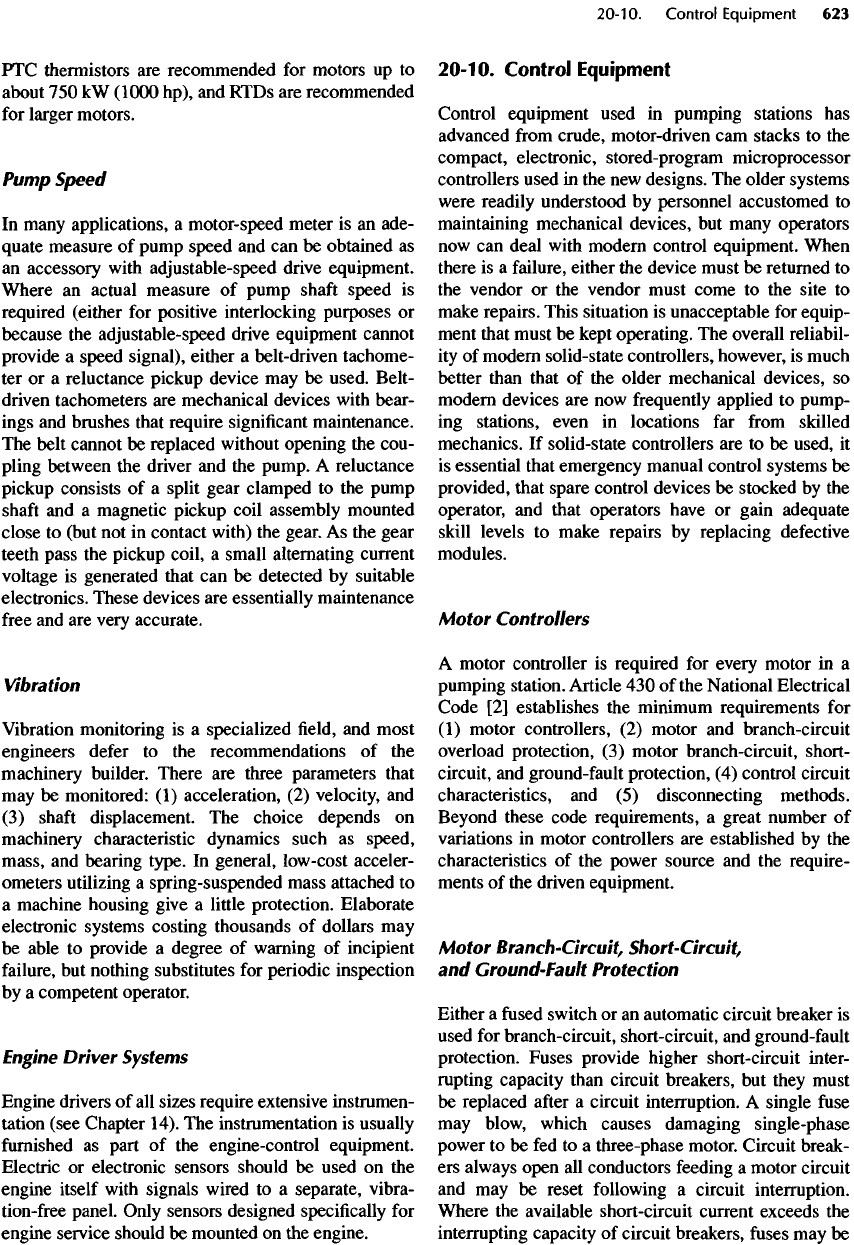
PTC
thermistors
are
recommended
for
motors
up to
about
750 kW
(1000 hp),
and
RTDs
are
recommended
for
larger motors.
Pump Speed
In
many applications,
a
motor-speed meter
is an
ade-
quate
measure
of
pump speed
and can be
obtained
as
an
accessory with adjustable-speed drive equipment.
Where
an
actual measure
of
pump
shaft
speed
is
required (either
for
positive interlocking purposes
or
because
the
adjustable-speed drive equipment cannot
provide
a
speed signal), either
a
belt-driven tachome-
ter or a
reluctance pickup device
may be
used. Belt-
driven
tachometers
are
mechanical devices with bear-
ings
and
brushes that require
significant
maintenance.
