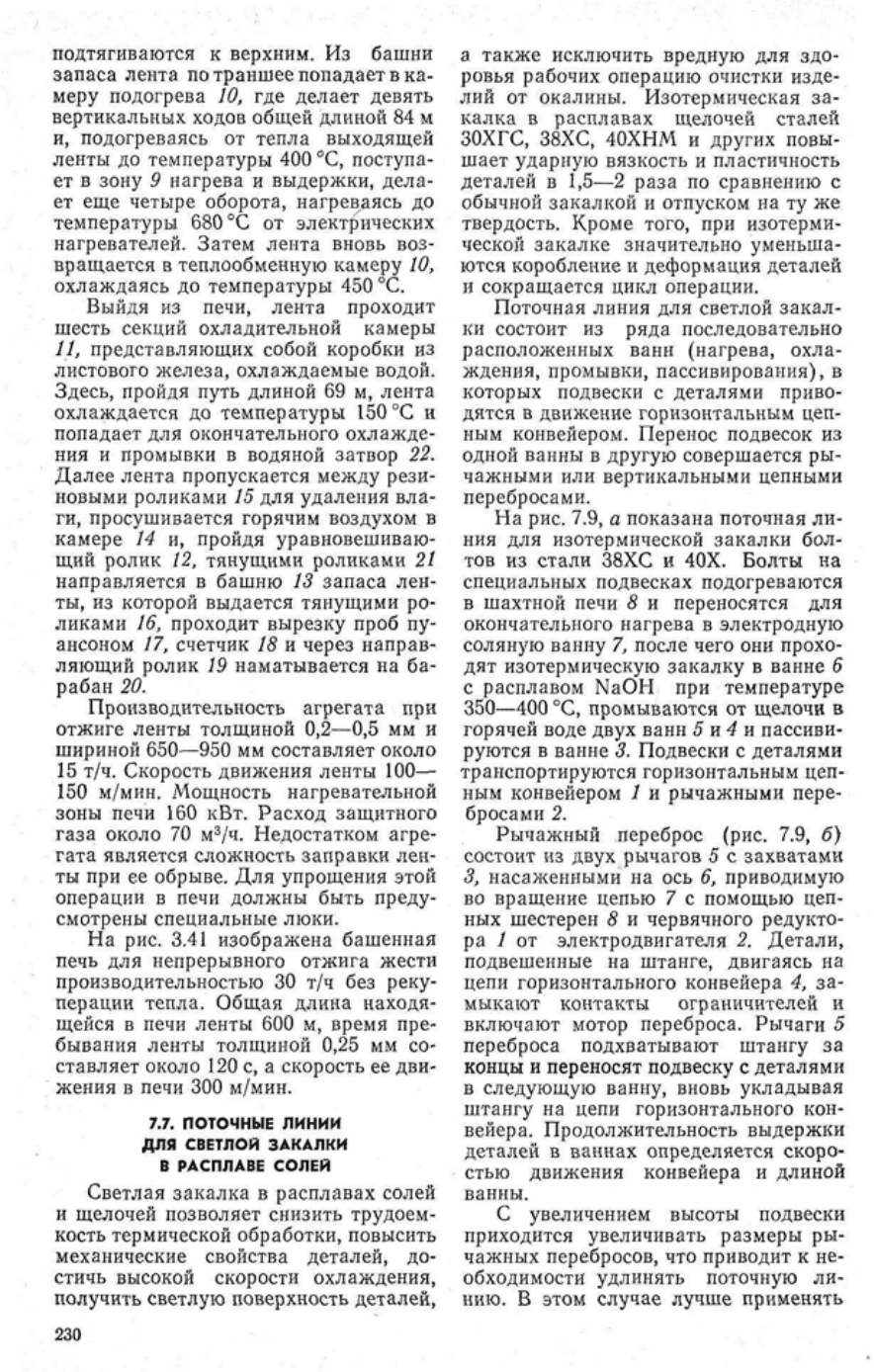
подтягиваются к верхним. Из башни
запаса лента по траншее попадает в ка-
меру подогрева 10, где
делает
девять
вертикальных
ходов
общей длиной 84 м
и,
подогреваясь от тепла выходящей
ленты до температуры 400 °С, поступа-
ет в зону 9 нагрева и выдержки, дела-
ет еще четыре оборота, нагреваясь до
температуры 680 °С от электрических
нагревателей. Затем лента вновь воз-
вращается в теплообменную камеру 10,
охлаждаясь до температуры 450 °С.
