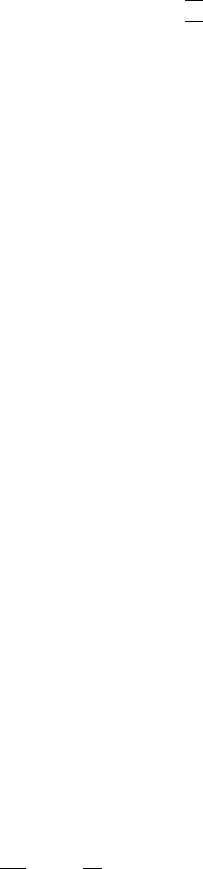
1 c
2
T ln
d
dt
c
3
0
B
@
1
C
A
2
6
4
3
7
5
3
c
1
G
x
p
11:13
where x is the atomic fraction of carbon. c
i
are material parameters (Engberg and
Carlsson 2002).
Static strain ageing in ferritic steels gives rise to the Lu
È
ders' strain during
tensile testing. The localisation of strain to the band(s) gives local strain rates
much in excess of the nominal ones. The sharper the plastic front, caused, for
example, by a finer grain size where the indivi dual grain boundaries constitute
barriers for front movement, the higher the strain rate and consequently the
higher is the yield stress and the yield elongation. With an increased nominal
strain rate the yield stress increase is larger than what is obtained during
homogeneous deformation (see, for example, Yoshitake et al. 1996). This is of
importance, for example, during skin-pass rollin g, where commonly a fixed total
elongation is prescribed, at accelerations or decelerations giving rise to
substantial changes in needed roll force.
11.3.2 Warm to hot working temperatures
Above around 0.3 T
m
recovery by cross-slip mechanisms are thought to occur
and above 0.5 T
m
climb becomes significant. This has a very significant effect on
the temperature and strain-rate dependency of the flow stress. Also, recrystal-
lisation will become of importance. The dislocation generation mechanisms will
remain as given above. It has, however, been suggested that the generation of
point defects, vacancies, due to cutting of forest dislocations or other dislocation
interactions can be of importance as this will increase the diffusivity. One classic
example of this effect is found in dynamic strain ageing of substitutional alloys.
In Fig. 11.3 one example of the phenomenon is shown for a 316-austenitic
stainless steel deformed at 400ëC. The effect increases with strain as more
vacancies are created and the diffusivity increases.
The generation of vacancies is also counteracted by diffusion to various
sinks, such as dislocations, grain boundaries, etc. A simple description is given
by
dx
v
dt
c
1
b
d
dt
p
ÿ c
2
D
m
x
v
x
v
ÿ x
v0
p
11:14
where x
v
is the vacancy conce ntration, x
v0
the same at thermal equilibrium, D
m
the migration part of the diffusion coefficient and c
i
are material parameters
(Siwecki and Engberg 1997). The first term on the right-hand side gives the
generation and the second term the annihilation of vacancies.
Recrystallisation is traditionally described by a JMAK (Johnson-Mehl,
Awrami, Kolmogorov) type expression combined with regression formulas for
Analysing metal working processes 459