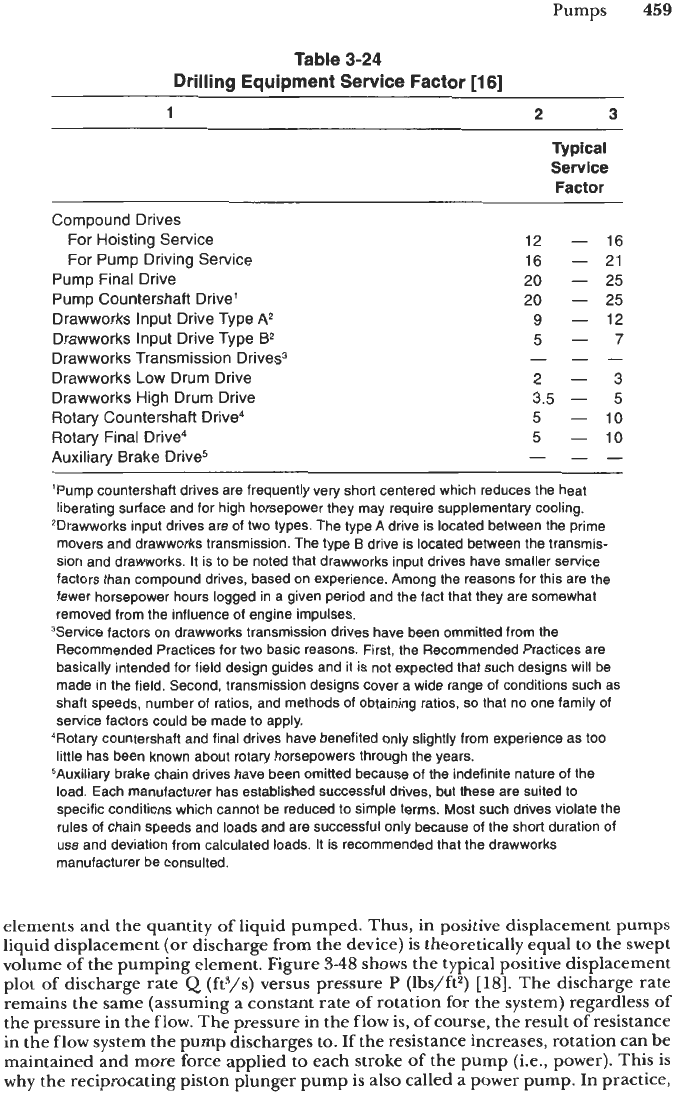
Pumps
459
Table
3-24
Drilling Equipment Service Factor
[16]
1 2
3
Typical
Service
Factor
Compound Drives
For Hoisting Service
For Pump Driving Service
Pump
Final
Drive
Pump
Countershaft
Drive'
Drawworks
Input
Drive
Type
A*
Drawworks
Input
Drive
Type
B2
Drawworks Transmission Drives3
Drawworks Low Drum Drive
Drawworks High
Drum
Drive
Rotary Countershaft Drive4
Rotary
Final
Drive4
Auxiliarv
Brake
Drive5
12
-
16
16
-
21
20
-
25
20
-
25
9
-
12
5-
7
2-
3
3.5
-
5
5
-
10
5
-
10
-
--
-
--
'Pump countershaft drives are frequently very short centered which reduces the heat
liberating surface and for high horsepower they may require supplementaty cooling.
2Drawworks input drives are of two types. The type A drive is located between the prime
movers and drawworks transmission. The type
B
drive is located between the transmis-
sion and drawworks. It is
to
be noted that drawworks input drives have smaller service
factors than compound drives, based on experience. Among the reasons for this are the
fewer horsepower hours logged in a given period and the fact that they are somewhat
removed from the influence of engine impulses.
3Servi~e factors on drawworks transmission drives have been ommitted from the
Recommended Practices for
two
basic reasons. First, the Recommended Practices are
basically intended for field design guides and it is not expected that such designs will be
made in the field. Second, transmission designs cover a wide range of conditions such as
shaft speeds, number of ratios, and methods of obtaining ratios,
so
that no one family
of
service factors could be made to apply.
4R~tary countershaft and final drives have benefited only slightly from experience as too
little has been known about rotary horsepowers through the years.
5Auxiliary brake chain drives have been omitted because of the indefinite nature of the
load. Each manufacturer has established successful drives, but these are suited to
specific conditions which cannot be reduced to simple terms. Most such drives violate the
rules of chain speeds and loads and are successful only because of the short duration of
use
and deviation from calculated loads. It is recommended that the drawworks
manufacturer be consulted.
elements and the quantity of liquid pumped. Thus, in positive displacement pumps
liquid displacement
(or
discharge from the device) is theoretically equal to the swept
volume of the pumping element. Figure
3-48
shows the typical positive displacement
plot
of
discharge rate
Q
(fP/s) versus pressure P (lbs/ft2)
[HI.
The discharge rate
remains the same (assuming a constant rate of rotation for the system) regardless
of
the pressure in the flow. The pressure in the
flow
is,
of
course, the result of resistance
in the flow system the pump discharges to. If the resistance increases, rotation can be
maintained and more force applied
to
each stroke
of
the pump (i.e., power). This
is
why the reciprocating piston plunger pump is also called a power pump. In practice,