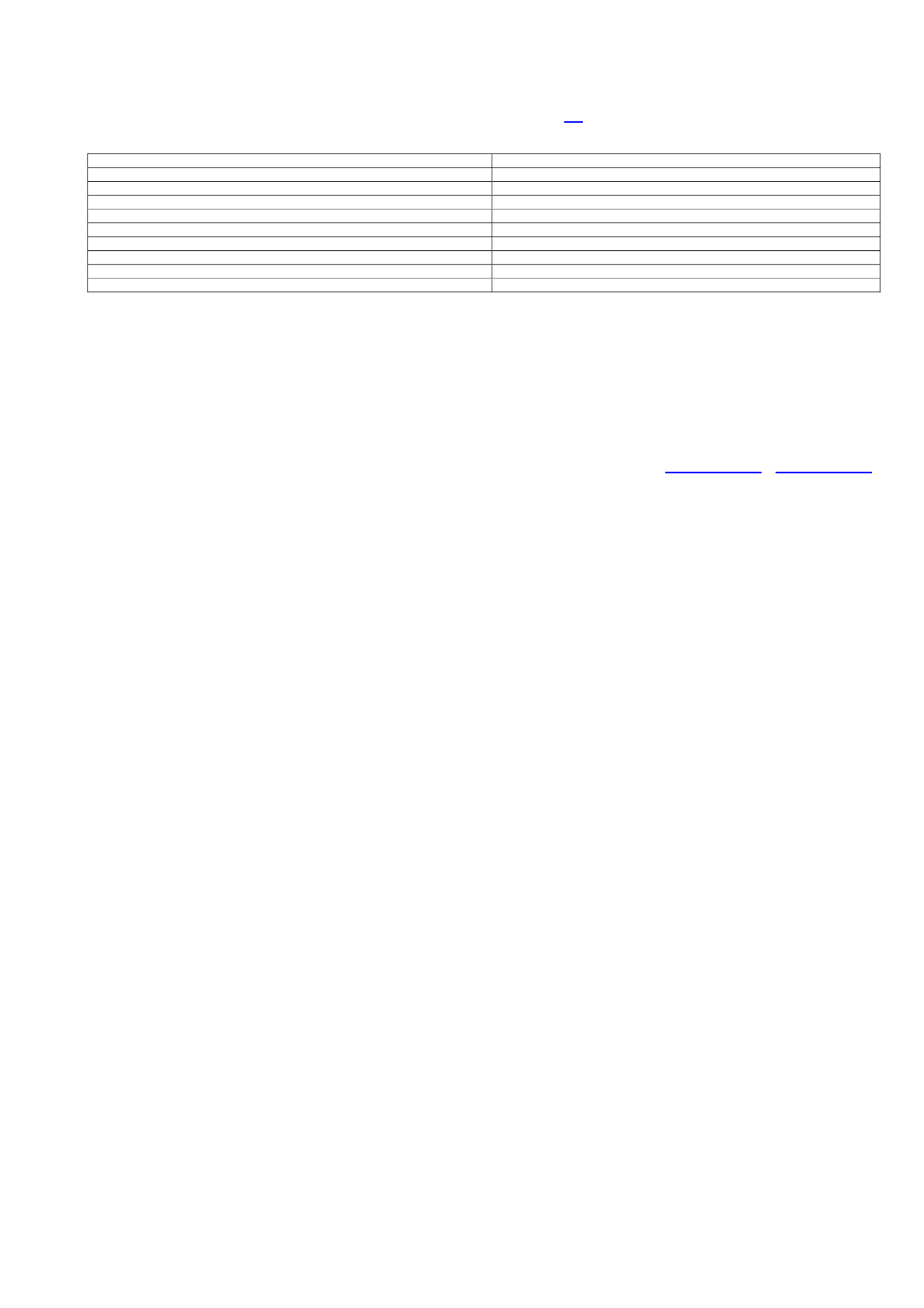
- а также другие измерительные средства.
4.2.1.12 Допускается применение новых средств визуального и измерительного контроля при условии наличия
соответствующих инструкций, методик их применения с использованием специальных приборов и методов измерения, в том
числе оптических, механических, гидростатических, радиотехнических, лазерных, телевизионных и прочих при условии
обеспечения погрешности измерения не более величин, указанных в таблице 4.1
.
Таблица 4.1 - Допустимая погрешность измерений при измерительном контроле
4.2.1.13 Измерительные приборы и инструменты должны периодически, а также после ремонта проходить поверк
(калибровку) в метрологических службах, аккредитованных Ростехрегулированием. Срок проведения поверки (калибровки)
устанавливается нормативной документацией на соответствующие приборы и инструменты, средства измерения.
