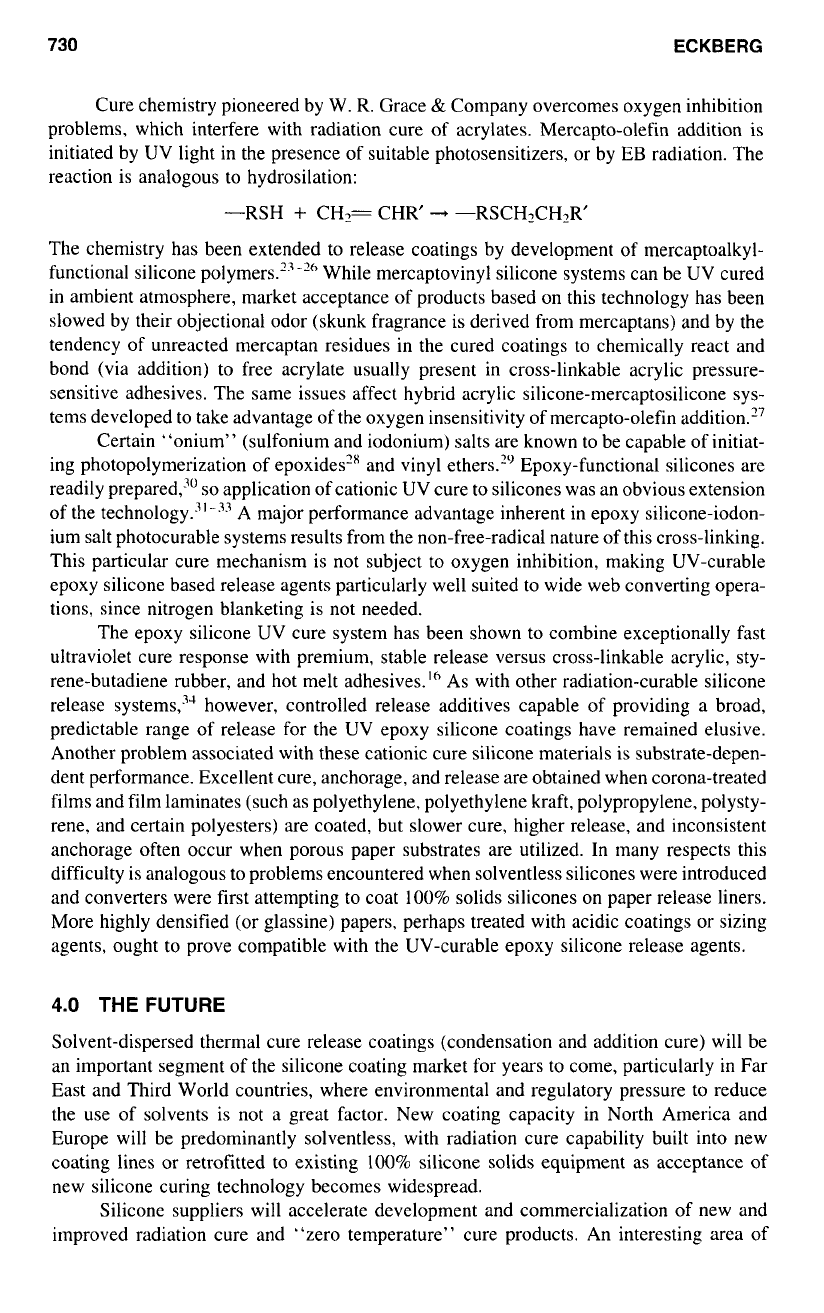
730
ECKBERG
Cure chemistry pioneered by W. R. Grace
&
Company overcomes oxygen inhibition
problems, which interfere with radiation cure of acrylates. Mercapto-olefin addition is
initiated by UV light in the presence of suitable photosensitizers, or by EB radiation. The
reaction is analogous to hydrosilation:
“RSH
+
CH?= CHR’
-+
-RSCH,CH?R’
The chemistry has been extended to release coatings by development
of
mercaptoalkyl-
functional silicone While mercaptovinyl silicone systems can be UV cured
in ambient atmosphere, market acceptance of products based on this technology has been
slowed by their objectional odor (skunk fragrance is derived from mercaptans) and by the
tendency of unreacted mercaptan residues in the cured coatings to chemically react and
bond (via addition) to free acrylate usually present in cross-linkable acrylic pressure-
sensitive adhesives. The same issues affect hybrid acrylic
silicone-mercaptosilicone
sys-
tems developed to take advantage of the oxygen insensitivity of mercapto-olefin addition.”
Certain “onium” (sulfonium and iodonium) salts are known to be capable of initiat-
ing photopolymerization of epoxides” and vinyl ethers.‘” Epoxy-functional silicones are
readily prepared,3”
so
application of cationic UV cure
to
silicones was an obvious extension
of the A major performance advantage inherent in epoxy silicone-iodon-
ium salt photocurable systems results from the non-free-radical nature of this cross-linking.
This particular cure mechanism is not subject to oxygen inhibition, making UV-curable
epoxy silicone based release agents particularly well suited to wide web converting opera-
tions, since nitrogen blanketing is not needed.
The epoxy silicone UV cure system has been shown to combine exceptionally fast
ultraviolet cure response with premium, stable release versus cross-linkable acrylic, sty-
rene-butadiene rubber, and hot melt adhesives.I6 As with other radiation-curable silicone
release systems,” however, controlled release additives capable of providing
a
broad,
predictable range of release for the UV epoxy silicone coatings have remained elusive.
Another problem associated with these cationic cure silicone materials is substrate-depen-
dent performance. Excellent cure, anchorage, and release are obtained when corona-treated
films and film laminates (such
as
polyethylene, polyethylene kraft, polypropylene, polysty-
rene, and certain polyesters) are coated, but slower cure, higher release, and inconsistent
anchorage often occur when porous paper substrates are utilized. In many respects this
difficulty is analogous to problems encountered when solventless silicones were introduced
and converters were first attempting to coat
100%
solids silicones on paper release liners.
More highly densified (or glassine) papers, perhaps treated with acidic coatings or sizing
agents, ought to prove compatible with the UV-curable epoxy silicone release agents.
4.0
THE
FUTURE
Solvent-dispersed thermal cure release coatings (condensation and addition cure) will be
an important segment of the silicone coating market for years to come, particularly in Far
East and Third World countries, where environmental and regulatory pressure to reduce
the use of solvents is not
a
great factor. New coating capacity in North America and
Europe will be predominantly solventless, with radiation cure capability built into new
coating lines or retrofitted to existing
100%
silicone solids equipment
as
acceptance of
new silicone curing technology becomes widespread.
Silicone suppliers will accelerate development and commercialization
of
new and
improved radiation cure and “zero temperature” cure products. An interesting area
of