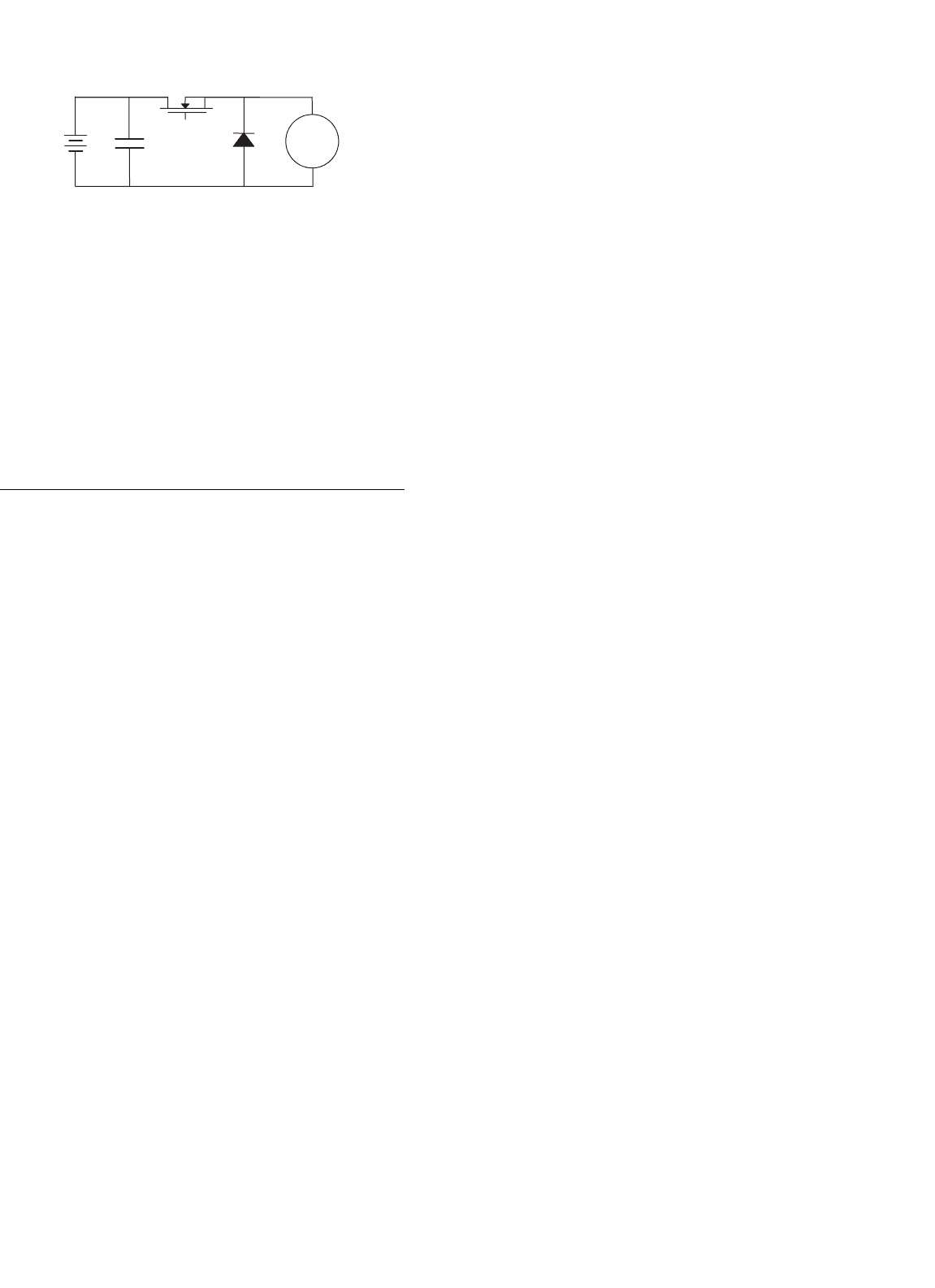
644 D. J. Perreault et al.
FIGURE 25.9 Low-loss circuit to control the speed of a motor.
through a variable-output dc-to-dc converter. The converter
is located close to the motor and no filter is required between
the converter output and motor winding.
Another low-loss method that can be used to control the
speed of a motor employs a three-phase brushless dc motor.
The speed in this case is controlled by controlling the MOS-
FETs in the dc-to-three-phase-ac converter that drives the
motor.
