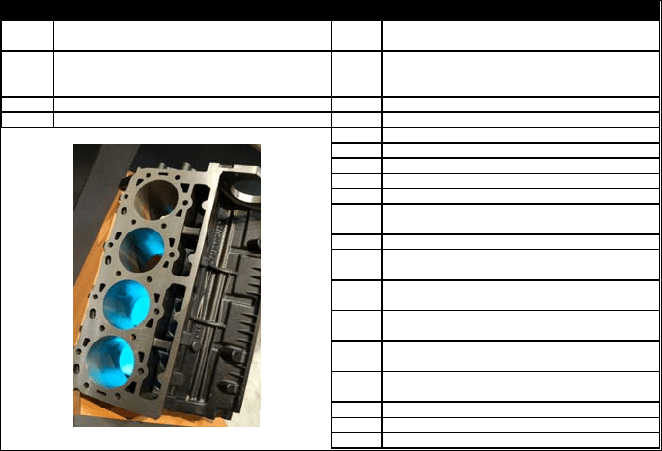
424 Ciro A. Rodríguez and Horacio Ahuett
ity. This need for flexibility comes from both a) the market demand shifts typical
of the automotive sector and b) manufacturing operation changes associated with
new product models. Clearly, the architecture of the machining system is designed
to suit the production demands and ranges from transfer lines to individual ma-
chines in job shop arrangements. The choice of architecture in turn determines the
structure of the machines that constitute the system.
13.2.1 Dedicated Machines
Dedicated machines are divided into linear transfer machines and rotary transfer
machines. The following sections explain and illustrate both types of dedicated
machines.
13.2.1.1 Linear Transfer Machines
The linear transfer machine or transfer line is an automated and interlocked group of
stations that includes machining, deburring, cleaning and inspection operations. The
whole transfer line must be designed and built as a unit. The various stations in the
transfer machine perform manufacturing operations on the product simultaneously.
By interlocking the machine stations and the material handing system, it is possible to
OP 10C
Pre-machine oil pan face and crakcase features,
finish-millin
manufacturin
lu
s
OP 10
Mill bank faces, mill oil pan face and crankcase
features, drill manufacturin
holes
OP 20C
Pre-machine bank & end faces, core drill cup plug
holes, drill oil gallery holes, de-flash cylinder bores
OP 20 Rough and finish-bore parent metal cylinder bores
OP 30C Washe
OP 30 Preliminary washe
OP 40C Leak test OP 40 Cylinder block heate
OP 50 Cylinder liner assembl
OP 60 Coolin
& stora
e s
stem
OP 70 Finish-mill, drill and tap bearin
cap seats
OP 80 Intermediate washe
OP 90 Bearing cap assembl
OP 100
Semi-finish mill, drill and tap oil pan face, finish
bore manufacturing holes
OP 110 Semi-finish mill, drill and tap end faces
OP 120
Drill and tap deck faces, drill and ream oil feed
and dip stick holes
OP 130
Finish-bore cup plug holes, mill, drill & tap
mounting
OP 140
Rough, semi-finish and finish-bore crank bore,
finish-bore water pump and dowel holes
OP 150
Rough, semi-finish and finish-bore cylinder bores
and finish-mill bank face
OP 160
Finish-mill front, rear & pan faces. Finish-bore
bank face dowels.
OP 170 Hone
OP 180 Final washe
OP 190 Cup plu
assembl
and leak test
Operations Order In Foundry Operations Order in Engine Plant
OP 10C
Pre-machine oil pan face and crakcase features,
finish-millin
manufacturin
lu
s
OP 10
Mill bank faces, mill oil pan face and crankcase
features, drill manufacturin
holes
OP 20C
Pre-machine bank & end faces, core drill cup plug
holes, drill oil gallery holes, de-flash cylinder bores
OP 20 Rough and finish-bore parent metal cylinder bores
OP 30C Washe
OP 30 Preliminary washe
OP 40C Leak test OP 40 Cylinder block heate
OP 50 Cylinder liner assembl
OP 60 Coolin
& stora
e s
stem
OP 70 Finish-mill, drill and tap bearin
cap seats
OP 80 Intermediate washe
OP 90 Bearing cap assembl
OP 100
Semi-finish mill, drill and tap oil pan face, finish
bore manufacturing holes
OP 110 Semi-finish mill, drill and tap end faces
OP 120
Drill and tap deck faces, drill and ream oil feed
and dip stick holes
OP 130
Finish-bore cup plug holes, mill, drill & tap
mounting
OP 140
Rough, semi-finish and finish-bore crank bore,
finish-bore water pump and dowel holes
OP 150
Rough, semi-finish and finish-bore cylinder bores
and finish-mill bank face
OP 160
Finish-mill front, rear & pan faces. Finish-bore
bank face dowels.
OP 170 Hone
OP 180 Final washe
OP 190 Cup plu
assembl
and leak test
Operations Order In Foundry Operations Order in Engine Plant
Fig. 13.3 Operations sequence for engine block machining in transfer line [1]