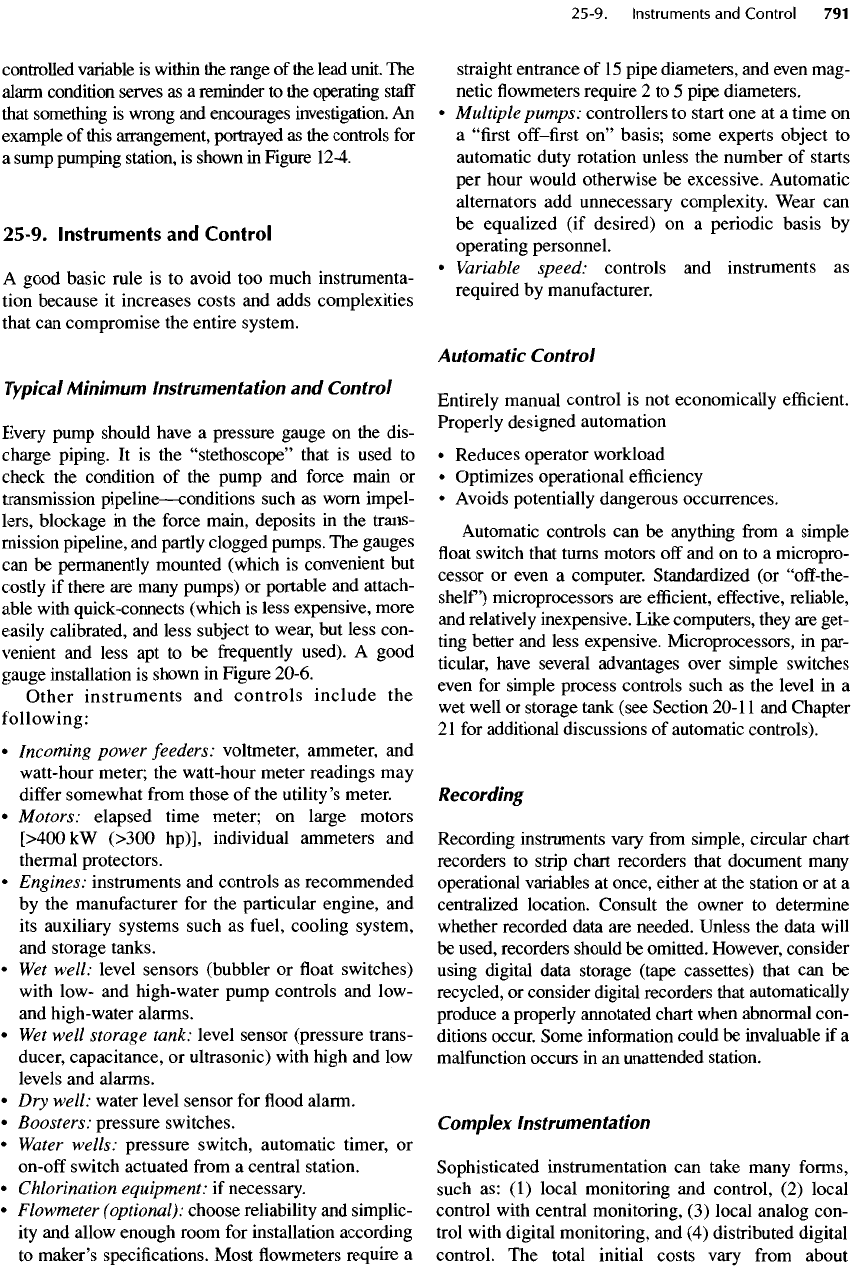
controlled variable
is
within
the
range
of the
lead unit.
The
alarm
condition serves
as a
reminder
to the
operating
staff
that
something
is
wrong
and
encourages investigation.
An
example
of
this arrangement, portrayed
as the
controls
for
a
sump pumping station,
is
shown
in
Figure 12-4.
25-9.
Instruments
and
Control
A
good basic rule
is to
avoid
too
much instrumenta-
tion because
it
increases costs
and
adds complexities
that
can
compromise
the
entire system.
