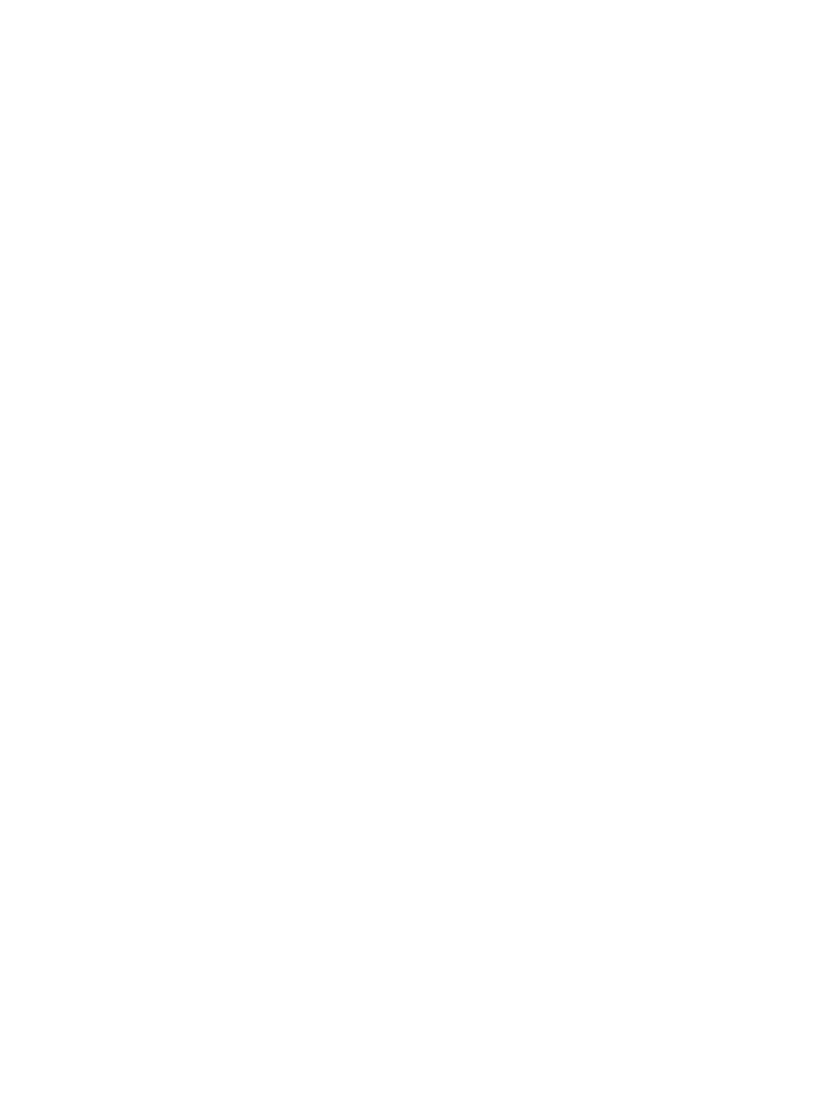
40.16 CHAPTER FORTY
1.76 V. This higher open-circuit cutoff voltage significantly decreased the corrosivity of the
sodium polysulfide active material, permitting the use of lower-cost container coatings.
12
During this same time period, SPL adopted a major change in cell design philosophy to
address problems with freeze-thaw durability and battery reliability (networking considera-
tions). A relatively small, nominally 10-Ah cell resulted that was designated the PB.
40.3.3 Sodium/Nickel-Chloride Cell Technology
A schematic diagram of a sodium /nickel-chloride cell was shown previously in Fig. 40.1b
and a photograph of a modern cell in Fig. 40.6b. In this standard configuration, the sodium
is located on the outside of the

ⴖ-Al
2
O
3
electrolyte (outside sodium). An inside sodium
configuration would require the use of an expensive nickel container. Another advantage of
the outside-sodium cell configuration is that an external cell case with a square cross-section
can be used. This cell geometry permits maximum volumetric packing efficiency within the
battery enclosure to be attained. A third advantage of this configuration is the cell behavior
during thermal ‘‘freeze/ thaw’’ cycling. Here, detrimental tensile stresses on the electrolyte
do not develop, thus effectively eliminating this potential failure mode. The positive electrode
itself is then contained within the electrolyte. In a fully charged cell, this electrode is a
porous nickel matrix that is partially chlorinated to nickel dichloride. The remaining nickel
backbone serves as part of the positive-electrode current collector. About 30% of the nickel
is used in the cell reactions. The matrix is impregnated with the NaAlC1
4
molten salt. The
sodium compartment is less complex than that of the sodium/sulfur cell because safety
features are not needed. The approach to primary containment for both the outer container
and the electrode seals is similar to that with sodium/ sulfur. As discharge proceeds, the
reactions in the positive electrode occur from the outside of the solid nickel structure and
proceed inqard thorugh an ever-increasing thickness of reduced nickel. This shrinking-core
process resuls in an increasing electrical resistance as the cell discharges because the effective
area of the reacting nickel chloride is constantly being reduced. The chemistry of the dis-
charge process provides another significant advantage relative to sodium/ sulfur: cells can be
safely assembled with the discharge products (nickel metal and salt), and then charged.
Also in contrast to the sodium/ sulfur technology, the development of the sodium/metal
chloride system has been pursued by a successive progression of single, integrated organi-
zations for one primary application—electric vehicles. Currently, the prime developer is the
Swiss company, MES-DEA SA. They purchased the technology from AEG Anglo Battery
Holdings (AABH), an organization formed by the German company AEG in cooperation
with the original developers (Zebra Power Systems and Beta R&D Ltd.). This technology is
often referred to as ZEBRA because of its origins. The acronym ZEBRA stands for Zero
Emission Battery Research Activities. To date, development has focused almost exclusively
on the higher voltage nickel variant but using iron as a doping addition to the positive
electrode. As such, the pure iron-based system will not be discussed further in this chapter.
The cell designs that have been developed to date have capacities ranging from 20 to 200
Ah. Specifications for the actual cell design that incorporates the advancements made during
the past five years are listed in Table 40.5. These advancements resulted in an improved
pulse-power capability (especially near the end of discharge) and energy content.
4
At 80%
depth-of-discharge, the power of a modern cell (ML3) is 2.5 times that of a 1992 vintage
cell (SL09). This enhanced level of power performance can be determined by comparing the
cell data previously presented in Fig. 40.3 with modern performance data shown in Fig.
40.12 for a full-sized battery. The most important modifications involved: (1) the use of a
fluted or cruciform-shaped electrolyte that minimized the thickness of the positive electrode
and increased the area of the

ⴖ-Al
2
O
3
electrode; and (2) the introduction of iron as a dopant
to the nickel positive electrode. Optimization of the design and improvements in the chem-
istry of the positive electrode also resulted in a 20 to 40% increase in energy content. The
demonstrated reliability of the early 1990s ZEBRA cells was outstanding with cell failures
virtually non-existent.