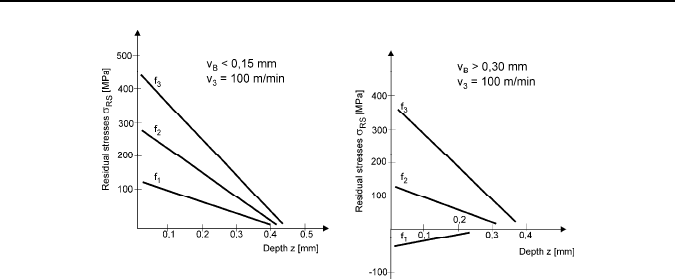
3 Residual Stresses and Microstructural Modifications 77
stresses with arrows as a function of the respective processing conditions, i.e. with
different grinding speeds and the same feed rate and cutting depth, and with a speci-
fied turning speed and different feed rates.
Conclusions considering varying of residual stresses are as follows:
With lower feed rates, a grinding speed exerts a decisive influence on the magni-
tude and variation of the residual stresses in the thin surface layer. With higher
feed rates, however, residual tensile stresses are almost the same at the surface, but
with an increasing cutting speed the layer depth with residual tensile stresses gets
reduced (Figure 3.9). Increasing of the cutting speed results in a reduced depth of
material deformation, which is confirmed by the variations of residual stresses.
A turning speed exerts the strongest influence on the depth of the hardened sur-
face layer, whereas the feed rate exerts a major influence on the magnitude of the
residual stresses at the surface. It is also true that increasing of the feed velocity
results in increased tensile residual stresses in the surface. Such a relation holds
regardless of the turning speed chosen, but it is more distinct with lower speeds, and
with both the sharp tool, VB<0.15
mm (a) and with the worn one, VB>0.30
mm (b).
A comparison of the variation and magnitude of the residual stresses at the
specimens with the same cutting speed (v
3
=
100 m/min) and grinding depth (a
=
1.0
mm), using the sharp tool (VB<0.15
mm) and the worn one (VB>0.30) shows
a reduction of tensile residual stresses with feed rate (Figure 3.10). Thus, with the
lowest feed rate, f
1
=
0.04
mm/rev, even compressive stresses occur, which con-
firms a more distinct effect of workpiece material compression in the surface layer.
Figure 3.10, left, shows the influence of a different degree of tool wear with
a cutting speed v
3
of 100
m/min and with the lowest feed rate, f
1
=
0.04
mm/rev.
The results obtained confirm that with a less worn tool the turning process is still
satisfactory, whereas with a more strongly worn tool (VB>0.30
mm) workpiece
material compression in the surface layer predominates, which results in the gen-
eration of compressive residual stresses in the surface. The diagram in Figure 3.10b
shows that in grinding with a cutting speed v
3
of 100
m/min and higher feed rates f
2
and f
3
, and with the sharp or worn tool very similar residual-stress variations are
obtained, the residual-stress variations being somewhat lower and the hardened
(a) (b)
Figure 3.9. Influence of feed rate (f
1
, f
2
, f
3
) on residual stresses after turning with cutting
speed v
3
= 100 m/min, either with (a) sharp or (b) worn tool [19]