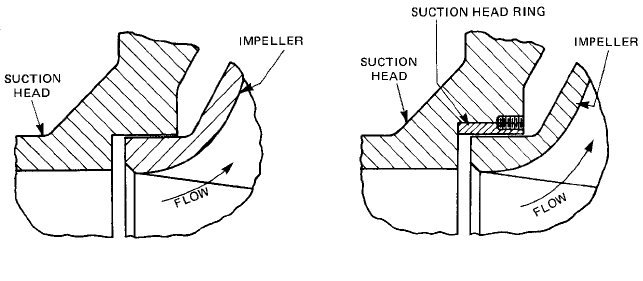
2.2.1 CENTRIFUGAL PUMP: MAJOR COMPONENTS 2.119
FIGURE 39 A plain flat leakage joint with no rings
further by adding the word wearing, such as casing wearing ring. A renewable part for the
impeller wearing surface is called the impeller ring. Pumps with both stationary and
rotating rings are said to have double-ring construction.
Wearing Ring Types Various types of wearing ring designs, and the selection of the
most desirable type depends on the liquid being handled, the pressure differential across
the leakage joint, the rubbing speed, and the particular pump design. In general, cen-
trifugal pump designers use the ring construction that they have found to be most suit-
able for each particular pump service.
The most common ring constructions are the flat type (see Figures 40 and 41) and the
L type. The leakage joint in the former is a straight, annular clearance. In the L-type ring
(see Figure 43), the axial clearance between the impeller and the casing ring is large, so the
velocity of the liquid flowing into the stream entering the suction eye of the impeller is low.
The L-type casing rings shown in Figures 43 and 44 have the additional function of guid-
ing the liquid into the impeller eye; they are called nozzle rings. Impeller rings of the L type
shown in Figure 44 also furnish protection for the face of the impeller wearing ring hub.
Some designers favor labyrinth-type rings (see Figures 45 and 46) that have two or
more annular leakage joints connected by relief chambers. In leakage joints involving a
single unbroken path, the flow is a function of both the area and the length of the joint as
well as of the pressure differential across the joint. If the path is broken by relief chambers
(see to Figure 42, 45, and 46), the velocity energy in the jet is dissipated in each relief cham-
ber, increasing the resistance. As a result, with several relief chambers and several leak-
age joints for the same actual flow through the joint, the area and hence the clearance
between the rings can be greater than for an unbroken, shorter leakage joint.
The single labyrinth ring with only one relief chamber (refer to Figure 45) is often
called an intermeshing ring. The step-ring type (refer to Figure 42) utilizes two flat-ring
elements of slightly different diameters over the total leakage joint width with a relief
chamber between the two elements. Other ring designs also use some form of relief cham-
ber. For example, one commonly used in small pumps has a flat joint similar to that in Fig-
ure 40, but with one surface broken by a number of grooves. These act as relief chambers
to dissipate the jet velocity head, thereby increasing the resistance through the joint and
decreasing the leakage.
For raw water pumps in waterworks service and for larger pumps in sewage services
in which the liquid contains sand and grit, water-flushed rings have been used (see Figure
47). Clear water under a pressure greater than that on the discharge side of the rings is
piped to the inlet and distributed by the cored passage, the holes through the stationary
ring, and the groove to the leakage joint. Ideally, the clear water should fill the leakage
joint with some flow to the suction and discharge sides to prevent any sand or grit from
getting into the clearance space. Wearing-ring flush is also employed in some process
pumps when pumping solids or abrasives to minimize ring wear by injecting a compatible
clean liquid between the rings.
FIGURE 40 A single flat casing ring construction.