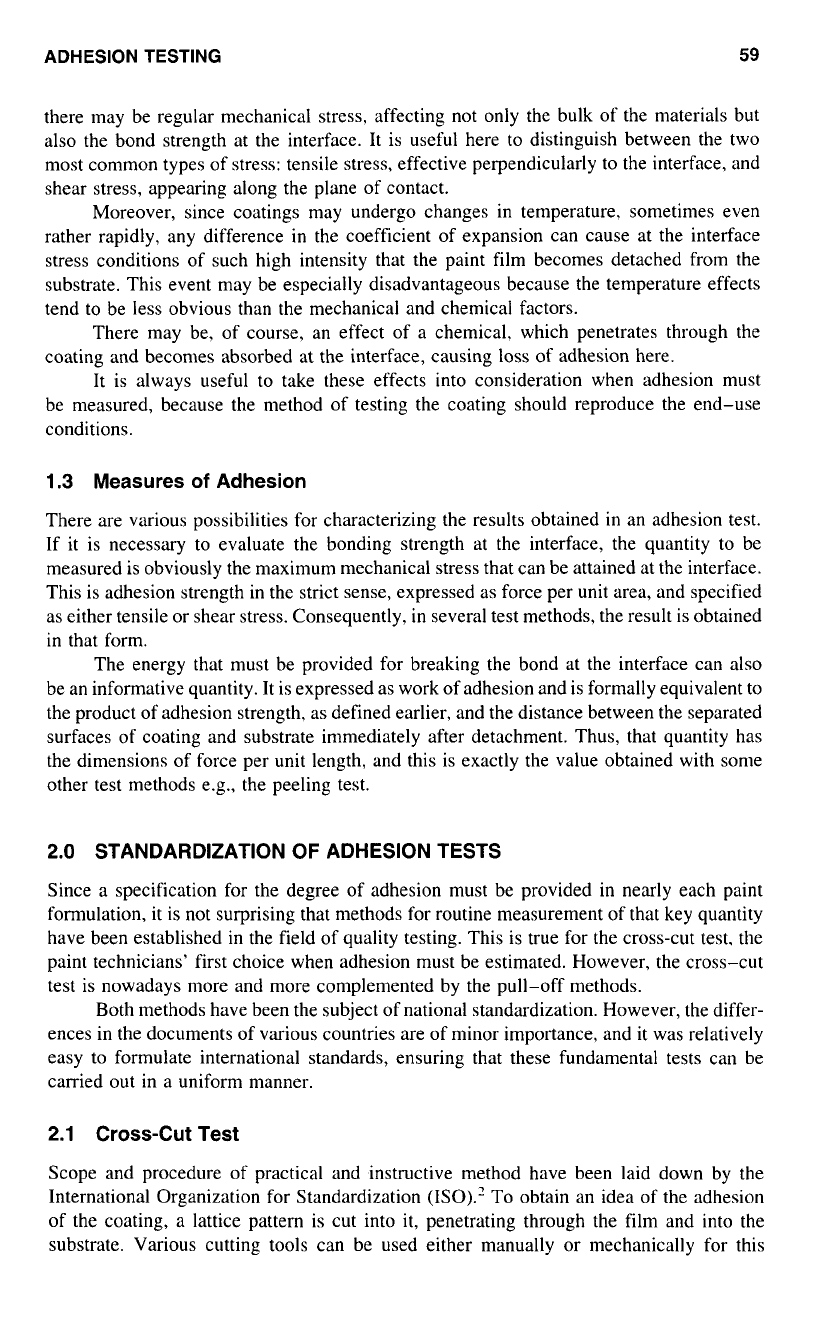
ADHESION TESTING
59
there may be regular mechanical stress, affecting not only the bulk of the materials but
also the bond strength at the interface. It is useful here
to
distinguish between the two
most common types of stress: tensile stress, effective perpendicularly to the interface, and
shear stress, appearing along the plane
of
contact.
Moreover, since coatings may undergo changes in temperature, sometimes even
rather rapidly, any difference in the coefficient
of
expansion can cause at the interface
stress conditions of such high intensity that the paint film becomes detached from the
substrate. This event may be especially disadvantageous because the temperature effects
tend to be less obvious than the mechanical and chemical factors.
There may be, of course, an effect of
a
chemical, which penetrates through the
coating and becomes absorbed at the interface, causing
loss
of adhesion here.
It is always useful to take these effects into consideration when adhesion must
be measured, because the method of testing the coating should reproduce the end-use
conditions.
1.3
Measures
of
Adhesion
There are various possibilities for characterizing the results obtained in an adhesion test.
If it is necessary to evaluate the bonding strength at the interface, the quantity to be
measured
is
obviously the maximum mechanical stress that can be attained at the interface.
This is adhesion strength in the strict sense, expressed
as
force per unit area, and specified
as
either tensile or shear stress. Consequently, in several test methods, the result is obtained
in that form.
The energy that must be provided for breaking the bond at the interface can
also
be an informative quantity. It is expressed
as
work
of
adhesion and is formally equivalent to
the product of adhesion strength,
as
defined earlier, and the distance between the separated
surfaces of coating and substrate immediately after detachment. Thus, that quantity has
the dimensions
of
force per unit length, and this is exactly the value obtained with some
other test methods e.g., the peeling test.
2.0
STANDARDIZATION
OF
ADHESION TESTS
Since
a
specification for the degree of adhesion must be provided in nearly each paint
formulation, it is not surprising that methods for routine measurement of that key quantity
have been established in the field of quality testing. This is true for the cross-cut test. the
paint technicians’ first choice when adhesion must be estimated. However, the cross-cut
test is nowadays more and more complemented by the pull-off methods.
Both methods have been the subject of national standardization. However, the differ-
ences in the documents of various countries are of minor importance, and it was relatively
easy to formulate international standards, ensuring that these fundamental tests can be
carried out in a uniform manner.
2.1
Cross-Cut Test
Scope and procedure of practical and instructive method have been laid down by the
International Organization for Standardization
(ISO).’
To obtain an idea of the adhesion
of the coating,
a
lattice pattern is cut into it, penetrating through the film and into the
substrate. Various cutting tools can be used either manually or mechanically for this