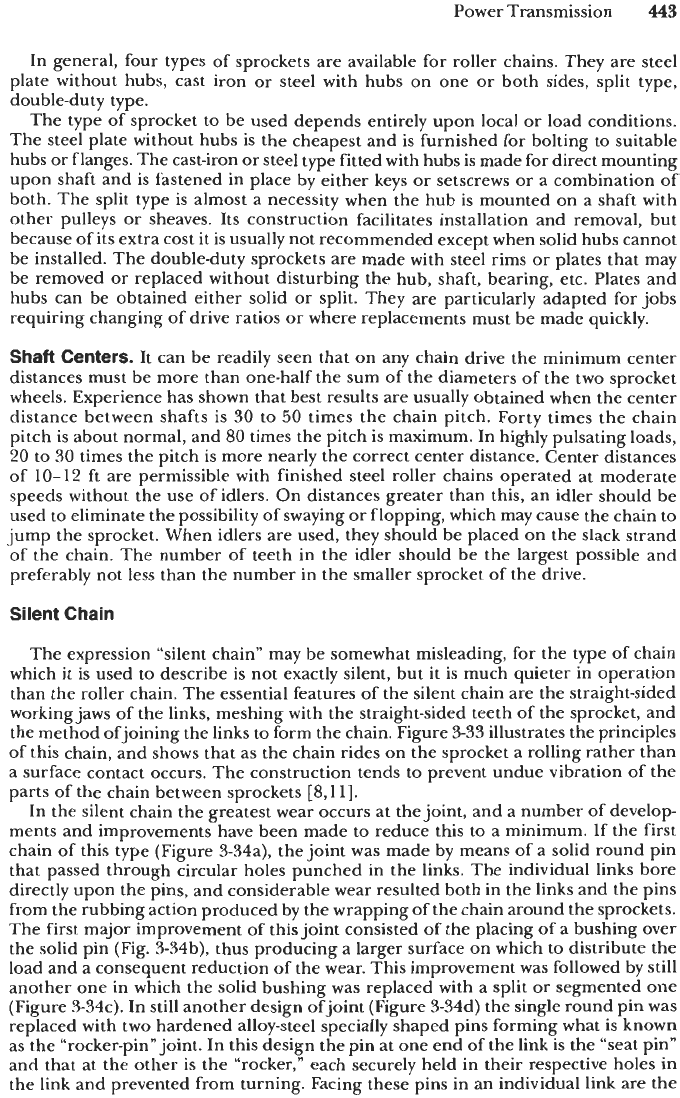
Power Transmission
443
In general, four types of sprockets are available for roller chains. They are steel
plate without hubs, cast iron or steel with hubs on one or both sides, split type,
double-duty type.
The type of sprocket to be used depends entirely upon local or load conditions.
The steel plate without hubs is the cheapest and is furnished for bolting to suitable
hubs
or
flanges. The cast-iron or steel type fitted with hubs is made for direct mounting
upon shaft and is fastened in place by either keys or setscrews or a combination of
both. The split type is almost a necessity when the hub is mounted on a shaft with
other pulleys or sheaves. Its construction facilitates installation and removal, but
because of its extra cost it is usually not recommended except when solid hubs cannot
be installed. The double-duty sprockets are made with steel rims or plates that may
be removed
or
replaced without disturbing the hub, shaft, bearing, etc. Plates and
hubs can be obtained either solid or split. They are particularly adapted for jobs
requiring changing of drive ratios
or
where replacements must be made quickly.
Shaft
Centers.
It can be readily seen that on any chain drive the minimum center
distances must be more than one-half the sum of the diameters
of
the two sprocket
wheels. Experience has shown that best results are usually obtained when the center
distance between shafts is
30
to
50
times the chain pitch. Forty times the chain
pitch is about normal, and
80
times the pitch is maximum. In highly pulsating loads,
20
to
30
times the pitch is more nearly the correct center distance. Center distances
of 10-12 ft are permissible with finished steel roller chains operated at moderate
speeds without the use of idlers. On distances greater than this, an idler should be
used to eliminate the possibility of swaying or flopping, which may cause the chain to
jump the sprocket. When idlers are used, they should be placed on the slack strand
of
the chain, The number of teeth in the idler should be the largest possible and
preferably not less than the number in the smaller sprocket of the drive.
Silent Chain
The expression “silent chain” may be somewhat misleading, for the type of chain
which
it
is used to describe is not exactly silent, but it is much quieter in operation
than the roller chain. The essential features of the silent chain are the straight-sided
working jaws of the links, meshing with the straight-sided teeth
of
the sprocket, and
the method ofjoining the links to form the chain. Figure
3-33
illustrates the principles
of this chain, and shows that as the chain rides on the sprocket a rolling rather than
a surface contact occurs. The construction tends to prevent undue vibration of the
parts of the chain between sprockets
[8,11].
In the silent chain the greatest wear occurs at the joint, and a number of develop-
ments and improvements have been made to reduce this to a minimum.
If
the first
chain of this type (Figure 3-34a), the joint was made by means of a solid round pin
that passed through circular holes punched in the links. The individual links bore
directly upon the pins, and considerable wear resulted both in the links and the pins
from the rubbing action produced by the wrapping of the chain around the sprockets.
The first major improvement of this joint consisted
of
the placing of a bushing over
the solid pin (Fig. 3-34b), thus producing a larger surface on which to distribute the
load and a consequent reduction of the wear. This improvement was followed by still
another one in which the solid bushing was replaced with a split or segmented one
(Figure 3-34c). In still another design ofjoint (Figure 3-34d) the single round pin was
replaced with two hardened alloy-steel specially shaped pins forming what is known
as the “rocker-pin” joint. In this design the pin at one end of the link is the “seat pin”
and that at the other is the “rocker,” each securely held in their respective holes in
the link and prevented from turning. Facing these pins in
an
individual link are the