровода при расчетных или разрешенных
параметрах является соответствие элементов трубопровода условиям прочности, а также выполнение обязательных требований
пунктов 7.2.1
и 7.2.5 настоящего стандарта.
8.8.15 Если по условиям прочности при статическом нагружении отдельные элементы или узлы трубопровода из-за утонения
стенок от коррозии, эрозии или каких либо других повреждений, а также из-за снижения механических свойств основного
металла или сварных соединений или пониженных запасов прочности не выдерживают расчётное давление и температуру,
продление срока эксплуатации возможно после
восстановительного ремонта или замены элементов (узлов), не
удовлетворяющих условиям прочности, или при установлении дополнительных требований к условиям эксплуатации
трубопровода, включая параметры его работы, а также контроль и проверку состояния трубопровода в процессе разрешённого
срока эксплуатации.
Для трубопроводов из стали 20, работающих при температуре выше 350 °С, допускается продление срока эксплуатации при
пониженных коэффициентах запаса прочности. При этом фактические коэффициенты запаса прочности должны быть не ниже
1,35, а допускаемый срок продления в этом случае должен быть сокращён в зависимости от конкретных значений коэффициент
запаса прочности и фактического состояния металла по результатам контроля и исследований.
8.8.16 Трубопровод считается пригодным к дальнейшей эксплуатации, если по результатам его обследования
подтверждается, что состояние основного и наплавленного металла удовлетворяет требованиям настоящего стандарта и
действующей нормативной документации; коррозионный и эрозионный износ, а также изменения в состоянии трассы и
геометрических размеров элементов трубопровода обеспечивают нормативные запасы прочности.
При необходимости оценки остаточного ресурса трубопроводов с учётом цикличности нагружения (п. 8.8.11) или коррозии
металла (п. 8.8.12
), а также для трубопроводов с температурой эксплуатации 390 °С и более допускаемый срок продления
эксплуатации трубопровода устанавливается на основании результатов расчётов на прочность с учётом этих факторов.
8.8.17 Контролируемый трубопровод может быть допущен к дальнейшей эксплуатации сроком не более, чем на 8 лет, а для
трубопроводов с температурой выше 350 °С - не более, чем на 50 тыс. часов, на основании положительных результатов
контроля,
асчетов на прочность и гидравлических испытаний при соблюдении установленных требований по условиям
(регламенту) пуска и эксплуатации трубопровода, а также рекомендаций заключения по итогам обследования.
8.8.18 По истечению дополнительно назначенного срока службы трубопровода, установленного по результатам первичного
(предыдущего) диагностирования, следует провести очередной (повторный) контроль (диагностирование) трубопровода для
определения возможности, условий и срока его дальнейшей эксплуатации. Программа последующего (повторного)
диагностирования может отличаться от программы предыдущего технического диагностирования трубопровода.
8.9. Сосуды, работающие под давлением
Введено с 30.06.2008СТО 17230282.27.100.005-2008 Основные элементы котлов, т
рбин и тр
б
...
NormaCS® (NRMS10-05534) www.normacs.ru 15.07.2010 Стр. 195 из 261