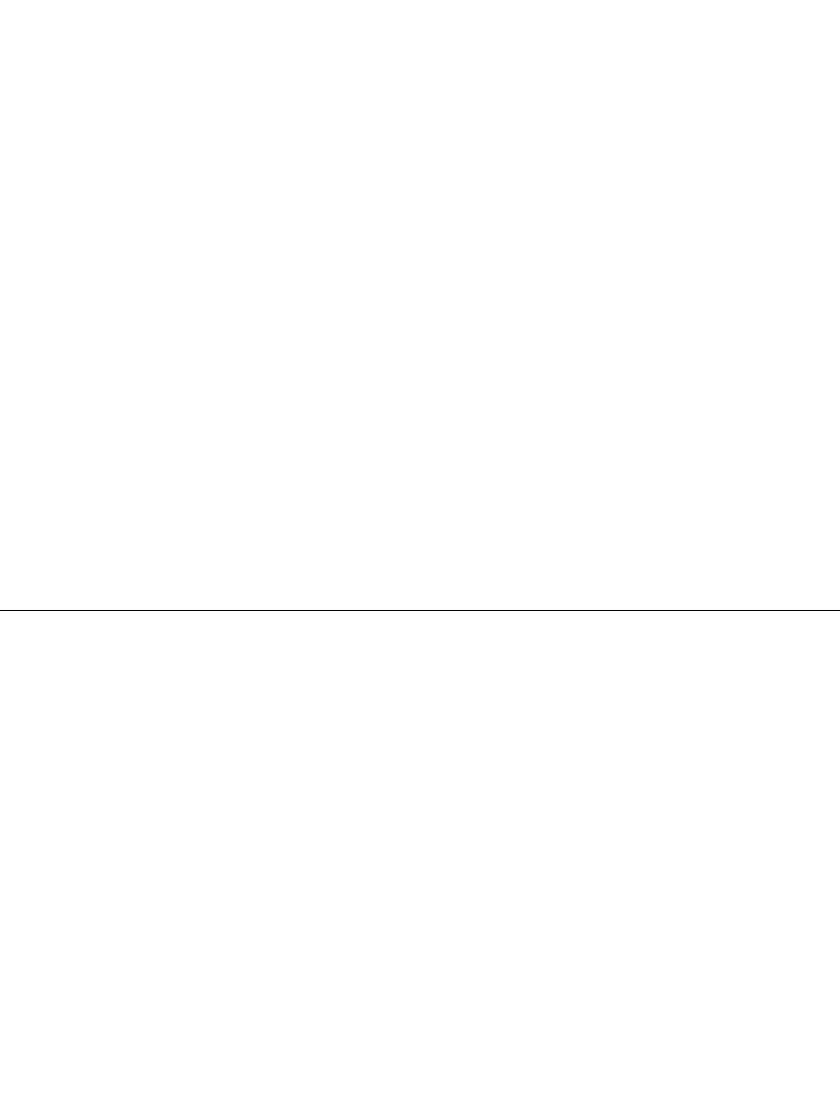
12.10 CHAPTER TWELVE
Because of the slight solubility of silver oxides in alkaline electrolyte, little work was done
with zinc /silver oxide cells until 1941 when Andre´
22
suggested the use of a cellophane
barrier. Cellophane prevents migrating silver ions from reaching the anode
23,24
by reducing
them to insoluble silver metal. The cellophane is oxidized and destroyed in the process,
making it less effective for long-life cells.
Many types of laminated membranes are presently available. A commonly used alternate
barrier material is prepared from a radiation graft of methacrylic acid onto a polyethylene
membrane.
23,24
The graft makes the film wettable and permeable to the electrolyte. Studies
have shown that lower resistance polyethylene barrier membrane is suitable for high-rate
KOH cells while higher resistance polyethylene is suitable for low-rate NaOH cells. Cello-
phane is used in conjunction with the grafted membrane as a sacrificial barrier. The lami-
nation of cellophane to either side of the polyethylene membrane results in a synergistic
action for stopping silver migration.
15
A separator is commonly used in conjunction with a barrier membrane layer as added
protection to the barrier. It is located between the barrier and anode cavity and is multi-
functional both during cell manufacture and in performance. Separators in zinc/silver cells
are typically fibrous woven or non-woven polymers such as polyvinyl alcohol (PVA). The
fibrous nature of the separator gives it stability and strength that protects the more fragile
barrier layers from compression failure during cell closure or penetration of zinc particles
through the membranes themselves. The separator also acts in controlling dimensional stress
in the barrier layers which is often derived during original rollup of cellophane or in lami-
nation with polyethylene membranes. As barrier membranes wet out, this stress is relieved.
Differential swelling may then occur which could result in a gap that would allow silver ion
migration to the anode. The separator acts to prevent the formation of these gaps.
12.3 CONSTRUCTION
Figure 12.8 is a cross-sectional view of a typical zinc/ silver oxide button type battery.
Zinc/ silver oxide button cells are designed as anode limited; the cell has 5 to 10% more
cathode capacity than anode capacity. If the cell were cathode limited, a zinc-nickel or zinc-
iron couple could form between the anode and the cathode can resulting in the generation
of hydrogen.
The cathode material for zinc /silver oxide cells is monovalent silver oxide (Ag
2
O) mixed
with 1 to 5% graphite to improve the electrical conductivity. The Ag
2
O cathode material
may also contain manganese dioxide (MnO
2
) or silver nickel oxyhydroxide (AgNiO
2
)as
cathode extenders. The cathode could also be prepared from a controlled blend of divalent
silver oxide and monovalent silver oxide with either silver plumbate (Ag
5
Pb
2
O
6
) or silver
metal to reduce the AgO cathode voltage and cell impedance, but this is no longer a com-
mercial process. A small amount of polytetrafluoroethylene (Teflon
TM
) may be added to the
mix as a binder and to ease pelleting.
The anode is a high surface area, amalgamated, gelled zinc metal powder housed in a
top cup which serves as the external negative terminal for the cell. The top cup is pressed
from a triclad metal sheet: the outer surface is a protective layer of nickel over a core of
steel. The inner surface that is in direct contact with the zinc is high-purity copper or tin.
The cathode pellet is consolidated into the positive can, which is formed from nickel-plated
steel and serves as the positive terminal for the cell. To keep the anode and cathode separated,
a barrier disk of cellophane or a grafted plastic membrane is placed over the consolidated
cathode. The entire system is wetted with potassium or sodium hydroxide electrolyte.
The gasket serves to seal the cell against electrolyte loss and to insulate the top and
bottom cups from contact. The gasket material is made from an elastic, electrolyte-resistant
plastic such as nylon. The seal may be improved by coating the gasket with a sealant such
as polyamide or bitumen to prevent electrolyte leakage at the seal surfaces.