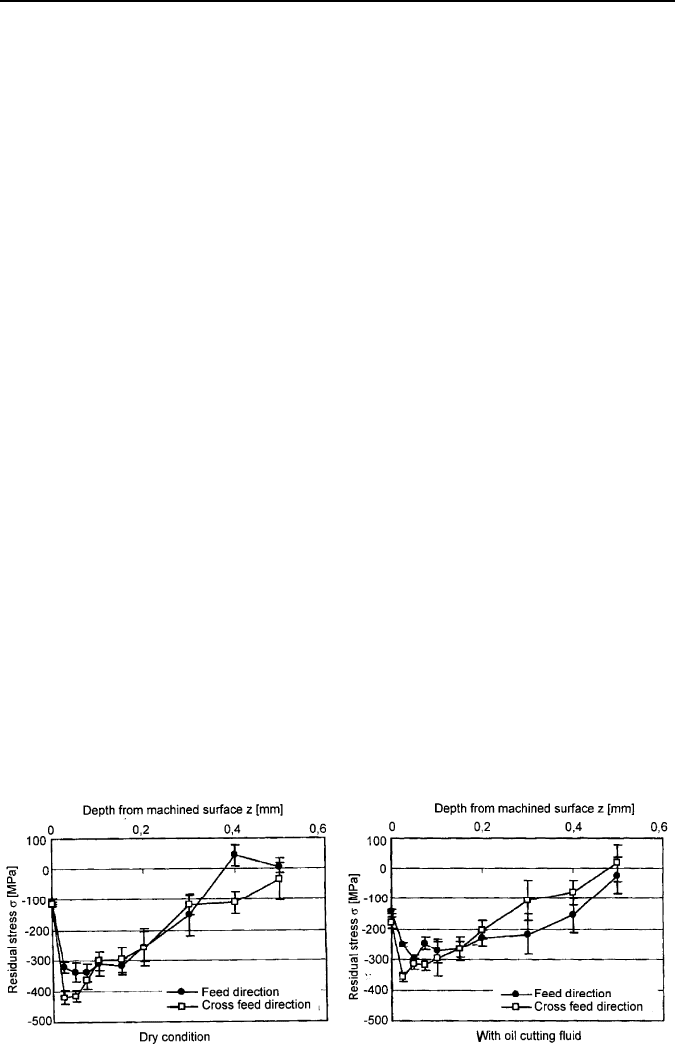
3 Residual Stresses and Microstructural Modifications 103
nent with this tool would be extended regarding residual stress fields.
Li et al. [39] carried out an FEM study on residual stresses induced by high-
speed end milling of hardened steel SKD11. Milling of hardened steel SKD11 is
usually a finishing process, therefore a stable cutting process must be guaranteed
first. Residual stresses were studied in this paper with a finite-element method
(FEM) for its significant influence on the quality of machined part. A two-dimen-
sion (2D) fully thermomechanical coupled finite-element (FE) model was employ-
ed to evaluate residual stress in a machined component. The same cutting tools
were employed to model continuous feed milling process. Residual-stress profiles
were obtained after end-milling and stress-relaxation stages. The predicted resid-
ual-stress profiles corresponded to experimental results.
Hardened steel SKD11 has wide applications in the mold and die industry. It is
also a difficult-to-cut material due to its high strength and hardness that varies from
60 to 62 HRC. With the development of cutting tools, hard milling is becoming
a feasible approach to traditional grinding and electron discharge machining
(EDM) for its high machining efficiency. However, hard milling is often used as a
finishing process, a stable cutting process should be guaranteed to obtain satisfied
machining precision. Residual stresses existing in a machined product have a major
influence on the quality of the machined part, in particular, its fatigue life and cor-
rosion resistance. Predicting the distribution of residual stress induced by cutting
process is very important.
As evidence of the ability of the simulation procedure to model residual stress,
a comparison was carried out between FEM predictions and experimental meas-
urements. Predicted residual-stress profiles were obtained until the workpiece was
unloaded and left to cool down to room temperature. Figure 3.47 shows the com-
parison of the two residual stress between FEM and experiment. Although both of
the curves do not match exactly, the FE model correctly estimates the in-depth RS
profiles showing the same trend and starting with almost the same surface value as
the experimental one.
In general, an exact match between FEM and experimental results could not be
expected because of the different sources of errors in each of them. The main
source of errors encountered in FEM modeling could be summarized as follows
(a) (b)
Figure 3.46. Residual stress profiles measured from the machined surface: (a) dry condition;
and (b) with oil cutting fluid [38]