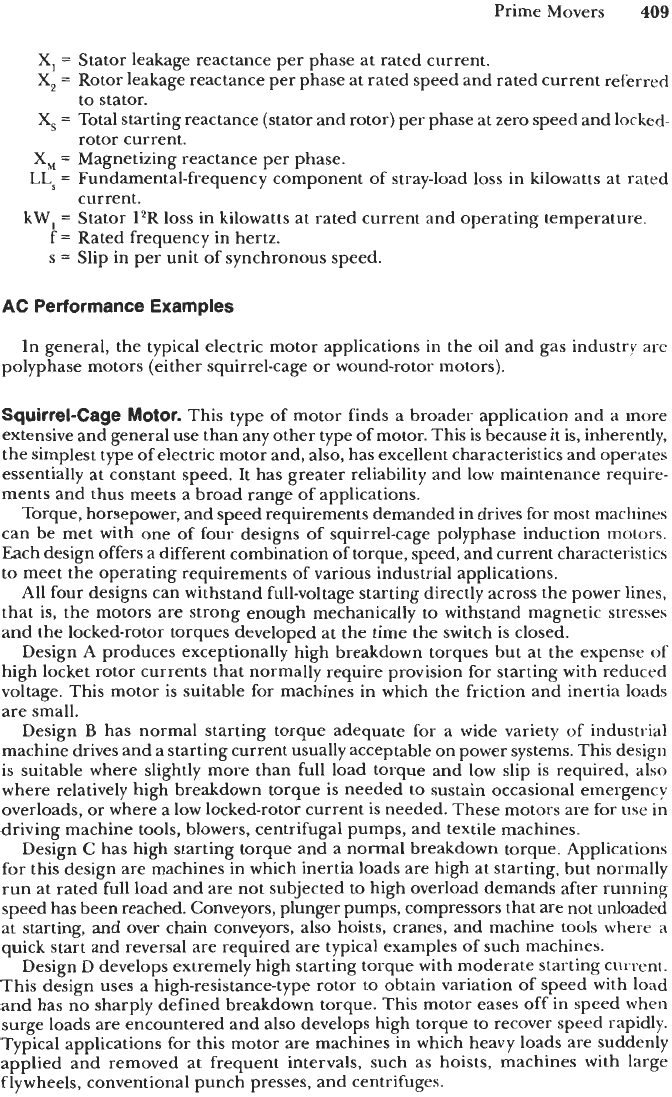
Prime Movers
409
X,
=
Stator leakage reactance per phase at rated current.
X,
=
Rotor leakage reactance per phase at rated speed and rated current referred
X,
=
Total starting reactance (stator and rotor) per phase at zero speed and locked-
X,
=
Magnetizing reactance per phase.
LLs
=
Fundamental-frequency component of stray-load
loss
in kilowatts at rated
to stator.
rotor current.
current.
kW,
=
Stator
12R
loss
in kilowatts at rated current and operating temperature.
f
=
Rated frequency in hertz.
s
=
Slip in per unit of synchronous speed.
AC
Performance
Examples
In general, the typical electric motor applications in the oil and gas industry arc
polyphase motors (either squirrel-cage or wound-rotor motors).
SqUirrel-Cage Motor.
This type of motor finds a broader application and a more
extensive and general use than any other type of motor. This is because it is, inherently,
the simplest type of electric motor and, also, has excellent characteristics and operates
essentially at constant speed. It has greater reliability and low maintenance require-
ments and thus meets a broad range of applications.
Torque, horsepower, and speed requirements demanded in drives for most machines
can be met with one of four designs of squirrel-cage polyphase induction motors.
Each design offers a different combination of torque, speed, and current characteristics
to meet the operating requirements of various industrial applications.
All
four designs can withstand full-voltage starting directly across the power lines,
that
is,
the motors are strong enough mechanically to withstand magnetic stresses
and the locked-rotor torques developed at the time the switch is closed.
Design
A
produces exceptionally high breakdown torques but at the expense of
high locket rotor currents that normally require provision for starting with reduced
voltage. This motor is suitable for machines in which the friction and inertia loads
are small.
Design
B
has normal starting torque adequate for
a
wide variety of industrial
machine drives and a starting current usually acceptable on power systems. This design
is suitable where slightly more than full load torque and low slip is required, also
where relatively high breakdown torque is needed to sustain occasional emergency
overloads, or where a low locked-rotor current is needed. These motors are for use in
driving machine tools, blowers, centrifugal pumps, and textile machines.
Design
C
has high starting torque and a normal breakdown torque. Applications
for this design are machines in which inertia loads are high at starting, but normally
run at rated full load and are not subjected to high overload demands after running
speed has been reached. Conveyors, plunger pumps, compressors that are not unloaded
at starting, and over chain conveyors, also hoists, cranes, and machine tools where
a
quick start and reversal are required are typical examples of such machines.
Design
D
develops extremely high starting torque with moderate starting current.
This design uses a high-resistance-type rotor to obtain variation of speed with load
and has no sharply defined breakdown torque. This motor eases off in speed when
surge loads are encountered and also develops high torque to recover speed rapidly.
Typical applications for this motor are machines in which heavy loads are suddenly
applied and removed at frequent intervals, such as hoists, machines with large
flywheels, conventional punch presses, and centrifuges.