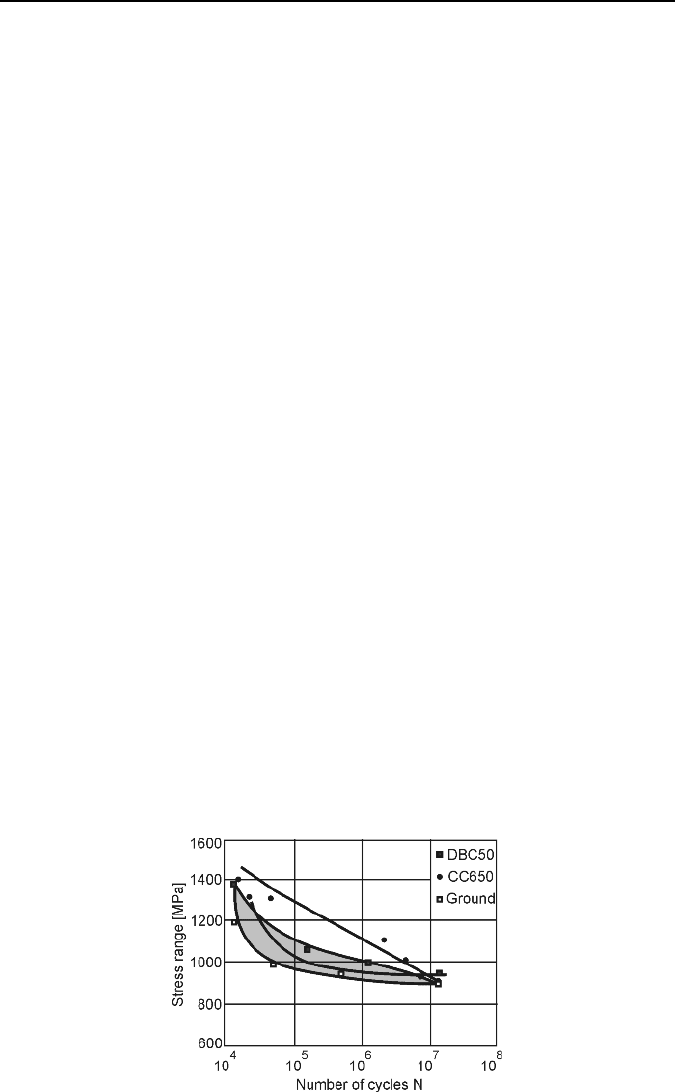
96 J. Grum
Figure 3.38 shows the fatigue life in the S−N curves. For the same applied load,
a longer fatigue life was obtained on specimens turned with PCBN tools, although
for a stress range of approximately 900 MPa, a run-out was obtained for both cut-
ting tool materials. The shadowed area details the bounds of the results for the
ground specimens that were not as consistent, however, the fatigue life was similar
to that obtained with the specimens turned with CC650.
García Navas et al. [33] presented electrodischarge machining (EDM) versus
hard turning and grinding with emphasis on comparison of residual stresses and
surface integrity in AISI 01 tool steel. Electrodischarge machining (EDM) appears
as an alternative to grinding and hard turning for the machining of tool steels be-
cause EDM allows the machining of any type of conducting material, regardless of
its hardness.
Nevertheless, other factors must be taken into account in the selection of machin-
ing processes, especially in the case of crucial parts. These factors are related with
surface integrity: residual stresses, hardness and structural changes generated by the
machining processes. Production grinding generates compressive stresses at the
surface, and a slight tensile peak, accompanied by a decrease in hardness beneath it.
No microstructural changes are noticeable. Hard turning generates slight tensile
stresses in the surface, accompanied by an increase in hardness and in the amount of
retained austenite. Below the surface, residual stresses in compression are obtained
as well as a decrease in hardness and in the volume fraction of retained austenite.
Wire electrodischarge machining (WEDM) generates tensile residual stresses at the
surface layer accompanied by the formation of a superficial “white layer” where
there is a noticeable increase of the volume fraction of retained austenite and of the
hardness. Consequently, among the three machining processes studied, WEDM is
the most detrimental to surface integrity and, consequently, to the service life of
the machined parts, because it promotes crack formation and propagation.
Figure 3.39 shows residual-stress profiles generated by each machining process.
The depth profiles of the non-null components of the stress tensor (the two normal
components (σ
11
and σ
22
) and the shear components σ
12
) are represented in each
graph.
Both WEDM processes generate tensile residual stresses at the surface that in-
crease up to a maximum tensile peak at 20 to 30
μm below the surface, before tend-
Figure 3.38. Fatigue life of finish turned and ground hardened bearing steel [32]