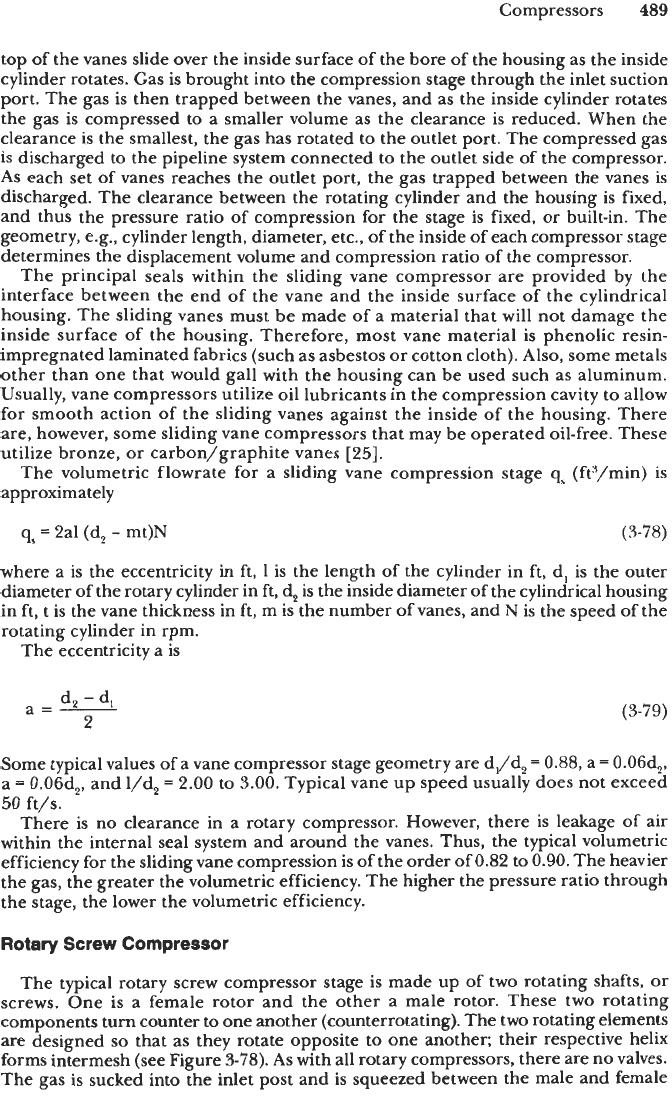
Compressors
489
top of the vanes slide over the inside surface of the bore of the housing as the inside
cylinder rotates. Gas is brought into the compression stage through the inlet suction
port. The gas is then trapped between the vanes, and as the inside cylinder rotates
the gas is compressed to a smaller volume as the clearance is reduced. When the
clearance is the smallest, the gas has rotated to the outlet port. The compressed gas
is discharged to the pipeline system connected to the outlet side of the compressor.
As each set of vanes reaches the outlet port, the gas trapped between the vanes is
discharged. The clearance between the rotating cylinder and the housing is fixed,
and thus the pressure ratio of compression for the stage is fixed,
or
built-in. The
geometry, e.g., cylinder length, diameter, etc., of the inside of each compressor stage
determines the displacement volume and compression ratio of the compressor.
The principal seals within the sliding vane compressor are provided by the
interface between the end of the vane and the inside surface of the cylindrical
housing. The sliding vanes must be made of a material that will not damage the
inside surface of the housing. Therefore, most vane material is phenolic resin-
impregnated laminated fabrics (such as asbestos
or
cotton cloth). Also, some metals
other than one that would gall with the housing can be used such as aluminum.
Usually, vane compressors utilize oil lubricants in the compression cavity to allow
for smooth action of the sliding vanes against the inside of the housing. There
are, however, some sliding vane compressors that may be operated oil-free. These
utilize bronze,
or
carbon/graphite vanes
[25].
The volumetric flowrate for a sliding vane compression stage
q,
(ft”/min) is
approximately
q,
=
2al (d,
-
mt)N
(3-78)
where a is the eccentricity in ft,
1
is the length of the cylinder in ft, d, is the outer
diameter of the rotary cylinder in ft,
4
is the inside diameter of the cylindrical housing
in ft, t is the vane thickness in ft, m is the number of vanes, and
N
is the speed of the
rotating cylinder in rpm.
The eccentricity a is
a=- d,
-
d,
2
(3-79)
Some typical values of a vane compressor stage geometry are dJd,
=
0.88,
a
=
0.06d2,
a
=
0.06d2, and l/d,
=
2.00 to
3.00.
Typical vane up speed usually does not exceed
50
ft/s.
There is no clearance in a rotary compressor. However, there is leakage
of
air
within the internal seal system and around the vanes. Thus, the typical volumetric
efficiency for the sliding vane compression
is
of the order
of
0.82
to
0.90.
The heavier
the gas, the greater the volumetric efficiency. The higher the pressure ratio through
the stage, the lower the volumetric efficiency.
Rotary
Screw
Compressor
The typical rotary screw compressor stage is made up of two rotating shafts, or
screws. One is a female rotor and the other a male rotor. These two rotating
components turn counter
to
one another (counterrotating). The two rotating elements
are designed
so
that as they rotate opposite to one another; their respective helix
forms intermesh (see Figure
3-78).
As
with all rotary compressors, there are no valves.
The gas is sucked into the inlet post and is squeezed between the male and female