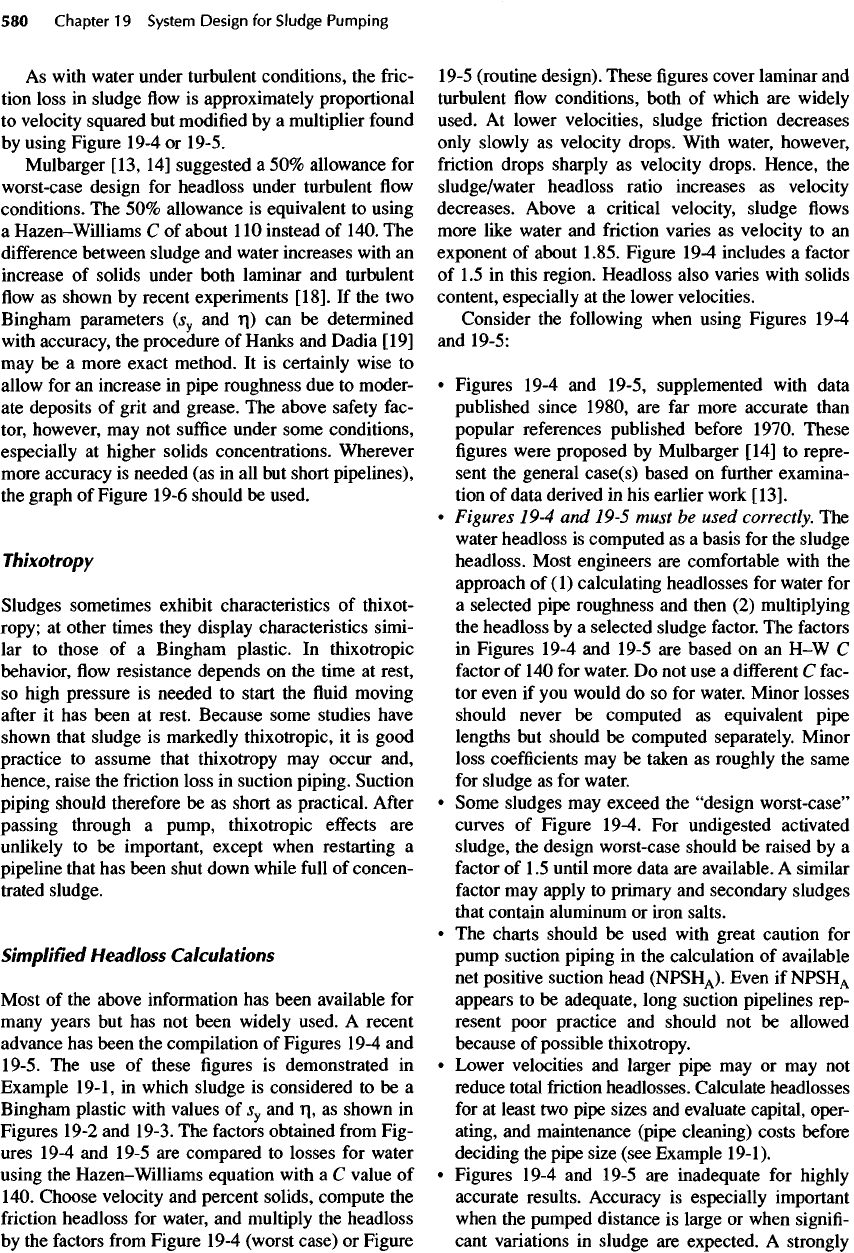
As
with water under turbulent
conditions,
the fric-
tion
loss
in
sludge
flow is
approximately proportional
to
velocity squared
but
modified
by a
multiplier
found
by
using Figure
19-4
or
19-5.
Mulbarger
[13,
14]
suggested
a 50%
allowance
for
worst-case design
for
headloss under turbulent
flow
conditions.
The 50%
allowance
is
equivalent
to
using
a
Hazen-Williams
C of
about
1
10
instead
of
140.
The
difference
between sludge
and
water increases with
an
increase
of
solids under both laminar
and
turbulent
flow as
shown
by
recent experiments
[18].
If the two
Bingham
parameters
(s
y
and
J])
can be
determined
with
accuracy,
the
procedure
of
Hanks
and
Dadia [19]
may
be a
more exact method.
It is
certainly wise
to
allow
for an
increase
in
pipe roughness
due to
moder-
ate
deposits
of
grit
and
grease.
