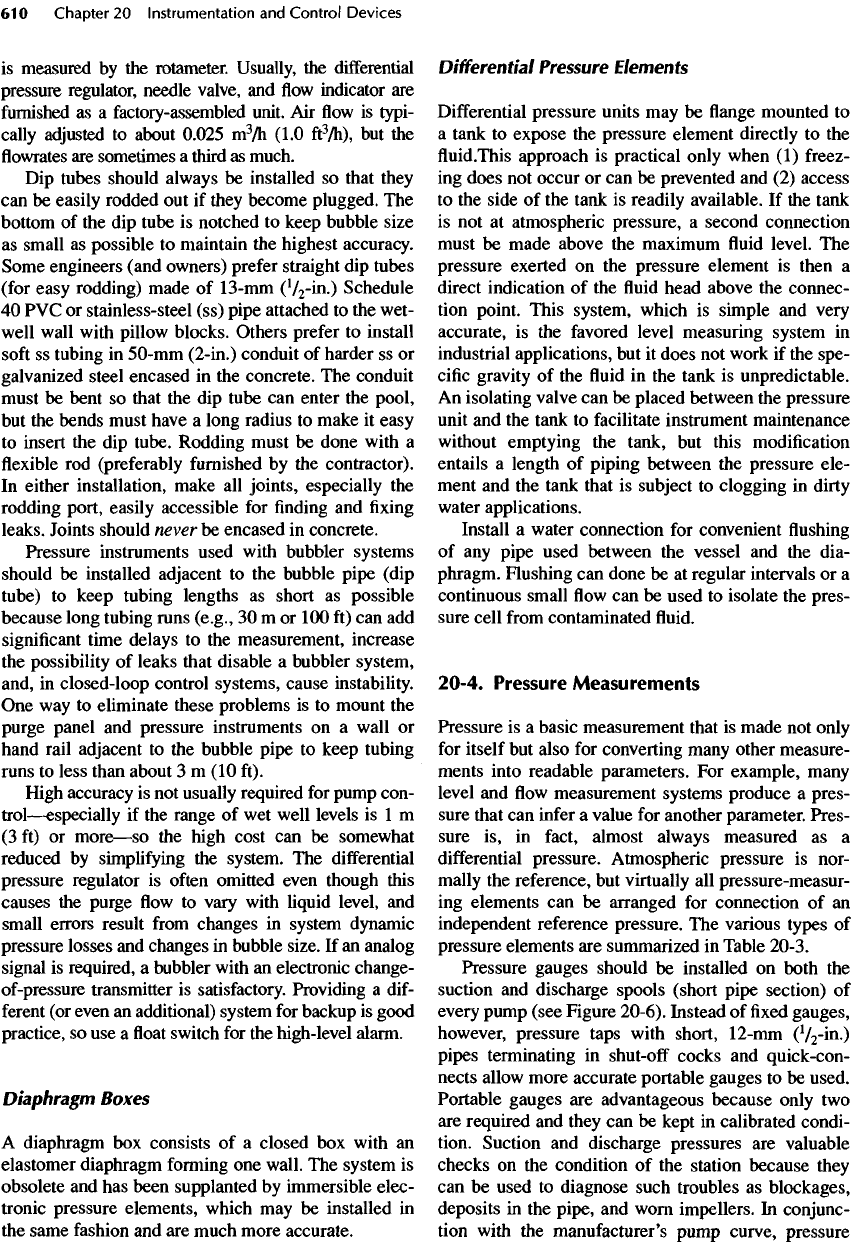
is
measured
by the
rotameter.
Usually,
the
differential
pressure
regulator, needle valve,
and flow
indicator
are
furnished
as a
factory-assembled unit.
Ak flow is
typi-
cally
adjusted
to
about
0.025
m
3
/h
(1.0
ft
3
/h), but the
flowrates
are
sometimes
a
third
as
much.
Dip
tubes should always
be
installed
so
that they
can
be
easily rodded
out if
they become plugged.
The
bottom
of the dip
tube
is
notched
to
keep bubble size
as
small
as
possible
to
maintain
the
highest accuracy.
Some engineers (and owners) prefer straight
dip
tubes
(for
easy rodding) made
of
13-mm
(
l
/
2
-in.)
Schedule
40 PVC or
stainless-steel (ss) pipe attached
to the
wet-
well wall with pillow blocks. Others prefer
to
install
soft
ss
tubing
in
50-mm (2-in.) conduit
of
harder
ss or
galvanized
steel encased
in the
concrete.