Typical
Minimum Instrumentation
and
Control
Every
pump should have
a
pressure gauge
on the
dis-
charge
piping.
It is the
"stethoscope"
that
is
used
to
check
the
condition
of the
pump
and
force main
or
transmission
pipeline
—
conditions
such
as
worn impel-
lers, blockage
in the
force main, deposits
in the
trans-
mission pipeline,
and
partly clogged pumps.
The
gauges
can
be
permanently mounted (which
is
convenient
but
costly
if
there
are
many pumps)
or
portable
and
attach-
able
with quick-connects (which
is
less expensive, more
easily
calibrated,
and
less subject
to
wear,
but
less con-
venient
and
less
apt to be
frequently
used).
A
good
gauge
installation
is
shown
in
Figure 20-6.
Other instruments
and
controls include
the
following:
•
Incoming power
feeders:
voltmeter, ammeter,
and
watt-hour
meter;
the
watt-hour meter readings
may
differ
somewhat
from
those
of the
utility's meter.
•
Motors: elapsed time meter;
on
large motors
[>400kW
(>300
hp)], individual ammeters
and
thermal
protectors.
•
Engines: instruments
and
controls
as
recommended
by
the
manufacturer
for the
particular engine,
and
its
auxiliary systems such
as
fuel,
cooling system,
and
storage tanks.
• Wet
well: level sensors (bubbler
or float
switches)
with
low-
and
high-water pump controls
and
low-
and
high-
water
alarms.
• Wet
well storage tank: level sensor (pressure trans-
ducer,
capacitance,
or
ultrasonic) with high
and low
levels
and
alarms.
• Dry
well: water level sensor
for flood
alarm.
•
Boosters: pressure switches.
•
Water
wells: pressure switch, automatic timer,
or
on-off
switch actuated
from
a
central station.
•
Chlorination equipment:
if
necessary.
•
Flowmeter
(optional):
choose reliability
and
simplic-
ity
and
allow enough room
for
installation according
to
maker's specifications. Most
flowmeters
require
a
straight entrance
of 15
pipe diameters,
and
even mag-
netic
flowmeters
require
2 to 5
pipe
diameters.
•
Multiple
pumps: controllers
to
start
one at a
time
on
a
"first
off-first
on"
basis; some experts object
to
automatic duty rotation unless
the
number
of
starts
per
hour would otherwise
be
excessive. Automatic
alternators
add
unnecessary complexity. Wear
can
be
equalized
(if
desired)
on a
periodic basis
by
operating personnel.
•
Variable
speed: controls
and
instruments
as
required
by
manufacturer.
Automatic
Control
Entirely manual control
is not
economically
efficient.
Properly designed automation
•
Reduces operator workload
•
Optimizes operational
efficiency
•
Avoids potentially dangerous occurrences.
Automatic
controls
can be
anything
from a
simple
float
switch
that turns motors
off and on to a
micropro-
cessor
or
even
a
computer. Standardized
(or
"off-the-
shelf)
microprocessors
are
efficient,
effective,
reliable,
and
relatively inexpensive. Like computers, they
are
get-
ting
better
and
less expensive. Microprocessors,
in
par-
ticular,
have several advantages over simple switches
even for
simple process controls such
as the
level
in a
wet
well
or
storage tank (see Section
20-1
1
and
Chapter
21 for
additional discussions
of
automatic controls).
Recording
Recording instruments vary
from
simple, circular chart
recorders
to
strip chart recorders that document many
operational variables
at
once, either
at the
station
or at a
centralized location. Consult
the
owner
to
determine
whether recorded data
are
needed. Unless
the
data will
be
used, recorders should
be
omitted. However, consider
using digital data storage (tape cassettes) that
can be
recycled,
or
consider digital recorders that automatically
produce
a
properly annotated chart when abnormal con-
ditions occur. Some information could
be
invaluable
if a
malfunction
occurs
in an
unattended station.
Complex
Instrumentation
Sophisticated instrumentation
can
take many forms,
such
as: (1)
local monitoring
and
control,
(2)
local
control with central monitoring,
(3)
local analog con-
trol with digital monitoring,
and (4)
distributed digital
control.
The
total initial costs vary
from
about