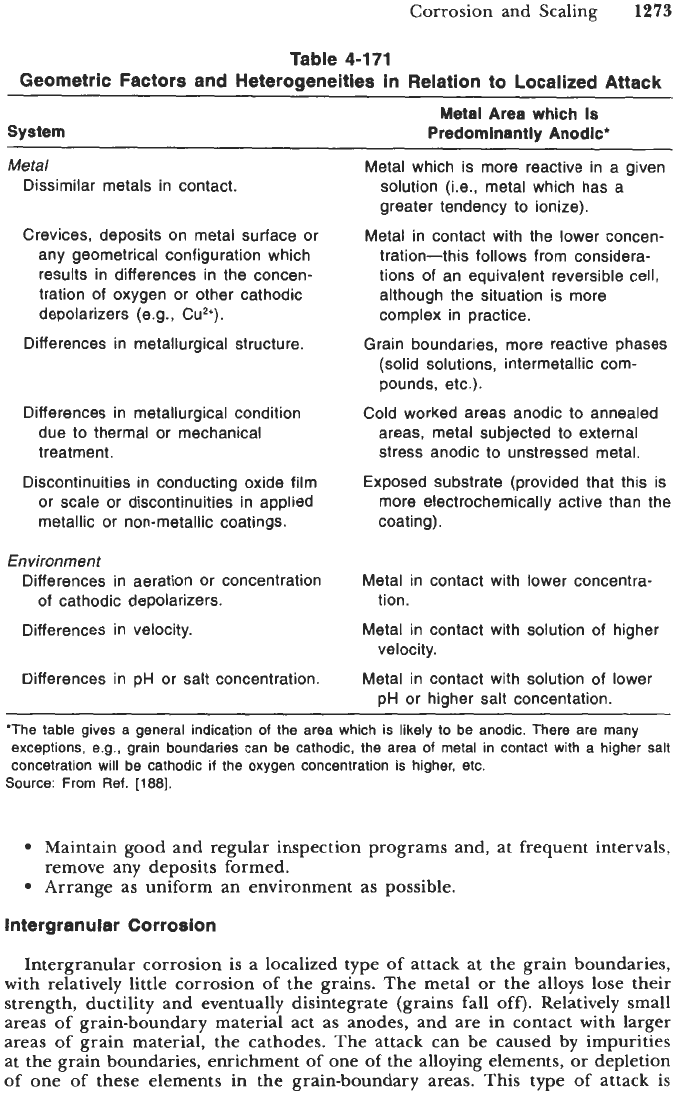
Corrosion and Scaling
1273
Table
4-171
Geometric Factors and Heterogeneities in Relation to Localized Attack
Metal Area
which
Is
System Predominantly Anodic'
Metal
Dissimilar metals in contact.
Crevices, deposits on metal surface or
any geometrical configuration which
results in differences in the concen-
tration
of
oxygen or other cathodic
depolarizers (e.g., Cu2+).
Differences in metallurgical structure.
Differences in metallurgical condition
due to thermal or mechanical
treatment.
Discontinuities in conducting oxide film
or scale or discontinuities in applied
metallic or non-metallic coatings.
Environment
Differences in aeration or concentration
Differences in velocity.
of cathodic depolarizers.
Differences in pH or salt concentration.
Metal which is more reactive in a given
solution (Le., metal which has a
greater tendency to ionize).
Metal in contact with the lower concen-
tration-this follows from considera-
tions of an equivalent reversible cell,
although the situation is more
complex in practice.
(solid solutions, intermetallic com-
pounds, etc.).
Cold worked areas anodic to annealed
areas, metal subjected to external
stress anodic to unstressed metal.
Exposed substrate (provided that this is
more electrochemically active than the
coating).
Grain boundaries, more reactive phases
Metal in contact with
Metal in contact with
Metal in contact with
tion.
velocity.
lower concentra-
solution of higher
solution of lower
pH or higher salt concentation
"The table gives a general indication of the area which is likely
to
be anodic. There are many
exceptions, e.g., grain boundaries can
be
cathodic, the area of metal in contact with
a
higher
salt
concetration will be cathodic
if
the oxygen concentration is higher, etc.
Source: From Ref.
[188].
Maintain good and regular inspection programs and, at frequent intervals,
remove any deposits formed.
Arrange as uniform an environment as possible.
intergranular Corrosion
Intergranular corrosion is a localized type of attack at the grain boundaries,
with relatively little corrosion of the grains. The metal
or
the alloys lose their
strength, ductility and eventually disintegrate (grains fall off). Relatively small
areas of grain-boundary material act as anodes, and are in contact with larger
areas of grain material, the cathodes. The attack can be caused by impurities
at the grain boundaries, enrichment of one of the alloying elements,
or
depletion
of one of these elements in the grain-boundary areas. This type of attack is