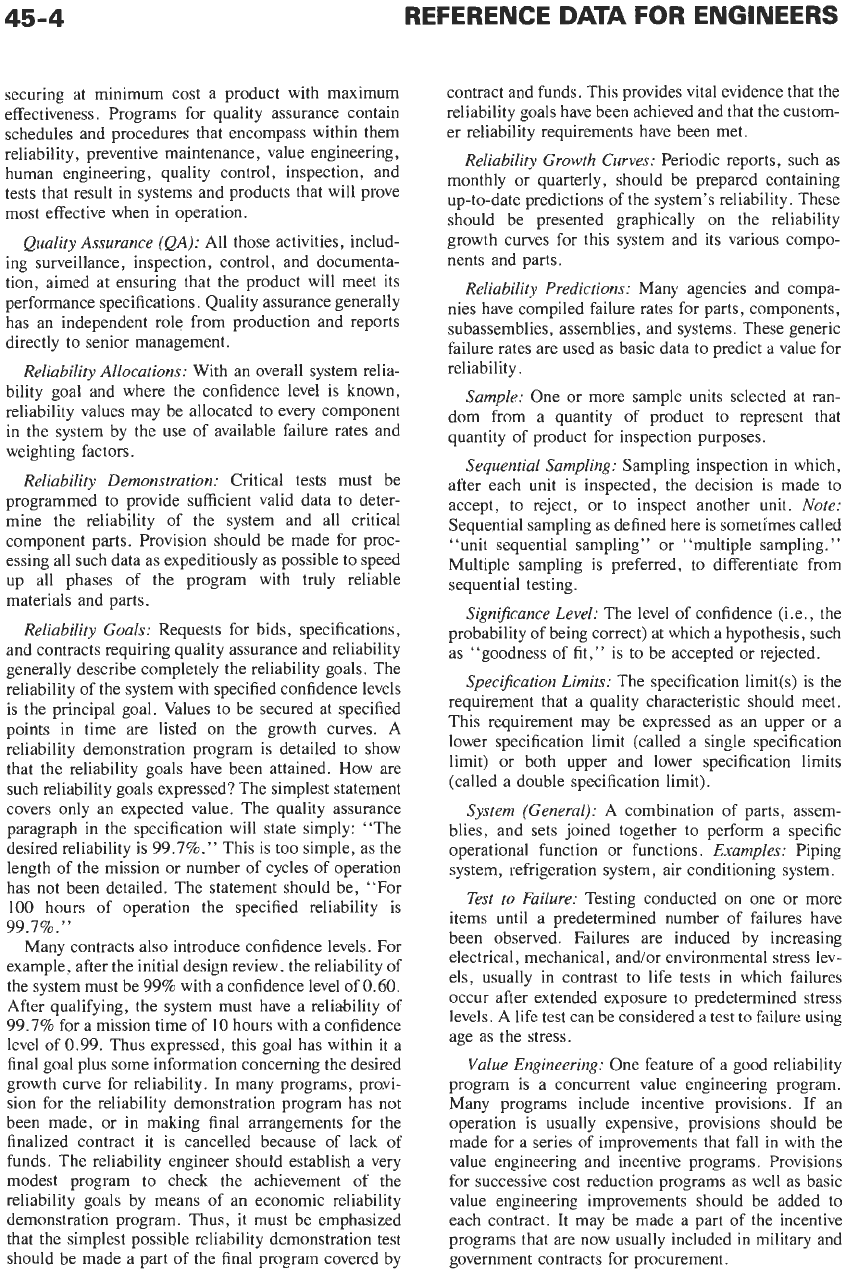
45-4
REFERENCE
DATA
FOR ENGINEERS
securing at minimum cost a product with maximum
effectiveness. Programs for quality assurance contain
schedules and procedures that encompass within them
reliability, preventive maintenance, value engineering,
human engineering, quality control, inspection, and
tests that result in systems and products that will prove
most effective when in operation.
Quality Assurance (QA):
All those activities, includ-
ing surveillance, inspection, control, and documenta-
tion, aimed at ensuring that the product will meet its
performance specifications, Quality assurance generally
has an independent role from production and reports
directly to senior management.
