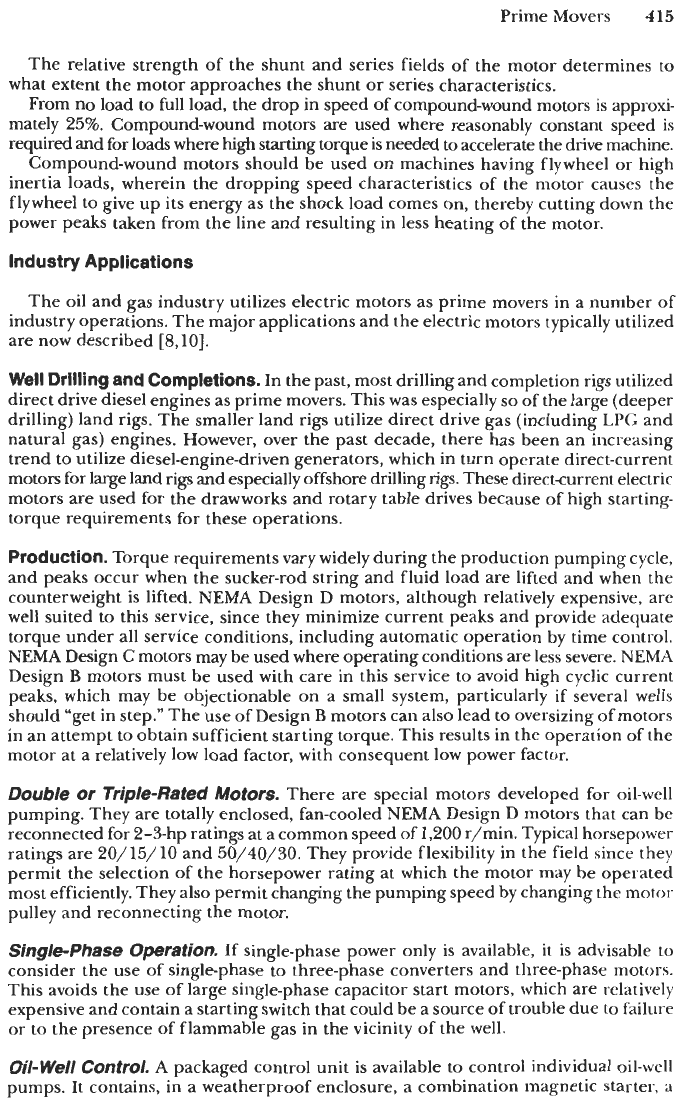
Prime Movers
415
The relative strength of the shunt and series fields of the motor determines to
what extent the motor approaches the shunt or series characteristics.
From no load to full load, the drop in speed
of
compound-wound motors
is
approxi-
mately 25%. Compound-wound motors are used where reasonably constant speed is
required and for loads where
high
starting torque is needed to accelerate the drive machine.
Compound-wound motors should be used on machines having flywheel or high
inertia loads, wherein the dropping speed characteristics of the motor causes the
flywheel to give up its energy as the shock load comes on, thereby cutting down the
power peaks taken from the line and resulting in less heating of the motor.
Industry Applications
The oil and gas industry utilizes electric motors as prime movers in a number of
industry operations. The major applications and the electric motors typically utilized
are now described [8,10].
Well
Drilling and Completions.
In the past, most drilling and completion rigs utilized
direct drive diesel engines as prime movers. This was especially
so
of the large (deeper
drilling) land rigs. The smaller land rigs utilize direct drive gas (including
LPG
and
natural gas) engines. However, over the past decade, there has been an increasing
trend to utilize diesel-enginedriven generators, which in turn operate direct-current
motors for large land rigs
and
especially offshore drilling rigs. These directcurrent electric
motors are used for the drawworks and rotary table drives because of high starting-
torque requirements for these operations.
Production.
Torque requirements vary widely during the production pumping cycle,
and peaks occur when the sucker-rod string and fluid load are lifted and when the
counterweight is lifted. NEMA Design D motors, although relatively expensive, are
well suited to this service, since they minimize current peaks and provide adequate
torque under all service conditions, including automatic operation by time control.
NEMA Design C motors
may
be used where
operating
conditions are less severe. NEMA
Design
B
motors must be used with care in this service to avoid high cyclic current
peaks, which may be objectionable on a small system, particularly
if
several wells
should “get in step.” The use of Design
B
motors can also lead to oversizing
of
motors
in an attempt to obtain sufficient starting torque. This results in the operation of the
motor at a relatively low load factor, with consequent low power factor.
Double
Or
Tripe-Rated
Motors.
There are special motors developed for oil-well
pumping. They are totally enclosed, fan-cooled NEMA Design D motors that can be
reconnected for 2-3-hp ratings at a common speed of 1,200 r/min. Typical horsepower
ratings are 20/15/10 and 50/40/30. They provide flexibility in the field since they
permit the selection of the horsepower rating at which the motor may be operated
most efficiently. They also permit changing the pumping speed by changing the motor
pulley and reconnecting the motor.
Singk-Phase
Operation.
If single-phase power only is available, it is advisable
to
consider the use of single-phase to three-phase converters and three-phase motors.
This avoids the use
of
large single-phase capacitor start motors, which are relatively
expensive and contain a starting switch that could be a source
of
trouble due to failure
or to the presence of flammable gas in the vicinity of the well.
Oil- Well
Control.
A
packaged control unit is available to control individual oil-well
pumps. It contains, in a weatherproof enclosure, a combination magnetic starter,
a