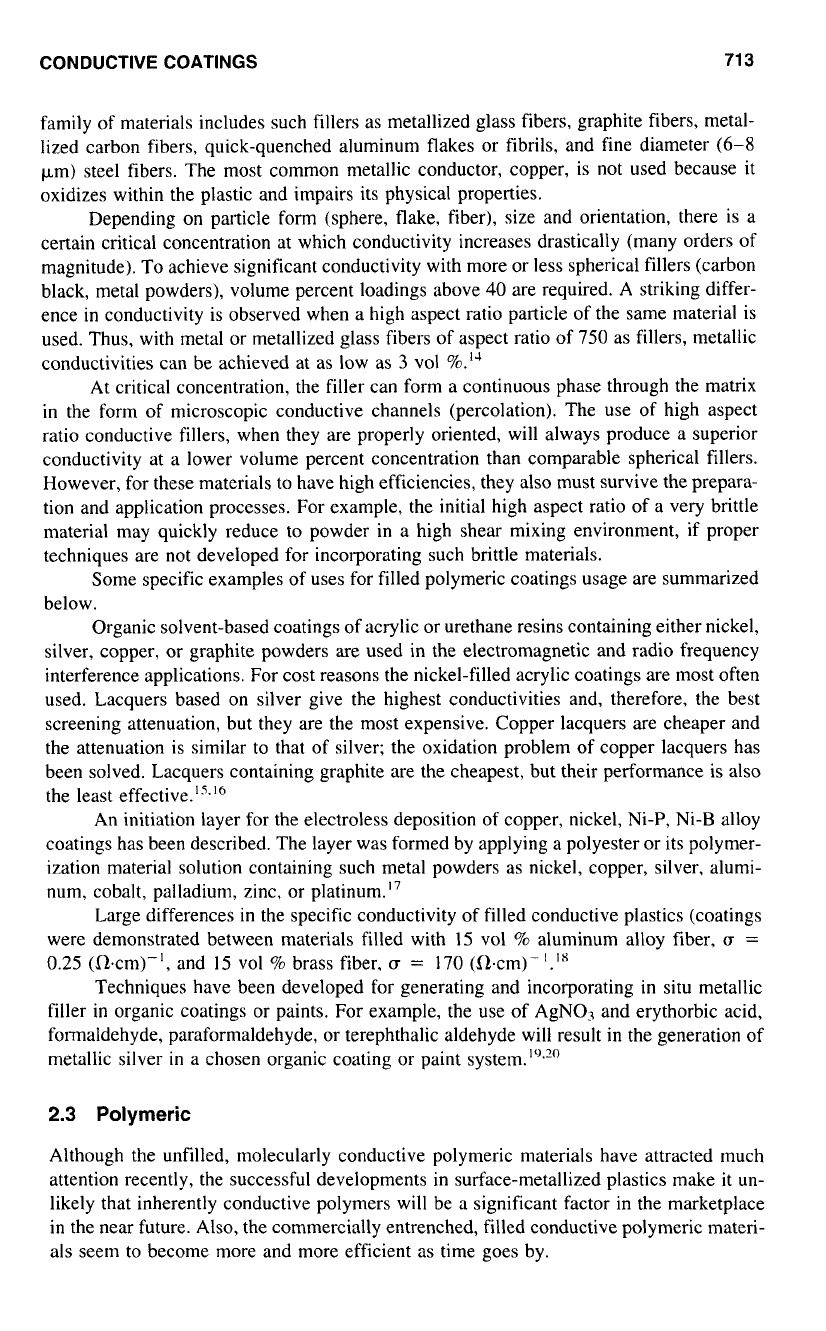
CONDUCTIVE COATINGS
71
3
family
of
materials includes such fillers as metallized glass fibers, graphite fibers, metal-
lized carbon fibers, quick-quenched aluminum flakes or fibrils, and fine diameter
(6-8
pm) steel fibers. The most common metallic conductor, copper,
is
not used because it
oxidizes within the plastic and impairs its physical properties.
Depending on particle form (sphere, flake, fiber), size and orientation, there is a
certain critical concentration at which conductivity increases drastically (many orders
of
magnitude).
To
achieve significant conductivity with more or less spherical fillers (carbon
black, metal powders), volume percent loadings above
40
are required. A striking differ-
ence in conductivity is observed when a high aspect ratio particle of the same material is
used. Thus, with metal or metallized glass fibers of aspect ratio of
750
as fillers, metallic
conductivities can be achieved at as low as
3
v01
%.l4
At critical concentration, the filler can form a continuous phase through the matrix
in
the form
of
microscopic conductive channels (percolation). The use of high aspect
ratio conductive fillers, when they are properly oriented, will always produce a superior
conductivity at a lower volume percent concentration than comparable spherical fillers.
However, for these materials to have high efficiencies, they also must survive the prepara-
tion and application processes.
For
example, the initial high aspect ratio of a very brittle
material may quickly reduce to powder in a high shear mixing environment,
if
proper
techniques are not developed for incorporating such brittle materials.
Some specific examples
of
uses for filled polymeric coatings usage are summarized
below.
Organic solvent-based coatings
of
acrylic or urethane resins containing either nickel,
silver, copper, or graphite powders are used in the electromagnetic and radio frequency
interference applications. For cost reasons the nickel-filled acrylic coatings are most often
used. Lacquers based on silver give the highest conductivities and, therefore, the best
screening attenuation, but they are the most expensive. Copper lacquers
are
cheaper and
the attenuation is similar to that of silver; the oxidation problem of copper lacquers has
been solved. Lacquers containing graphite are the cheapest, but their performance is also
the least
An initiation layer for the electroless deposition of copper, nickel, NI-P, NI-B alloy
coatings has been described. The layer was formed by applying
a
polyester or its polymer-
ization material solution containing such metal powders as nickel, copper, silver, alumi-
num, cobalt, palladium, zinc, or platinum.
Large differences in the specific conductivity of filled conductive plastics (coatings
were demonstrated between materials filled with
15
v01
%
aluminum alloy fiber,
U
=
0.25
(Rcm)-l, and
15
v01
%
brass fiber,
U
=
170
(f2.cm)".'s
Techniques have been developed
for
generating and incorporating in situ metallic
filler in organic coatings or paints. For example, the use of AgN03 and erythorbic acid,
formaldehyde, paraformaldehyde, or terephthalic aldehyde will result in the generation of
metallic silver in
a
chosen organic coating or paint
2.3
Polymeric
Although the unfilled, molecularly conductive polymeric materials have attracted much
attention recently, the successful developments in surface-metallized plastics make it un-
likely that inherently conductive polymers will be a significant factor in the marketplace
in
the near future. Also, the commercially entrenched, filled conductive polymeric materi-
als seem to become more and more efficient as time goes by.