Reliability Allocations:
With an overall system relia-
bility goal and where the confidence level is known,
reliability values may be allocated to every component
in the system by the use of available failure rates and
weighting factors.
Reliability Demonstration:
Critical tests must be
programmed to provide sufficient valid data to deter-
mine the reliability
of the system and all critical
component parts. Provision should be made for proc-
essing all such data as expeditiously as possible
to
speed
up all phases of the program with truly reliable
materials and parts.
Reliability Goals:
Requests for bids, specifications,
and contracts requiring quality assurance and reliability
generally describe completely the reliability goals. The
reliability of the system with specified confidence levels
is the principal goal. Values to be secured at specified
points in time are listed
on
the growth curves. A
reliability demonstration program is detailed to show
that the reliability goals have been attained. How are
such reliability goals expressed? The simplest statement
covers only an expected value. The quality assurance
paragraph
in
the specification will state simply: “The
desired reliability is 99.7%.” This is too simple, as the
length of the mission or number of cycles of operation
has not been detailed. The statement should be, “For
100
hours of operation the specified reliability is
99.7%.”
Many contracts also introduce confidence levels. For
example, after the initial design review, the reliability of
the system must be 99% with a confidence level of
0.60.
After qualifying, the system must have a reliability of
99.7% for a mission time of
10
hours with a confidence
level of 0.99. Thus expressed, this goal has within it a
final goal plus some information concerning the desired
growth curve
for reliability.
In
many programs, pros+
sion for the reliability demonstration program has not
been made, or in making final arrangements for the
finalized contract it is cancelled because
of
lack of
funds. The reliability engineer should establish a very
modest program to check the achievement of the
reliability goals by means of an economic reliability
demonstration program. Thus, it must be emphasized
that the simplest possible reliability demonstration test
should be made a part of the final program covered by
contract and funds. This provides vital evidence that the
reliability goals have been achieved and that the custom-
er reliability requirements have been met.
Reliability Growth Curves:
Periodic reports, such as
monthly or quarterly, should be prepared containing
up-to-date predictions of the system’s reliability. These
should be presented graphically
on
the reliability
growth curves for this system and its various compo-
nents and parts.
Reliability Predictions:
Many agencies and compa-
nies have compiled failure rates for parts, components,
subassemblies, assemblies, and systems. These generic
failure rates are used as basic data to predict a value for
reliability.
Sample:
One or more sample units selected at ran-
dom from a quantity of product to represent that
quantity of product for inspection purposes.
Sequential Sampling:
Sampling inspection in which,
after each unit is inspected, the decision is made to
accept, to reject, or to inspect another unit.
Note:
Sequential sampling as defined here is sometimes called
“unit sequential sampling” or “multiple sampling.”
Multiple sampling is preferred, to differentiate from
sequential testing.
SigniJicance Level:
The level of confidence (i.e., the
probability of being correct) at which a hypothesis, such
as “goodness of fit,” is to be accepted or rejected.
SpeciJication Limits:
The specification limit(s) is the
requirement that a quality characteristic should meet.
This requirement may be expressed as an upper or a
lower specification limit (called a single specification
limit) or both upper and lower specification limits
(called a double specification limit).
System (General):
A combination of parts, assem-
blies, and sets joined together to perform a specific
operational function or functions.
Examples:
Piping
system, refrigeration system, air conditioning system.
Test
to
Failure:
Testing conducted
on
one or more
items until a predetermined number of failures have
been observed. Failures are induced by increasing
electrical, mechanical, and/or environmental stress lev-
els, usually in contrast to life tests in which failures
occur after extended exposure to predetermined stress
levels.
A
life test can be considered a test to failure using
age as the stress.
Value Engineering:
One feature of a good reliability
program is a concurrent value engineering program.
Many programs include incentive provisions. If an
operation is usually expensive, provisions should be
made for a series of improvements that fall
in
with the
value engineering and incentive programs. Provisions
for successive cost reduction programs as well as basic
value engineering improvements should be added to
each contract. It may be made a part of the incentive
programs that are now usually included in military and
government contracts for procurement.