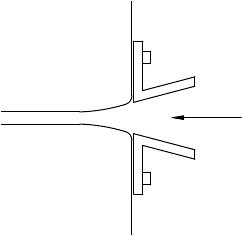
2.3.9 Shaft Shoulder Alignment
During rolldesign and roll manufacturing, it is
assumed that the baseline of all rolls and spacers
are exactly the same. During checking the finished
rolls, the rolls and spacers are placed on agranite
plate representingthis baseline. The gap between
the rollsiscarefully checked in this position. If one
imagines that this granite plate with the rollsis
rotated to 908 so that the granite plate becomes
vertical and the shafts horizontal, then in this
position, the granite plate represents the location
of the shaft shoulders, against which the rollsare
rested. If in the mill, the shaft shoulders are not
aligned, then the rolls cannot be properly aligned.
Unfortunately,this is the case in alarge pro-
portion of mills currently in operation.
During forming,the shaft bearings wear and the shafts become looser and looser.When the operator
side of ashaft can be moved easily up and down,then the shaft and its shoulder usually can also move in
and out. Loose shoulders cannot be used for accurate rollpositioning.Tocorrect this situation, the tapered
bearings can be tightened by pulling the shafts towards the drive-side direction. This also means that the
shoulder moves towards the driveside. If new bearings are installed, then the shoulders are frequently
moved outwards, towards the operator side. Therefore, amill that was assembled with accurately aligned
shoulders can be out of alignment within afew years. Wear in the bearing blocks and stand interfacecan
also contribute to shaft shoulder misalignment.
Different methods are used to align shoulders. The most frequently used method by the author to align
shoulder is described in Chapter 10 (Section 10.3.9).
2.3.10 Installation of Other Units in the Mill
The roll forming base is frequently the most convenient placetoinstall other units or equipment for the
secondaryoperations. These units can be positioned ahead, in-between, or after the roll forming stands. If
the unit is large, the horizontal center between the stands can be enlarged, or the mill bed can be extended
before the first or after the last pass.
It is assumed that all additional operations are continuous (do not require to stop the section).
Such operation can be rotary punching,rotary embossing,welding,curving (sweeping), and others.
Hydraulic presses,which do not generate shocks, can also be mounted on the mill bed. However,
mounting mechanical or pneumatic presses on the mill bed is not recommended.
If the secondaryoperation requires coolant or liquid other than the one used for roll forming,then
aseparate drainage and lubrication system has to be installed. Proper alignment of all additional
equipment and tooling is as crucial as the alignment of the forming rolls.
References
[4] Theis, E. 1995. Handbook of Metalforming Processes.MarcelDekker, NewYork.
[157] Halmos, G.T.1984. Guidelines for purchasing roll forming lines, SME “TechnologyofRoll
Forming”,September 25–27, MF84-954 Toronto,Canada.
[158] Wilson, R.A., Quick change forming cuts inventories, Iron Age ,February3,56–57, 1975.
[160] Wright, J.R., Quick change in roll forming, Prec. Met.,June, 43–45, 1988.
[161] Bradbury, D. 1983. Eliminating roll tooling changeover, FABTECH ’83 Conference,September
26–29, Chicago,IL, MF83-544.
FIGURE 2.53 If required, additional guides can be
applied at the entryside of the straightener and cutoffdie
to help entering the leading edge of the strip.
Roll Forming Handbook2 -32