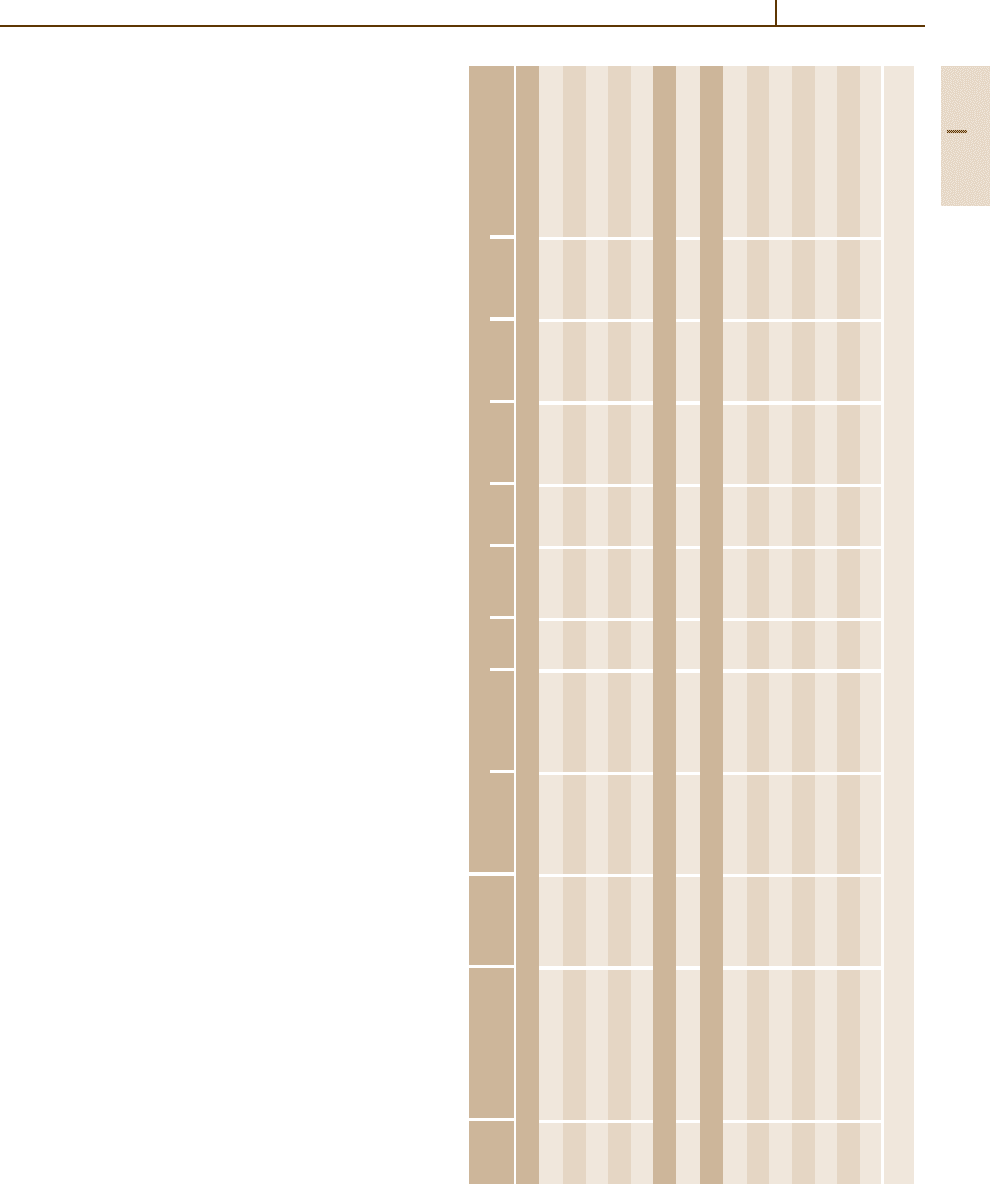
Metals 1.5 Iron and Steels 259
However, these embrittling mechanisms will not impair
the behavior at high operating temperatures if taken into
account properly, but will deteriorate the toughness after
cooling to room temperature. Heating to temperatures
above the range of occurrence of the embrittling phases
followed by sufficiently fast cooling will suppress the
embrittling effects.
The Cr and Ni alloyed austenitic steels possess
a higher temperature strength and better ductility, tough-
ness, and weldability. The susceptibility to embrittling
effects is considerably lower. At Ni contents above
30 wt% Ni, they are outside the stability region of the
brittle σ-phase.