4.2.2 Ультразвуковой контроль
4.2.2.1 Общие положения
Ультразвуковой контроль применяется при монтаже, ремонте (реконструкции) и эксплуатации тепловых электростанций,
также при техническом диагностировании оборудования для выявления дефектов основного и наплавленного (сварных
соединений) металла, возникающих при изготовлении (монтаже и ремонте) или при эксплуатации, а также для измерения
толщины стенки (толщинометрии) деталей.
Основные положения, касающиеся метода ультразвукового контроля металла, изложены в ГОСТ 12503-75 и ГОСТ 14782-86.
а) Ультразвуковому контролю подвергаются следующие элементы и детали тепломеханического оборудования (объекты
контроля - ОК), изготовленные из сталей перлитного и мартенситно-ферритного классов (кроме литья):
- основной метал гнутых участков (гибов) трубопроводов толщиной от 3,5 мм и диаметром от 57 мм;
- наружная и внутренняя поверхность корпусов пароохладителей и пусковых впрысков, в том числе в местах врезки
впрыскивающих устройств;
- наружная и внутренняя поверхность камер коллекторов и труб в местах врезки штуцеров, дренажных линий и т.п.;
- основной металл и резьбовая поверхность деталей крепежа (шпильки, болты) диаметром более М30;
- металл цельнокованых роторов высокого и среднего давления паровых и газовых турбин;
- металл валов роторов среднего и низкого давления;
- металл насадных дисков;
- металл рабочих лопаток паровых турбин;
- стыковые кольцевые (поперечные) сварные соединения трубопроводов, коллекторов и труб поверхностей теплообмена с
толщиной стенки от 2 мм до 120 мм и более, и диаметром более 10 мм;
- продольные и спиральные стыковые сварные соединения трубопроводов с толщиной стенки от 6 мм и более;
- стыковые кольцевые и продольные сварные соединения обечаек и днищ барабанов и сосудов;
- кольцевые угловые сварные соединения с полным проплавлением с толщиной стенки от 4,5 мм;
- стыковые кольцевые сварные соединения труб поверхностей теплообмена из сталей аустенитного класса;
- наплавки на участках ремонта сварных соединений или на основном металле элементов.
б) Ультразвуковой толщинометрии подвергаются следующие элементы и детали тепломеханического оборудования,
изготовленные из сталей перлитного и мартенситно-ферритного классов:
- участки трубопроводов, коллекторов и труб поверхностей теплообмена, а также дренажных и сбросных трубопроводов;
- участки патрубков за арматурой (задвижками, отсечными и регулирующими клапанами и т.п.) и дросселирующими
устройствами;
- гнутые участки трубопроводов (гибы) в растянутой и нейтральной части;
- барабаны котлов;
- сосуды, работающие под давлением;
- корпусные детали турбин и арматуры (по специальной методике).
Примечание - При толщинометрии определяется соответствие толщины стенок элементов прочностным расчетам, выявляются участки
коррозионных и эрозионных поражений и определяется величина утонения.
4.2.2.2. Участок ультразвукового контроля
а) Участок (группа) ультразвукового контроля входит в состав лаборатории неразрушающего контроля (лаборатории
металлов).
б) Участок должен быть оснащен соответствующей аппаратурой и принадлежностями. Персонал, проводящий
ультразвуковой контроль, должен быть обучен и аттестован в установленном порядке.
в) В приложении к «Свидетельству об аттестации» лаборатории (в видах контроля) должен быть указан ультразвуковой
контроль и ультразвуковая толщинометрия и перечислено оборудование, на котором допускается его применение.
4.2.2.3 Требование к аппаратуре
а) В дефектоскопии тепломеханического оборудования ТЭС применяется импульсный эхо метод ультразвукового контроля и
используется следующая аппаратура и принадлежности:
- ультразвуковые дефектоскопы;
- ультразвуковые толщиномеры;
- ультразвуковые преобразователи;
- стандартные образцы;
- вспомогательные приспособления и оснастка для контроля;
- диаграммы, шкалы и таблицы для расшифровки результатов контроля.
б) Ультразвуковые дефектоскопы и толщиномеры (отечественные или иностранные) должны иметь Технический Паспорт и
Сертификат соответствия («сертификат об утверждении средства измерения») и ежегодно поверяться аккредитованной
метрологической организацией.
Диапазон измеряемой величины, мм Погрешность измерений, мм
1 2
До 0,5 включительно 0,1
Свыше 0,5 до 1,0 включительно 0,2
Свыше 1,0 до 1,5 включительно 0,3
Свыше 1,5 до 2,5 включительно 0,4
Свыше 2,5 до 4,0 включительно 0,5
Свыше 4,0 до 6,0 включительно 0,6
Свыше 6,0 до 10,0 включительно 0,8
Свыше 10,0 1,0
Введено с 30.06.2008СТО 17230282.27.100.005-2008 Основные элементы котлов, т
рбин и тр
б
...
NormaCS® (NRMS10-05534) www.normacs.ru 15.07.2010 Стр. 11 из 261