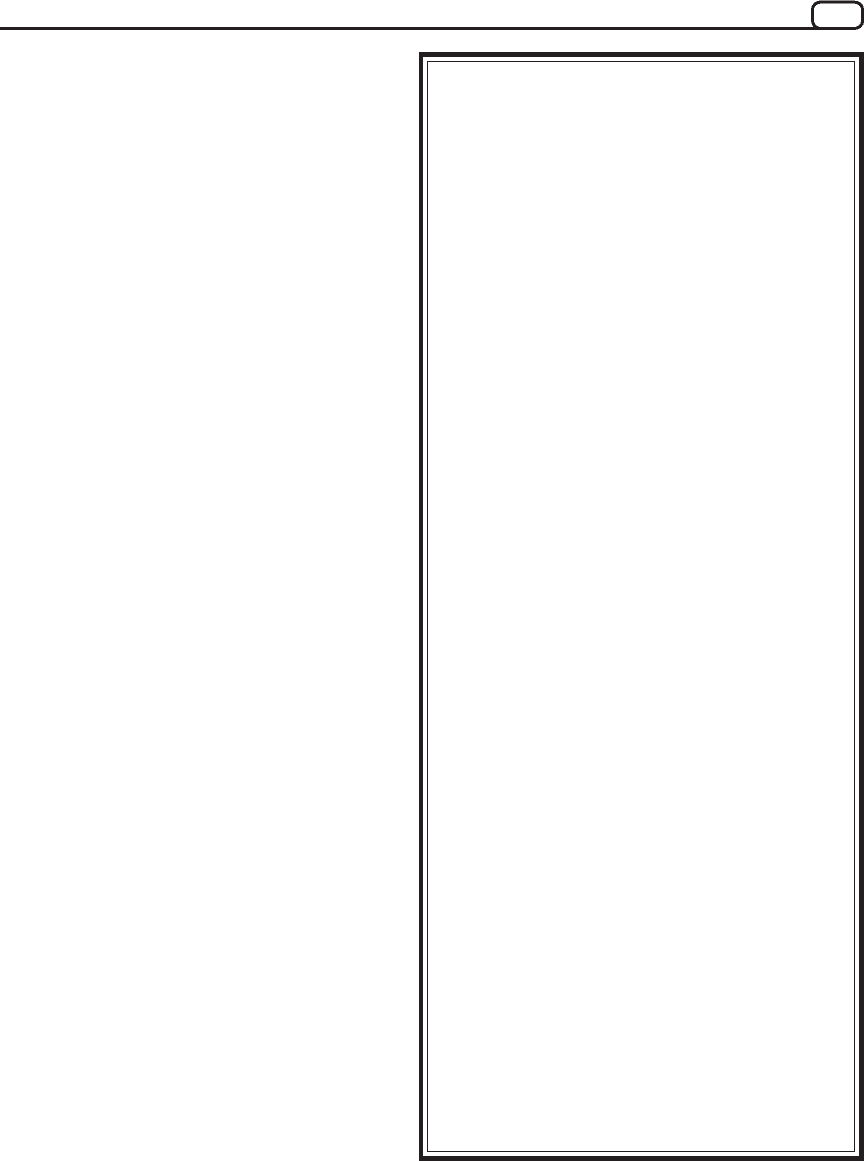
Distribution Strategy
195
optimal number of consumers in a given time
schedule at the lowest possible cost while
maintaining the desired degree of control. In
implementing this distribution strategy the
company should make the comparison of
direct versus indirect distribution on the basis
of the following parameters:
• Cost,
• Product characteristics,
• Degree of control, and
• Other factors.
Cost variable includes distribution costs,
opportunity costs which incurs during the non-
availability of the product inventory costs and
shipping costs. The product attributes may be
measured in terms of replacement rate, gross
margin, service requirements and the time
involved in search thereof. The degree of
control is generally greater when direct
distribution is followed. The factors other than
above are adaptability, technological changes
and social/cultural values. The effective
implementation of channel structure strategy
may result effectively in performing the direct
distribution. However this may result into the
high marketing costs and needs a large degree
of control. The foreign firms need to consider
the following issues for channel selection for
effective distribution:
• Market access
• Multiple markets, seasonality, safety,
channel length
• Value added competencies
• Resources, logistics and control,
competitive skills
• Financial consideration
• Building distribution network,
revenue-cost implications, operating
capital requirements
• Flexibility and control conditions
Strategy Focus 5.1: Radio Frequency
Identification Technology in Distribution
Management
Wireless identification and tracking with Radio
Frequency identification (RFID) technology represents
a new way to conduct operations, which creates new
benefits and challenges. This technology operates with
a reader that identifies the product tag in the warehouse
and sends the signal about its movement through a
computer based tracking tool. The identification is
accomplished by an interrogator, also called a reader or
“master,” and a tag, also called a transponder or “slave”
that has a unique identification code. Data is exchanged
between tags and readers using radio waves between
the tag and interrogator, and no direct line of sight is
required for the transaction. The interrogator asks the
tag for the code, or processes the signal being broadcast
by the tag, decodes the transmission and transfers the
data to a computer. The computer, in turn, may simply
record the reading, or look up the tag identification in a
database to direct further action, and may also direct
the interrogator to write additional information to the
tag. The latest generation of RFID allows the dozens
of individual objects within a group to be uniquely
identified at the same time. This is in contrast to bar
codes, which must be read one by one, and can be very
advantageous in high-speed reading, sorting and material
handling applications.
The low-cost tags generally are have limited data storage
capacity, typically 32 to 128 bits, which are read-only
(not rewriteable) like bar codes, and have limited read
range. On the contrary, high-cost tags are available for
many more complicated longer read applications. They
often have their own power source for managing large
storage databases. RFID systems are available in a
wide range of frequencies to suit various performance
needs. Frequency is an important factor in transmission
range and speed. This is an important consideration
when planning logistics and supply chain applications.
Most RFID technology used in warehousing and
distribution operates at 13.56 MHz (high frequency),
860-930MHz (ultrahigh frequency, or UHF) or the
2.45GHz (microwave) band.
Wal-Mart has already begun its RFID pilot with
selected distributors in 2006 while other eight suppliers
that started shipping a handful of RFID-enabled pallets
were Gillette, Hewlett-Packard, Johnson & Johnson,
Kimberly-Clark, Kraft Foods, Nestle Purina PetCare,
and Procter & Gamble.