The properties of the ferritic-austenitic steels lie be-
tween those of the ferritic and austenitic steels. They
are characterized by a higher fracture toughness, cold
formability, high temperature strength, and weldability
than the fully ferritic grades, and by a higher chemical
resistance in sulphurous gases than the austenitic grades.
It is obvious that the scaling resistance of the
heat-resisting steels will be detrimentally influenced
by any other corrosion mechanism which may be
destroying the oxide layer, e.g., by chemical reac-
tions with other metal oxides, chlorine, or chlorides.
Thus in general, the heat resistance cannot be char-
acterized by a single test method or measuring
parameter but will depend on the specific environmental
conditions.
In Table 3.1-70 chemical compositions of the
most important grades of heat resistant steels are pre-
sented [1.87]. Table 3.1-71 contains some information
about recommended temperature ranges for heat treat-
ment and hot forming. In Tables 3.1-72 and 3.1-73
the mechanical properties at room temperature and at
high temperatures are listed, respectively. Table 3.1-74
shows some physical properties. The ferritic and ferritic-
austenitic steels are magnetisable while the austenitic
grades are nonmagnetic. Qualitative data on the high
temperature behavior in special gas atmospheres are
given in Table 3.1-75. In carburizing atmospheres
carbon can diffuse into the steel, reacting with the
chromium to form chromium carbides which can lead
to embrittlement and reduced scaling resistance due
to chromium depletion in the matrix. Higher Ni and
Si contents reduce the carburization susceptibility. In
sulfur-containing atmospheres, which contain the sul-
fur mostly in the form of SO
2
or H
2
S, the formation
of sulfides at the surface may inhibit the formation
of the protecting oxide layer. Under oxidizing condi-
tions this process will proceed rather slowly, but under
reducing conditions the pick-up of sulfur occurs very
Table 3.1-70 Chemical composition of heat-resistant steels according to SEW [1.87]
Grade
a
Steel ASTM/ Chemical composition (wt%)
designation AISI grade C Si Mn P S Al Cr Ni Others
Ferritic steels
1.4713 X10CrAlSi7 – ≤0.12 0.5–1.0 ≤1 ≤0.04 ≤0.03 0.5–1.0 6.0–8.0 – –
1.4720 X7CrTi12 – ≤0.08 ≤1.0 ≤1 ≤0.04 ≤0.03 – 10.5–12.5 – Ti ≥ 6xwt%Cupto1.0
1.4724 X10CrAlSi13 405 ≤0.12 0.7–1.4 ≤1 ≤0.04 ≤0.03 0.7–1.2 12.0–14.0 – –
1.4742 X10CrAlSi18 430 ≤0.12 0.7–1.4 ≤1 ≤0.04 ≤0.03 0.7–1.2 17.0–19.0 – –
1.4762 X10CrAlSi25 446 ≤0.12 0.7–1.4 ≤1 ≤0.04 ≤0.03 1.2–1.7 23.0–26.0 – –
Ferritic–austenitic steels
1.4821 X15CrNiSi25-4 327 0.10–0.20 0.8–1.5 2.0 ≤0.04 ≤0.03 – 24.0–27.0 3.5–5.5 –
Austenitic steels
1.4878 X10CrNiTi18-10 321 ≤0.12 ≤1 ≤2.0 ≤0.045 ≤0.03 – 17.0–19.0 9.0–12.0 Ti ≥4xwt% C up to 0.8
1.4828 X15CrNiSi20-12 309 ≤0.20 1.5–2.5 ≤2.0 ≤0.045 ≤0.03 – 19.0–21.0 11.0–13.0 –
1.4833 X12CrNi23-12 309S ≤0.08 ≤1 ≤2.0 ≤0.045 ≤0.03 – 21.0–23.0 12.0–15.0 –
1.4845 X8CrNi25-21-12 310S ≤0.15 ≤0.75 ≤2.0 ≤0.045 ≤0.03 – 24.0–26.0 19.0–22.0 –
1.4841 X15CrNiSi25-20 310/314 ≤0.20 1.5–2.5 ≤2.0 ≤0.045 ≤0.03 – 24.0–26.0 19.0–22.0
1.4864 X12NiCrSi36-18 330 ≤0.15 1.0–2.0 ≤2.0 ≤0.030 ≤0.02 – 15.0–17.0 33.0–37.0 –
1.4876 X10NiCrAlTi32-21 B163 ≤0.12 ≤1 ≤2.0 0.030 ≤0.02 0.15–0.6 19.0–23.0 30.0–34.0 Ti 0.15–0.6
a
According to SEW [1.87]
Part 3 1.5