The
belt cannot
be
replaced without opening
the
cou-
pling between
the
driver
and the
pump.
A
reluctance
pickup
consists
of a
split gear clamped
to the
pump
shaft
and a
magnetic pickup coil assembly mounted
close
to
(but
not in
contact with)
the
gear.
As the
gear
teeth
pass
the
pickup coil,
a
small alternating current
voltage
is
generated that
can be
detected
by
suitable
electronics. These devices
are
essentially maintenance
free
and are
very accurate.
Vibration
Vibration
monitoring
is a
specialized
field, and
most
engineers
defer
to the
recommendations
of the
machinery
builder. There
are
three parameters that
may
be
monitored:
(1)
acceleration,
(2)
velocity,
and
(3)
shaft
displacement.
The
choice depends
on
machinery
characteristic dynamics such
as
speed,
mass,
and
bearing type.
In
general, low-cost acceler-
ometers utilizing
a
spring-suspended mass attached
to
a
machine housing give
a
little protection. Elaborate
electronic systems costing thousands
of
dollars
may
be
able
to
provide
a
degree
of
warning
of
incipient
failure,
but
nothing substitutes
for
periodic inspection
by
a
competent operator.
Engine
Driver Systems
Engine
drivers
of all
sizes require extensive instrumen-
tation
(see Chapter 14).
The
instrumentation
is
usually
furnished
as
part
of the
engine-control equipment.
Electric
or
electronic sensors should
be
used
on the
engine itself with signals wired
to a
separate, vibra-
tion-free
panel. Only sensors designed specifically
for
engine service should
be
mounted
on the
engine.
20-10.
Control
Equipment
Control equipment used
in
pumping stations
has
advanced
from
crude, motor-driven
cam
stacks
to the
compact, electronic,
stored-program
microprocessor
controllers used
in the new
designs.
The
older systems
were readily understood
by
personnel accustomed
to
maintaining mechanical devices,
but
many operators
now
can
deal with modern control equipment. When
there
is a
failure,
either
the
device must
be
returned
to
the
vendor
or the
vendor must come
to the
site
to
make
repairs. This situation
is
unacceptable
for
equip-
ment
that must
be
kept operating.
The
overall reliabil-
ity
of
modern solid-state controllers, however,
is
much
better than that
of the
older mechanical devices,
so
modern
devices
are now
frequently
applied
to
pump-
ing
stations, even
in
locations
far
from
skilled
mechanics.
If
solid-state controllers
are to be
used,
it
is
essential
that emergency manual control systems
be
provided, that spare control devices
be
stocked
by the
operator,
and
that operators have
or
gain adequate
skill levels
to
make repairs
by
replacing defective
modules.
Motor Controllers
A
motor controller
is
required
for
every motor
in a
pumping
station. Article
430 of the
National Electrical
Code
[2]
establishes
the
minimum requirements
for
(1)
motor controllers,
(2)
motor
and
branch-circuit
overload protection,
(3)
motor branch-circuit, short-
circuit,
and
ground-fault protection,
(4)
control circuit
characteristics,
and (5)
disconnecting methods.
Beyond
these code requirements,
a
great number
of
variations
in
motor controllers
are
established
by the
characteristics
of the
power source
and the
require-
ments
of the
driven equipment.
Motor Branch-Circuit,
Short-Circuit,
and
Ground-Fault
Protection
Either
a
fused
switch
or an
automatic circuit breaker
is
used
for
branch-circuit, short-circuit,
and
ground-fault
protection. Fuses provide higher short-circuit inter-
rupting
capacity than circuit breakers,
but
they must
be
replaced
after
a
circuit interruption.
A
single
fuse
may
blow, which causes damaging single-phase
power
to be fed to a
three-phase motor. Circuit break-
ers
always open
all
conductors feeding
a
motor circuit
and
may be
reset
following
a
circuit interruption.
Where
the
available short-circuit current exceeds
the
interrupting
capacity
of
circuit breakers,
fuses
may be