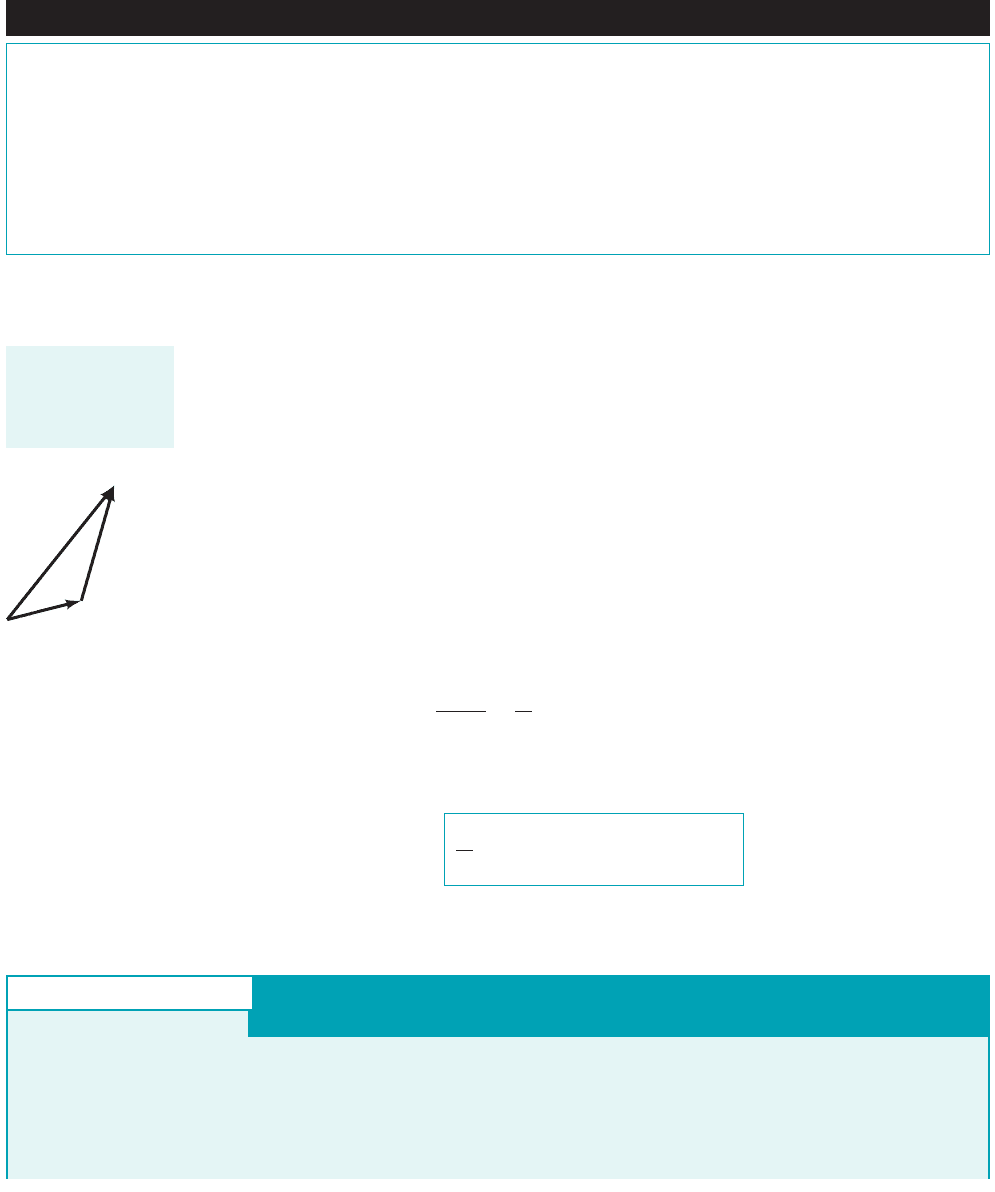
For steady flow involving more than one stream of a specific fluid or more than one specific
fluid flowing through the control volume,
The variety of example problems solved above should give the correct impression that the
fixed, nondeforming control volume is versatile and useful.
a
m
#
in
⫽
a
m
#
out
196 Chapter 5 ■ Finite Control Volume Analysis
Fluids in the News
New 1.6 GPF standards Toilets account for approximately 40%
of all indoor household water use. To conserve water, the new
standard is 1.6 gallons of water per flush (gpf). Old toilets use
up to 7 gpf; those manufactured after 1980 use 3.5 gpf. Neither
are considered low-flush toilets. A typical 3.2 person household
in which each person flushes a 7-gpf toilet 4 times a day uses
32,700 gallons of water each year; with a 3.5-gpf toilet the
amount is reduced to 16,400 gallons. Clearly the new 1.6-gpf
toilets will save even more water. However, designing a toilet
that flushes properly with such a small amount of water is not
simple. Today there are two basic types involved: those that are
gravity powered and those that are pressure powered. Gravity
toilets (typical of most currently in use) have rather long cycle
times. The water starts flowing under the action of gravity and the
swirling vortex motion initiates the siphon action which builds to
a point of discharge. In the newer pressure-assisted models, the
flowrate is large but the cycle time is short and the amount of
water used is relatively small. (See Problem 5.32.)
5.1.3 Moving, Nondeforming Control Volume
It is sometimes necessary to use a nondeforming control volume attached to a moving reference
frame. Examples include control volumes containing a gas turbine engine on an aircraft in flight,
the exhaust stack of a ship at sea, and the gasoline tank of an automobile passing by.
As discussed in Section 4.4.6, when a moving control volume is used, the fluid velocity rela-
tive to the moving control volume 1relative velocity2is an important flow field variable. The relative
velocity, W, is the fluid velocity seen by an observer moving with the control volume. The control
volume velocity, is the velocity of the control volume as seen from a fixed coordinate system.
The absolute velocity, V, is the fluid velocity seen by a stationary observer in a fixed coordinate sys-
tem. These velocities are related to each other by the vector equation
(5.14)
as illustrated by the figure in the margin. This is the same as Eq. 4.22, introduced earlier.
For a system and a moving, nondeforming control volume that are coincident at an instant
of time, the Reynolds transport theorem 1Eq. 4.232for a moving control volume leads to
(5.15)
From Eqs. 5.1 and 5.15, we can get the control volume expression for conservation of mass
1the continuity equation2for a moving, nondeforming control volume, namely,
(5.16)
Some examples of the application of Eq. 5.16 follow.
0
0t
冮
cv
r dV⫺⫹
冮
cs
rW ⴢ nˆ dA ⫽ 0
DM
sys
Dt
⫽
0
0t
冮
cv
r dV⫺⫹
冮
cs
rW ⴢ nˆ dA
V ⫽ W ⫹ V
cv
V
cv
,
Some problems are
most easily solved
by using a moving
control volume.
V
V
CV
W
GIVEN An airplane moves forward at a speed of as
shown in Fig. E5.6a. The frontal intake area of the jet engine is
and the entering air density is A stationary
observer determines that relative to the earth, the jet engine
exhaust gases move away from the engine with a speed of
0.736 kg
Ⲑ
m
3
.
0.80 m
2
971 km
Ⲑ
hr
Conservation of Mass—Compressible Flow with
a Moving Control Volume
The engine exhaust area is , and the exhaust
gas density is
FIND Estimate the mass flowrate of fuel into the engine in
kg
Ⲑ
hr.
0.515 kg
Ⲑ
m
3
.
0.558 m
2
1050 km
Ⲑ
hr.
E
XAMPLE 5.6
JWCL068_ch05_187-262.qxd 9/23/08 9:54 AM Page 196