25.5 Multiplexed Load Control
Another emerging application of power electronics in auto-
mobiles is in the area of load control. In the conventional
point-to-point wiring architecture, most of the loads are con-
trolled directly by the primary mechanical switches, as shown
in Fig. 25.1. In a point-to-point wiring architecture, each load
has a dedicated wire connecting it to the fuse box via the
primary switch. Consequently, fairly heavy wires have to be
routed all over the vehicle, as illustrated in Fig. 25.10a. The
situation is made worse when multiple switches control the
same load, as is the case with power windows and power
door locks. The complete harness of a 1994 C-class Mercedes-
Benz that uses point-to-point wiring has about 1000 wires,
with a total length of 2 km, over 300 connectors and weighs
36 kg. The process of assembling the wiring harness is difficult
and time consuming, leading to high labor costs. Retrofitting,
fault tracing, and repairing are time consuming and expen-
sive. The bulky harness also places constraints on the vehicle
body design, and the large number of connectors compromise
system reliability.
An alternative wiring technique is to control the loads
remotely and multiplex the control signals over a communi-
cation bus, as shown in Fig. 25.10b and c. A control message is
sent on the communication bus to switch a particular load on
or off. This allows more flexibility in the layout of the power
cables and could allow the pre-assembly of the harness to be
more automated. Furthermore, with communication between
the remote switches, it is practical to have a power manage-
ment system than can turn off non-essential loads when there
is a power shortage. One possibility is to group the remote
switches into strategically located distribution boxes, as shown
in Fig. 25.10b. A power and a communication bus connect
the distribution boxes. Another possibility is to integrate the
remote switches with the load, i.e. point-of-load switching,
as shown in Fig. 25.10c. In Fig. 25.10b the transceivers are
also built into the distribution boxes, while in Fig. 25.10c each
load and primary switch has an integrated transceiver. The
point-of-load switching topology is attractive because of its
simplicity, but raises cost and fusing challenges.
Multiplexed remote switching architectures have been
under consideration since at least the early 1970s, when
Ziomek investigated their application to various electrical sub-
systems [28]. The initial interest was dampened by cost and
reliability concerns and the non-availability of appropriate
remote switches. However, advances in semiconductor tech-
nology and rapid growth in the automotive electrical system
revived interest in multiplexed architectures. The SAE Mul-
tiplexing Standards Committee has partitioned automotive
communications into three classes: Class A for low data-rate
(1–10 kbit/s) communication for the control of body func-
tions, such as headlamps, windshield wipers, and power win-
dows, Class B for medium data-rate (10–100 kbit/s) parametric
data exchange, and Class C for high data-rate (1 Mbit/s) real-
time communication between safety critical functions, such
as between ABS sensors and brake actuators [29]. Although
load control is categorized as Class A, lack of any widely
accepted Class A communication protocols has lead to the
application of Class B and Class C communication IC’s to
load control. Class B has received the most attention due to
the California Air Resources Board mandated requirement for
on-board diagnostics (OBD II) and a large number of com-
peting protocols, including the French vehicle-area network
(VAN), the ISO 9141 and the SAE J1850, have been devel-
oped [30]. Of these, the SAE J1850 is the most popular in
the US. Another popular protocol is the controller area net-
work (CAN) developed by Bosch [31]. Although designed for
Class C with bit rates up to 1 Mbit/s, it is being applied for
Class A and Class B applications due to the availability of
inexpensive CAN ICs from a large number of semiconductor
manufacturers.
Remote switching systems require remote power switches.
An ideal remote switch must have a low on-state voltage,
be easy to drive from a micro-controller, and incorporate
current sensing. A low on-state voltage helps minimize the
heatsinking requirements, while current sensing is needed for
the circuit protection function to be incorporated into the
switch. To withstand the harsh automotive environment the
switch must also be rugged. Furthermore, if PWM control is
required for the load, the switch must have short turn-on and
turn-off times and a high cycle-life. The traditional means of
remotely switching loads in an automobile is via electrome-
chanical relays. Although relays offer the lowest voltage drop
per unit cost, they require large drive current, are relatively
large, are difficult to integrate with logic, and are not suit-
able for PWM applications [32–34]. Therefore, their use will
be limited to very high current, non-PWM applications. The
power levels of the individual loads in the automobile are too
low for IGBTs and MCTs to be competitive. Bipolar transistors