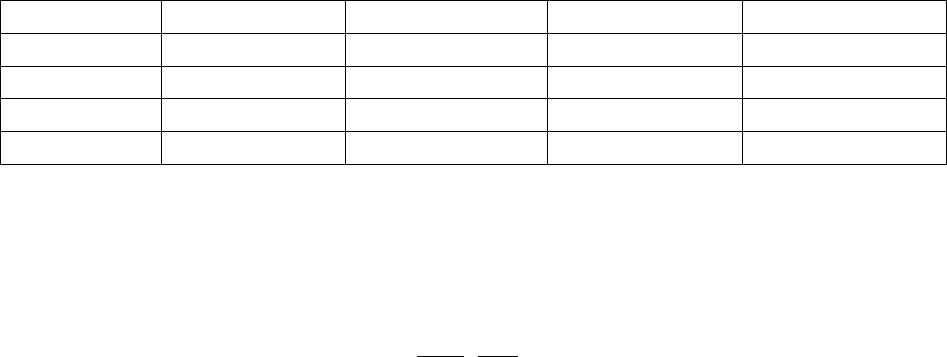
Секция 2. Листопрокатное производство
173
основе положены методы теории вероятностей, математической, статистики и классификации
альтернативных вариантов, которые достаточно подробно рассмотрены в работах [6, 8, 9].
Энергосиловые параметры рассчитываются по математическим моделям с учетом
прочностных свойств металла, и производится их сравнение с допустимыми значениями. По
результатам анализа принимается решение о выборе режима прокатки. Информация
подтверждается оператором ГПУ и передается на стан холодной прокатки.
В результате использования данной методики для поиска наилучших технологических
факторов холодной прокатки достигается высокая надежность и точность результатов за счет
значительного сужения границ поиска, путем выделения характеристик групп режимов и выбора
наилучшей группы, внутри которой происходит выбор наилучшего технологического режима.
Ниже приведен пример практического использования методики, согласно которой
рассчитан и реализован режим холодной прокатки полос изотропной электротехнической стали
(ЭИС) четвертой группы легирования (типоразмер 2,0→0,5×1065 мм) на 4-хклетьевом стане 1400.
Данная сталь с высоким содержанием кремния (порядка 3%) отличается повышенной твердостью
и хрупкостью, что оказывает негативное влияние на стабильность процесса прокатки, которое
заключается в частых обрывах полосы и преждевременном выходе из строя рабочих валков.
При формировании исходной базы данных использовали информацию о горячекатаных
рулонах с подобным уровнем механических свойств и геометрических параметров, данные о
режимах прокатки только для установившегося процесса, при незначительном отклонении
значений уставок СРП от среднего значения.
Проведен выбор наилучшего режима прокатки. В качестве технологических параметров
обработки металла на стане холодной прокатки использовали режим обжатий (ε
1
, ε
2
, ε
3
, ε
4
,) и
режим натяжений (σ
Р
, σ
1-2
, σ
2-3
, σ
3-4
, σ
М
), а в качестве критериев оптимизации выбрали скорость
прокатки и удельный расход энергии. Определение границ поддиапазонов производили с
помощью кластерного анализа данных.
Кластерный анализ проводили только для режима обжатий (ε
1
, ε
2
, ε
3
, ε
4
,), режим натяжений
(σ
Р
, σ
1-2
, σ
2-3
, σ
3-4
, σ
М
) в анализе не участвовал, ввиду недостаточной степени изменчивости. В
результате кластерного анализа данных выявлено 4 кластера режимов обжатий (рис. 1, табл. 1).
Таблица 1. Кластеры режимов обжатий динамной стали.
№ кластера ε
1
, % ε
2
, % ε
3
, % ε
4
, %
1 17,15 – 31,25 20,43 – 34,25 18,45 – 33,33 23,06 – 42,95
2 21,30 – 30,50 21,03 – 29,95 30,19 – 37,93 24,14 – 33,97
3 22,75 – 34,45 26,24 – 36,55 23,91 – 33,67 20,16 – 31,23
4 20,60 – 38,88 14,75 – 32,66 25,96 – 45,45 29,14 – 48,55
Выбор наилучшего кластера режима прокатки производили с точки зрения минимального
образования основных видов дефектов валков. Результаты расчета приведены ниже:
Кластер №1 Кластер №2 Кластер №3 Кластер №4
p
i
0,128446 0,027817 0,030600 0,086947
где p
i
– показатель дефектности, который определяется по формуле:
J
j
v
vp
деф
реж
i
деф
ii
⋅⋅=
1
, (1)
где p
i
– показатель дефектности i-го вида режима прокатки;
ν
i
деф
– относительная частота образования дефектов по i-му режиму прокатки;
ν
i
реж
– относительная частота реализации i-го вида режима прокатки;
j
деф
– количество рассматриваемых видов дефектов;