The
above
safety
fac-
tor, however,
may not
suffice
under some conditions,
especially
at
higher solids concentrations. Wherever
more accuracy
is
needed
(as in all but
short pipelines),
the
graph
of
Figure 19-6 should
be
used.
Thixotropy
Sludges
sometimes exhibit characteristics
of
thixot-
ropy;
at
other times they display characteristics simi-
lar to
those
of a
Bingham plastic.
In
thixotropic
behavior,
flow
resistance depends
on the
time
at
rest,
so
high pressure
is
needed
to
start
the fluid
moving
after
it has
been
at
rest. Because some studies have
shown
that sludge
is
markedly thixotropic,
it is
good
practice
to
assume that thixotropy
may
occur and,
hence, raise
the
friction loss
in
suction piping. Suction
piping should therefore
be as
short
as
practical.
After
passing through
a
pump, thixotropic
effects
are
unlikely
to be
important, except when restarting
a
pipeline that
has
been shut down while
full
of
concen-
trated
sludge.
Simplified
Headloss Calculations
Most
of the
above information
has
been available
for
many
years
but has not
been widely used.
A
recent
advance
has
been
the
compilation
of
Figures
19-4
and
19-5.
The use of
these
figures is
demonstrated
in
Example
19-1,
in
which sludge
is
considered
to be a
Bingham
plastic
with
values
of
s
y
and
Tj,
as
shown
in
Figures 19-2
and
19-3.
The
factors obtained
from
Fig-
ures
19-4
and
19-5
are
compared
to
losses
for
water
using
the
Hazen-Williams equation with
a C
value
of
140. Choose velocity
and
percent solids, compute
the
friction
headloss
for
water,
and
multiply
the
headloss
by
the
factors
from
Figure
19-4
(worst case)
or
Figure
19-5
(routine
design).
These
figures
cover laminar
and
turbulent
flow
conditions, both
of
which
are
widely
used.
At
lower velocities, sludge
friction
decreases
only slowly
as
velocity drops. With water, however,
friction
drops sharply
as
velocity drops. Hence,
the
sludge/water headloss ratio increases
as
velocity
decreases. Above
a
critical velocity, sludge
flows
more like water
and
friction varies
as
velocity
to an
exponent
of
about 1.85. Figure 19-4 includes
a
factor
of
1.5
in
this region. Headloss also varies with solids
content, especially
at the
lower velocities.
Consider
the
following when using Figures 19-4
and
19-5:
•
Figures 19-4
and
19-5, supplemented with data
published since 1980,
are far
more accurate than
popular references published before 1970. These
figures
were proposed
by
Mulbarger [14]
to
repre-
sent
the
general case(s) based
on
further
examina-
tion
of
data derived
in his
earlier work
[13].
•
Figures 19-4
and
79-5 must
be
used
correctly.
The
water
headloss
is
computed
as a
basis
for the
sludge
headloss. Most engineers
are
comfortable with
the
approach
of (1)
calculating headlosses
for
water
for
a
selected pipe roughness
and
then
(2)
multiplying
the
headloss
by a
selected sludge
factor.
The
factors
in
Figures 19-4
and
19-5
are
based
on an H-W C
factor
of 140 for
water.
Do not use a
different
C
fac-
tor
even
if you
would
do so for
water. Minor
losses
should never
be
computed
as
equivalent
pipe
lengths
but
should
be
computed separately. Minor
loss
coefficients
may be
taken
as
roughly
the
same
for
sludge
as for
water.
•
Some sludges
may
exceed
the
"design
worst-case"
curves
of
Figure 19-4.
For
undigested activated
sludge,
the
design worst-case should
be
raised
by a
factor
of 1.5
until more data
are
available.
A
similar
factor
may
apply
to
primary
and
secondary sludges
that contain aluminum
or
iron salts.
• The
charts should
be
used with great caution
for
pump
suction piping
in the
calculation
of
available
net
positive suction head
(NPSH
A
).
Even
if
NPSH
A
appears
to be
adequate, long suction pipelines rep-
resent poor practice
and
should
not be
allowed
because
of
possible thixotropy.
•
Lower velocities
and
larger pipe
may or may not
reduce total
friction
headlosses. Calculate headlosses
for
at
least
two
pipe sizes
and
evaluate capital, oper-
ating,
and
maintenance (pipe cleaning) costs before
deciding
the
pipe size (see Example 19-1).
•
Figures 19-4
and
19-5
are
inadequate
for
highly
accurate results. Accuracy
is
especially
important
when
the
pumped distance
is
large
or
when
signifi-
cant
variations
in
sludge
are
expected.
A
strongly