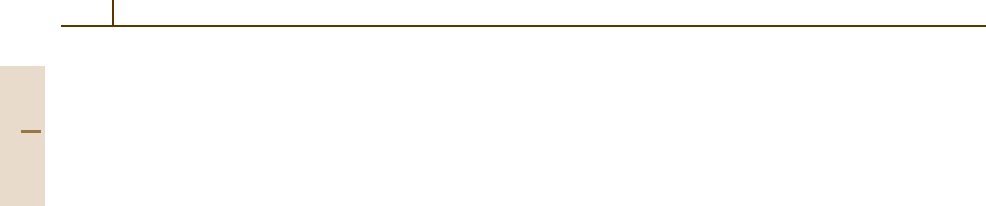
162 Part 3 Classes of Materials
3.1.5 Iron and Steels ................................... 221
3.1.5.1 Phase Relations and Phase
Transformations...................... 222
3.1.5.2 Carbon and Low-Alloy Steels .... 227
3.1.5.3 High-Strength Low-Alloy Steels 240
3.1.5.4 Stainless Steels ....................... 240
3.1.5.5 Heat-Resistant Steels............... 257
3.1.5.6 Tool Steels .............................. 262
3.1.5.7 Cast Irons ............................... 268
3.1.6 Cobalt and Cobalt Alloys ...................... 272
3.1.6.1 Co-Based Alloys ...................... 272
3.1.6.2 Co-Based Hard-Facing Alloys
and Related Materials.............. 274
3.1.6.3 Co-Based Heat-Resistant Alloys,
Superalloys............................. 274
3.1.6.4 Co-Based Corrosion-Resistant
Alloys .................................... 276
3.1.6.5 Co-Based
Surgical Implant Alloys............. 277
3.1.6.6 Cemented Carbides.................. 277
3.1.7 Nickel and Nickel Alloys....................... 279
3.1.7.1 Commercially Pure
and Low-Alloy Nickels ............. 279
3.1.7.2 Highly Alloyed
Ni-Based Materials.................. 279
3.1.7.3 Ni-Based Superalloys............... 284
3.1.7.4 Ni Plating ............................... 288
3.1.8 Copper and Copper Alloys .................... 296
3.1.8.1 Unalloyed Coppers................... 296
3.1.8.2 High Copper Alloys................... 297
3.1.8.3 Brasses .................................. 298
3.1.8.4 Bronzes.................................. 298
3.1.8.5 Copper–Nickel
and Copper–Nickel–
Zinc Alloys .............................. 300
3.1.9 Refractory Metals and Alloys ................ 303
3.1.9.1 Physical Properties .................. 306
3.1.9.2 Chemical Properties................. 308
3.1.9.3 Recrystallization Behavior ........ 311
3.1.9.4 Mechanical Properties.............. 314
3.1.10 Noble Metals and Noble Metal Alloys .... 329
3.1.10.1 Silver and Silver Alloys ............. 330
3.1.10.2 Gold and Gold Alloys ............... 347
3.1.10.3 Platinum Group Metals
and Alloys .............................. 363
3.1.10.4 Rhodium, Iridium, Rhutenium,
Osmium, and their Alloys ......... 386
3.1.11 Lead and Lead Alloys .......................... 407
3.1.11.1 Pure Grades of Lead ................ 407
3.1.11.2 Pb–Sb Alloys........................... 411
3.1.11.3 Pb–Sn Alloys........................... 414
3.1.11.4 Pb–Ca Alloys ........................... 416
3.1.11.5 Pb–Bi Alloys ........................... 419
3.1.11.6 Pb–Ag Alloys........................... 420
3.1.11.7 Pb–Cu, Pb–Te,
and Pb–Cu–Te Alloys ............... 421
3.1.11.8 Pb–As Alloys ........................... 421
3.1.11.9 Lead Cable Sheathing Alloys ..... 421
3.1.11.10 Other Lead Alloys .................... 421
References .................................................. 422
3.1.1 Magnesium and Magnesium Alloys
Magnesium is the lightest structural metal with a density
of 1.74 g cm
−3
. It is produced by two basic processes.
One is the electrolysis of fused anhydrous magnesium
chloride (MgCl
2
) derived from magnesite, brine, or sea-
water, and recently from serpentine ores. The other one
is the thermal reduction of magnesium oxide (MgO) by
ferrosilicon derived from carbonate ores [1.1]. The use
of primary Mg is shown in Fig. 3.1-1. Only one third is
used for structural parts, mainly for castings, while the
major amount of Mg is still used as an alloying element
in Al alloys.
Pure Mg is rarely used for structural applications
due to its poor mechanical properties. Therefore, Al and
Zn have been introduced as major alloying elements
for high-pressure die casting alloys. The main reason
for using magnesium alloys is to lower the weigh load,
predominantly in transportation industries. The weight
reduction amounts to about 30% compared to Al al-
loys and to about 75% compared to steel. Magnesium
has a hexagonal close-packed crystal structure (hcp).
Therefore its deformation properties are poor. At room
temperature slip occurs on the basal plane {0001} in
the 11
¯
20 direction only. In addition to slip on basal
planes the deformation by twinning is also possible, the
twinning system is {10
¯
12}10
¯
11. Twin formation leads
to different behavior of Mg alloys under tensile and
compressive load. With increasing temperature above
200–225
◦
C, prismatic slip planes are activated in ad-
dition. This is of main importance for the processing
wrought magnesium alloys.
Part 3 1.1