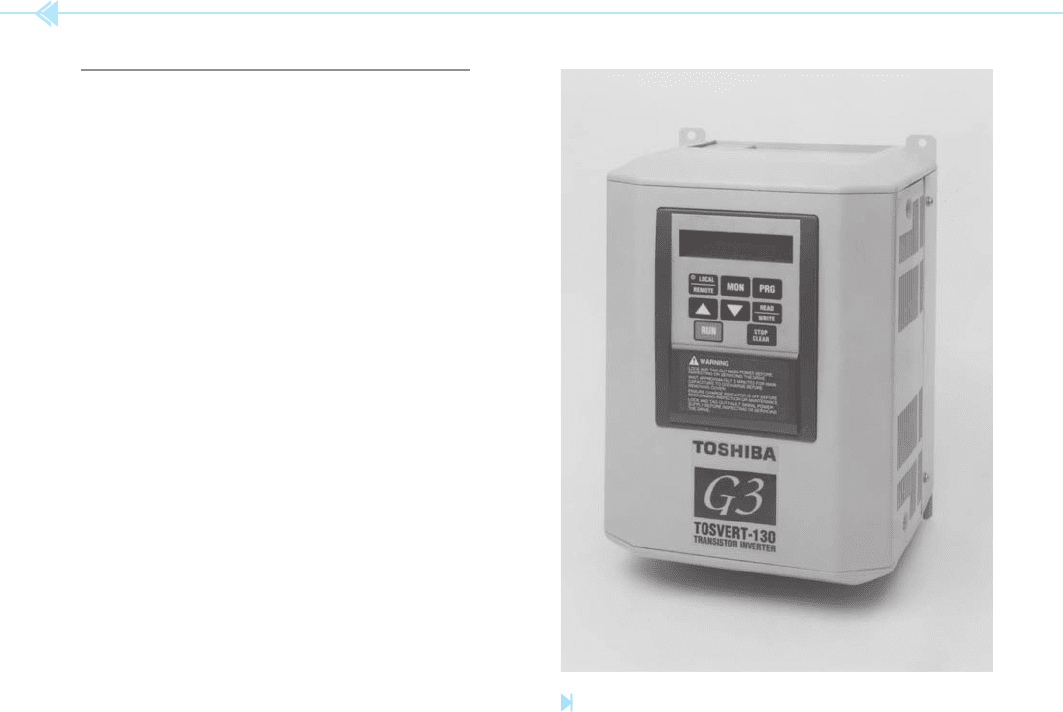
138 SECTION 3 Motors
unit converts the DC voltage back into three-phase
alternating current by turning transistors on or off at
the proper time and in the proper sequence. Assume,
for example, that transistors Q1 and Q4 are switched
on at the same time. This permits stator winding T
1
to be connected to a positive voltage and T
2
to be
connected to a negative voltage. Current can ow
through Q4 to T
2
, through the motor stator winding
and through T
1
to Q1.
Now assume that transistors Q1 and Q4 are
switched off and transistors Q3 and Q6 are switched
on. Current will now ow through Q6 to stator
winding T
3
, through the motor to T
2
, and through
Q3 to the positive of the power supply.
Because the transistors are turned completely
on or completely off, the waveform produced is a
square wave instead of a sine wave, Figure 13–7.
Induction motors will operate on a square wave
VARIABLE FREQUENCY DRIVES
One of the factors that determines the speed of the
rotating magnetic eld of an AC induction motor is
the frequency of the applied voltage. If the frequency
is changed, the speed of the rotating magnetic eld
changes also. A four-pole stator will have a synchro-
nous speed (speed of the rotating magnetic eld) of
1,800 RPM when connected to a 60-Hz line. If the
frequency is lowered to 30 Hz, the synchronous
speed decreases to 900 RPM.
When the frequency is lowered, care must be
taken not to damage the stator windings. The
current ow through the winding is limited to a
great extent by inductive reactance. When the fre-
quency is lowered, inductive reactance is lowered
also (X
L
⫽ 2πFL). For this reason, variable fre-
quency drives must employ some method of lower-
ing the applied voltage to the stator as frequency is
reduced.
In the air conditioning
eld, variable frequency
drive is often used to control the speed of blower
motors. This method of controlling air ow can be
more ef cient than inserting dampers into the duct
system. Variable frequency drives are very popular
in zone controlled systems.
Most variable frequency drives operate by rst
changing the AC voltage into DC and then changing
it back to AC at the desired frequency. A variable fre-
quency drive is shown in Figure 13–5. There are sev-
eral methods used to change the DC voltage back into
AC. The method employed is generally determined
by the manufacturer, age of the equipment, and the
size motor the drive must control. Variable frequency
drives intended to control the speed of motors up
to 500 horsepower generally use transistors. In
the circuit shown in Figure 13–6, a three-phase
bridge changes the three-phase alternating-current
into direct current. The bridge recti er uses
SCRs
(silicon
controlled recti ers) instead of
diodes. The SCRs permit the output voltage of the
recti
er to be controlled. As the frequency decreases,
the SCRs re later in the cycle and lower the output
voltage to the transistors. A choke coil and capaci-
tor bank are used to lter the output voltage before
transistors Q1 through Q6 change the DC voltage
back into AC. An electronic control unit is connected
to the bases of transistor Q1 through Q6. The control
Figure 13–5
Variable frequency drive. (Courtesy of Toshiba Corp.).