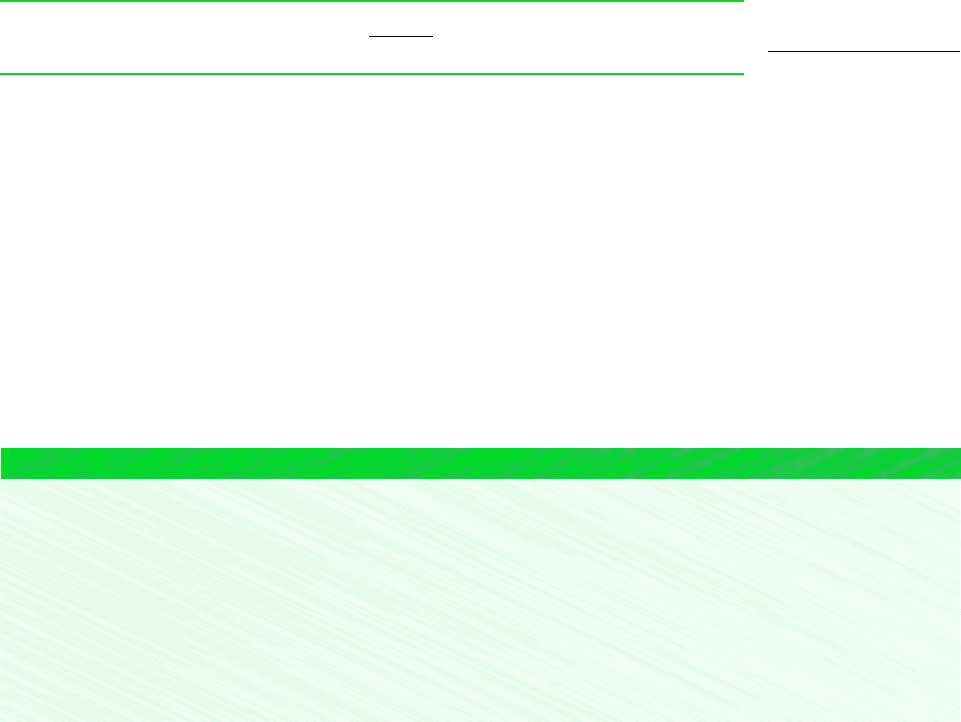
9.7 Regenerative Gas Turbines 401
First, refer to Fig. 9.15a. Since a finite temperature difference between the streams is
required for heat transfer to occur, the temperature of the cold stream at each loca-
tion, denoted by the coordinate z, is less than that of the hot stream. In particular,
the temperature of the colder stream as it exits the heat exchanger is less than the
temperature of the incoming hot stream. If the heat transfer area were increased,
providing more opportunity for heat transfer between the two streams, there would be
a smaller temperature difference at each location.
In the limiting case of infinite heat transfer area, the temperature difference would
approach zero at all locations, as illustrated in Fig. 9.15b, and the heat transfer would
approach reversibility. In this limit, the exit temperature of the colder stream would
approach the temperature of the incoming hot stream. Thus, the highest possible
temperature that could be achieved by the colder stream is the temperature of the
incoming hot gas.
Referring again to the regenerator of Fig. 9.14, we can conclude from the discussion of
Fig. 9.15 that the maximum theoretical value for the temperature T
x
is the turbine exhaust
temperature T
4
, obtained if the regenerator were operating reversibly. The regenerator effec-
tiveness,
reg
, is a parameter that gauges the departure of an actual regenerator from such an
ideal regenerator. The regenerator effectiveness is defined as the ratio of the actual enthalpy
increase of the air flowing through the compressor side of the regenerator to the maximum
theoretical enthalpy increase. That is,
(9.27)
As heat transfer approaches reversibility, h
x
approaches h
4
and tends to unity (100%).
In practice, regenerator effectiveness values typically range from 60 to 80%, and thus the
temperature T
x
of the air exiting on the compressor side of the regenerator is normally well
below the turbine exhaust temperature. To increase the effectiveness above this range would
require greater heat transfer area, resulting in equipment costs that might cancel any advan-
tage due to fuel savings. Moreover, the greater heat transfer area that would be required for
a larger effectiveness can result in a significant frictional pressure drop for flow through the
regenerator, thereby affecting overall performance. The decision to add a regenerator is in-
fluenced by considerations such as these, and the final decision is primarily an economic
one.
In Example 9.7, we analyze an air-standard Brayton cycle with regeneration and explore
the effect on thermal efficiency as the regenerator effectiveness varies.
h
reg
h
reg
h
x
h
2
h
4
h
2
EXAMPLE 9.7 Brayton Cycle with Regeneration
A regenerator is incorporated in the cycle of Example 9.4. (a) Determine the thermal efficiency for a regenerator effective-
ness of 80%. (b) Plot the thermal efficiency versus regenerator effectiveness ranging from 0 to 80%.
SOLUTION
Known: A regenerative gas turbine operates with air as the working fluid. The compressor inlet state, turbine inlet temper-
ature, and compressor pressure ratio are known.
Find: For a regenerator effectiveness of 80%, determine the thermal efficiency. Also plot the thermal efficiency versus the
regenerator effectiveness ranging from 0 to 80%.
regenerator effectiveness