Выйдя из печи, лента проходит
шесть секций охладительной камеры
11,
представляющих собой коробки из
листового железа, охлаждаемые водой.
Здесь, пройдя путь длиной 69 м, лента
охлаждается до температуры 150 °С и
попадает для окончательного охлажде-
ния
и промывки в водяной затвор 22.
Далее лента пропускается
между
рези-
новыми
роликами 15 для удаления вла-
ги,
просушивается горячим
воздухом
в
камере 14 и, пройдя уравновешиваю-
щий
ролик 12, тянущими роликами 21
направляется в башню 13 запаса лен-
ты, из которой выдается тянущими ро-
ликами
16, проходит вырезку проб пу-
ансоном
17, счетчик 18 и через направ-
ляющий
ролик 19 наматывается на ба-
рабан 20.
Производительность агрегата при
отжиге ленты толщиной
0,2—0,5
мм и
шириной
650—950
мм составляет около
15 т/ч. Скорость движения ленты 100—
150 м/мин. Мощность нагревательной
зоны
печи 160 кВт. Расход защитного
газа около 70 м
3
/ч. Недостатком агре-
гата
является сложность заправки лен-
ты при ее обрыве. Для упрощения этой
операции
в печи должны быть преду-
смотрены специальные люки.
На
рис. 3.41 изображена башенная
печь для непрерывного отжига жести
производительностью 30 т/ч без реку-
перации
тепла. Общая длина находя-
щейся
в печи ленты 600 м, время пре-
бывания
ленты толщиной 0,25 мм со-
ставляет около 120 с, а скорость ее дви-
' жения в печи 300 м/мин.
7.7.
ПОТОЧНЫЕ
ЛИНИИ
ДЛЯ
СВЕТЛОЙ
ЗАКАЛКИ
В РАСПЛАВЕ
СОЛЕИ
Светлая закалка в расплавах солей
и
щелочей позволяет снизить трудоем-
кость термической обработки, повысить
механические свойства деталей, до-
стичь высокой скорости охлаждения,
получить
светлую
поверхность деталей,
а также исключить вредную для здо-
ровья рабочих операцию очистки изде-
лий
от окалины. Изотермическая за-
калка
в расплавах щелочей сталей
ЗОХГС, 38ХС, 40ХНМ и
других
повы-
шает
ударную
вязкость и пластичность
деталей в 1,5—2 раза по сравнению с
обычной закалкой и отпуском на ту же.
твердость. Кроме того, при изотерми-
ческой закалке значительно уменьша-
ются коробление и деформация деталей
и
сокращается цикл операции.
Поточная
линия для светлой закал-
ки
состоит из ряда последовательно
расположенных ванн (нагрева,
охла-
ждения,
промывки, пассивирования), в
которых подвески с деталями приво-
дятся в движение горизонтальным цеп-
ным
конвейером. Перенос подвесок из
одной
ванны в
другую
совершается ры-
чажными или вертикальными цепными
перебросами.
На
рис. 7.9, а показана поточная ли-
ния
для изотермической закалки бол-
тов из стали
38ХС
и 40Х. Болты на
специальных подвесках подогреваются
в
шахтной печи 8 и переносятся для
окончательного нагрева в электродную
соляную ванну 7, после чего они прохо-
дят изотермическую закалку в ванне 6
с расплавом NaOH при температуре
350—400
°С, промываются от щелочи в
горячей воде
двух
ванн 5 и 4 и пассиви-
руются в ванне 3. Подвески с деталями
транспортируются горизонтальным цеп-
ным
конвейером 1 и рычажными пере-
бросами 2.
Рычажный
переброс (рис. 7.9, б)
состоит из
двух
рычагов 5 с захватами
3, насаженными на ось 6, приводимую
во вращение цепью 7 с помощью цеп-
ных шестерен 8 и червячного редукто-
ра 1 от электродвигателя 2. Детали,
подвешенные на штанге, двигаясь на
цепи
горизонтального конвейера 4, за-
мыкают контакты ограничителей и
включают мотор переброса. Рычаги 5
переброса подхватывают штангу за
концы
и
переносят
подвеску с деталями
в
следующую
ванну, вновь укладывая
штангу на цепи горизонтального кон-
вейера. Продолжительность выдержки
деталей в ваннах определяется скоро-
стью движения конвейера и длиной
ванны.
С
увеличением высоты подвески
приходится увеличивать размеры ры-
чажных перебросов, что приводит к не-
обходимости удлинять поточную ли-
нию.
В этом
случае
лучше применять
230