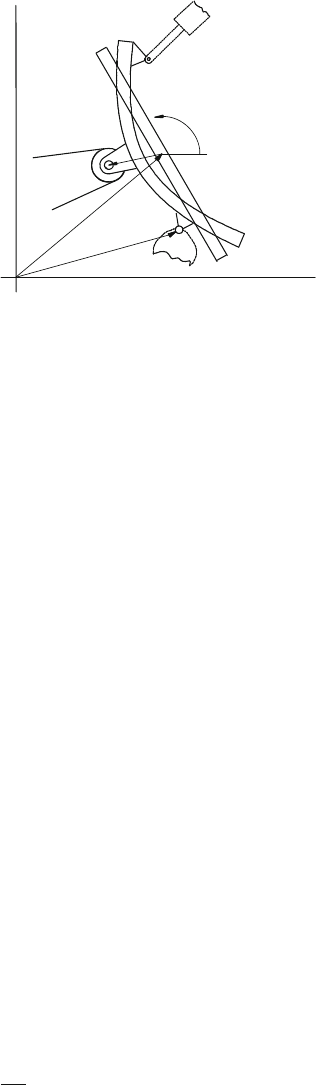
308 E. Keskinen et al.
Fig. 25.11 Link element
connected to hydraulic
actuator, neighboring link,
and wire wheel
S
R
r
j
θ
where the first two elements (S, ) of vector y D
S uv
T
are the rigid body
coordinates of link center of gravity. The remaining components are modal coordi-
nates of the vibratory motion in axial and bending directions.
The position of nodal points fixed to the moving link can be calculated using
kinematic transformation R D R.r; y/ D ŒXY
T
, where the link state variables y
and local link positions r are related to the global Cartesian variables. This makes it
possible to follow also the global positions of wheel centers with link motion. When
the wheels are moving with boom link, their velocity is given for wheel i by
v
i
D J .r
i
/ Py (25.29)
where J D @R=@y is the Jacobian between the Cartesian and state vector spaces
evaluated at the wire wheel node. The right-hand-side terms in (25.28), respectively,
represent gravitational loading, concentrated forces from motion constraints, actua-
tors loading, see (25.37), and the last term is the wire wheel force
L D J.r
i
/
T
F
i
: (25.30)
The wire reaction F
i
can be computed from (25.27) completing the equation system
in wire–boom interaction.
25.4 Fluid Power Circuit
The power source in lifting booms is very often oil hydraulics. Hydraulic volume
element consists of subvolumes in actuator chamber (a), hose (h), and pipe (p). If
lumped parameter approach is used, the dynamic equations for pressure variations
in plus (i DC) and minus (i D) volumes of actuator circuit are
Pp
i
D B
Q
i
V
i
; (25.31)