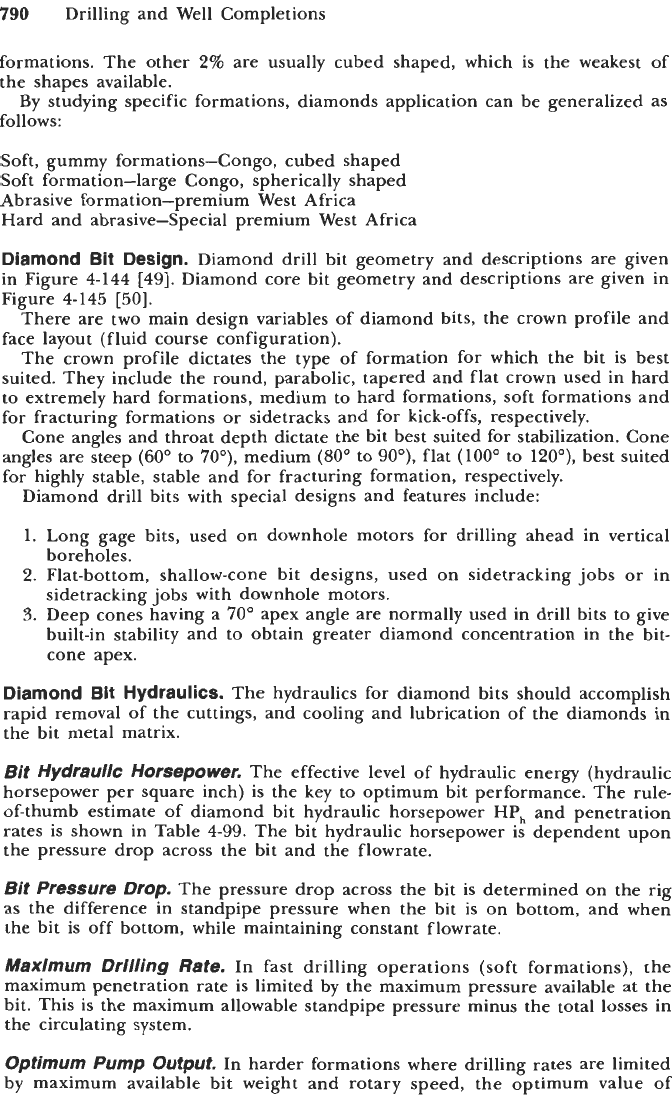
790
Drilling and Well Completions
formations. The other
2%
are usually cubed shaped, which is the weakest of
the shapes available.
By
studying specific formations, diamonds application can be generalized as
follows:
Soft, gummy formations-Congo, cubed shaped
Soft formation-large Congo, spherically shaped
Abrasive formation-premium West Africa
Hard and abrasive-Special premium West Africa
Diamond Bit Design.
Diamond drill bit geometry and descriptions are given
in Figure 4-144 [49]. Diamond core bit geometry and descriptions are given in
Figure 4-145 [50].
There are two main design variables of diamond bits, the crown profile and
face layout (fluid course configuration).
The crown profile dictates the type of formation for which the bit is best
suited. They include the round, parabolic, tapered and flat crown used in hard
to extremely hard formations, medium to hard formations, soft formations and
for fracturing formations or sidetracks and for kick-offs, respectively.
Cone angles and throat depth dictate the bit best suited for stabilization. Cone
angles are steep
(60"
to
70"),
medium
(SO0
to go"), flat (100" to 120°), best suited
for highly stable, stable and for fracturing formation, respectively.
Diamond drill bits with special designs and features include:
1.
Long gage bits, used on downhole motors for drilling ahead in vertical
boreholes.
2.
Flat-bottom, shallow-cone bit designs, used on sidetracking jobs or in
sidetracking jobs with downhole motors.
3.
Deep cones having a
70"
apex angle are normally used in drill bits to give
built-in stability and to obtain greater diamond concentration in the bit-
cone apex.
Diamond Bit
Hydraulics.
The hydraulics for diamond bits should accomplish
rapid removal of the cuttings, and cooling and lubrication of the diamonds in
the bit metal matrix.
Bit Hydrauk Horsepower.
The effective level of hydraulic energy (hydraulic
horsepower per square inch) is the key to optimum bit performance. The rule-
of-thumb estimate of diamond bit hydraulic horsepower
HP,
and penetration
rates is shown in Table 4-99. The bit hydraulic horsepower is dependent upon
the pressure drop across the bit and the flowrate.
Bit Pressure Drop.
The pressure drop across the bit is determined on the rig
as the difference in standpipe pressure when the bit is on bottom, and when
the bit is off bottom, while maintaining constant flowrate.
Maximum Drilling Rate.
In fast drilling operations (soft formations), the
maximum penetration rate is limited by the maximum pressure available at the
bit. This is the maximum allowable standpipe pressure minus the total losses in
the circulating system.
Optimum Pump Output.
In harder formations where drilling rates are limited
by maximum available bit weight and rotary speed, the optimum value of