The
conduit
must
be
bent
so
that
the dip
tube
can
enter
the
pool,
but
the
bends must have
a
long radius
to
make
it
easy
to
insert
the dip
tube. Rodding must
be
done with
a
flexible rod
(preferably
furnished
by the
contractor).
In
either installation, make
all
joints,
especially
the
rodding port, easily accessible
for
finding
and
fixing
leaks. Joints should never
be
encased
in
concrete.
Pressure instruments used with bubbler systems
should
be
installed adjacent
to the
bubble pipe (dip
tube)
to
keep tubing lengths
as
short
as
possible
because long tubing runs
(e.g.,
30 m or 100 ft) can add
significant
time delays
to the
measurement, increase
the
possibility
of
leaks that disable
a
bubbler system,
and,
in
closed-loop control systems, cause instability.
One
way to
eliminate these
problems
is to
mount
the
purge
panel
and
pressure instruments
on a
wall
or
hand
rail
adjacent
to the
bubble pipe
to
keep tubing
runs
to
less than about
3 m (10
ft).
High
accuracy
is not
usually
required
for
pump con-
trol—especially
if the
range
of wet
well levels
is 1 m
(3 ft) or
more
—
so the
high cost
can be
somewhat
reduced
by
simplifying
the
system.
The
differential
pressure regulator
is
often
omitted even though this
causes
the
purge
flow to
vary
with liquid level,
and
small
errors result
from
changes
in
system dynamic
pressure
losses
and
changes
in
bubble size.
If an
analog
signal
is
required,
a
bubbler with
an
electronic
change-
of-pressure transmitter
is
satisfactory. Providing
a
dif-
ferent
(or
even
an
additional) system
for
backup
is
good
practice,
so use a float
switch
for the
high-level alarm.
Diaphragm
Boxes
A
diaphragm
box
consists
of a
closed
box
with
an
elastomer diaphragm
forming
one
wall.
The
system
is
obsolete
and has
been supplanted
by
immersible
elec-
tronic pressure elements, which
may be
installed
in
the
same
fashion
and are
much more accurate.
Differential
Pressure Elements
Differential
pressure units
may be flange
mounted
to
a
tank
to
expose
the
pressure element directly
to the
fluid.This
approach
is
practical only when
(1)
freez-
ing
does
not
occur
or can be
prevented
and (2)
access
to the
side
of the
tank
is
readily available.
If the
tank
is not at
atmospheric pressure,
a
second connection
must
be
made above
the
maximum
fluid
level.
The
pressure exerted
on the
pressure element
is
then
a
direct indication
of the fluid
head above
the
connec-
tion point. This system, which
is
simple
and
very
accurate,
is the
favored
level measuring system
in
industrial applications,
but it
does
not
work
if the
spe-
cific
gravity
of the fluid in the
tank
is
unpredictable.
An
isolating valve
can be
placed between
the
pressure
unit
and the
tank
to
facilitate instrument maintenance
without emptying
the
tank,
but
this modification
entails
a
length
of
piping between
the
pressure ele-
ment
and the
tank that
is
subject
to
clogging
in
dirty
water applications.
Install
a
water connection
for
convenient
flushing
of
any
pipe
used between
the
vessel
and the
dia-
phragm. Flushing
can
done
be at
regular intervals
or a
continuous small
flow can be
used
to
isolate
the
pres-
sure cell
from
contaminated
fluid.
20-4. Pressure Measurements
Pressure
is a
basic measurement that
is
made
not
only
for
itself
but
also
for
converting many other measure-
ments into readable parameters.
For
example,
many
level
and flow
measurement systems produce
a
pres-
sure that
can
infer
a
value
for
another parameter.
Pres-
sure
is, in
fact,
almost always measured
as a
differential
pressure. Atmospheric pressure
is
nor-
mally
the
reference,
but
virtually
all
pressure-measur-
ing
elements
can be
arranged
for
connection
of an
independent reference pressure.
The
various types
of
pressure elements
are
summarized
in
Table 20-3.
Pressure gauges should
be
installed
on
both
the
suction
and
discharge
spools
(short
pipe
section)
of
every pump (see Figure
20-6).
Instead
of fixed
gauges,
however, pressure taps with short,
12-mm
(
l
/
2
-in.)
pipes terminating
in
shut-off
cocks
and
quick-con-
nects allow more accurate portable gauges
to be
used.
Portable gauges
are
advantageous because only
two
are
required
and
they
can be
kept
in
calibrated condi-
tion. Suction
and
discharge pressures
are
valuable
checks
on the
condition
of the
station because they
can
be
used
to
diagnose such
troubles
as
blockages,
deposits
in the
pipe,
and
worn impellers.
In
conjunc-
tion with
the
manufacturer's pump curve, pressure