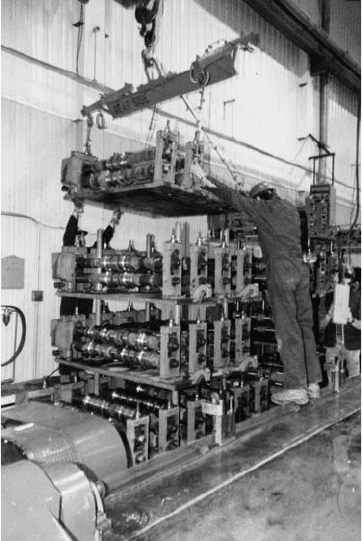
(orsleeve).Itisalsotroublesome to make
additionalsetsofrafts that fit exactlyonto
the pins and, at the same time, provide accurate
shoulder alignment. Twostops at the drive side of
the bed for the longer side of the plate and one stop
at each shortsideare sufficientfor accurate
location (Figure 2.21).
To provide the shortest possible tool change
time, hydraulic pushers and clamps can be used.
The upper surfaceofthe mill bed does not haveto
be fully machined. It is sufficient to machine only
the protruding surfaceswherethe plates (rafts)
rest.
The four lifting lugs attached to the plates
should provide areasonable good balance, and the
lifting attachments (bars or chains) should not rub
against the tooling,shafts, or stands.
To reduce changeover time, all the additional
components such as the entryguides, side-roll
stands, and straighteners should be permanently
attached to each set of plates.
Saving of floor space can be achievedbystoring
the plates of aprofile on top of each other
(Figure2.22). Tubes or other components(Figure
5.158) supporting the upper plate(s) should be
incorporated in the plate design.
2.2.7 Side-by-Side Mills
Tool changeover time can further be reduced by mounting morethan one set of tooling on the mill
shafts. The simplest arrangement for the narrowsections is to install twosets of rolls on common shafts
(Figure2.23). The uncoiler,the prepunched press (if required), and the cutoffpress are in line with one set
of rolls. When profilechange is required, the mill bed is moved sideways to align the second set of rolls
with the other equipment. The complete changeover takesless than 2min. Depending on the length of the
mill bed, two, three, or morepairs of supporting rolls(casters) are attached to the bottom of the mill bed.
The rolls are moving on rails embedded into the floor.Brass slides or linear bearings are also used to move
the mill sideways. The movement is accomplished by electrical motor driven screws or by other means
(e.g., hydraulic cylinders). Moving the mill bed against positive stops assuresproper alignment.
Occasionally,the mill remains in position while the uncoiler and the press (hydraulic) are moved
sideways.
The advantage of this “side-by-side” arrangement is the highup-time. The disadvantage is that setting
and adjusting one section will at the same time change the setting of the other section. However,this
shortcoming can be easily overcome by using one or twomoreextra stands. At the morefrequently
adjusted, critical passes, only rolls of one set are installed. At the critical passes of the other section, only
rollsfor the other section are installed. This arrangement ensures that adjusting one section will not
influence the other section.
It should also be noted that both sets of rollsmust havethe same pitch diameter and that recutting one
set of rolls will necessitate the recutting of the other.During setup,the rollscloser to the shaft shoulders
(drive side) should be set and tested first, followed by the roll set at the operator side.
To keep the changeover time to aminimum, each set of rolls should haveits own entryguide and
straightener.Ifthe product is curved(swept) after the operation, then two individual curving units
FIGURE 2.22 Storing plates on top of each other
reduces floor space requirement (Courtesy of Ideal
Roofing Co.Ltd.).
Roll Forming Mill 2 -13