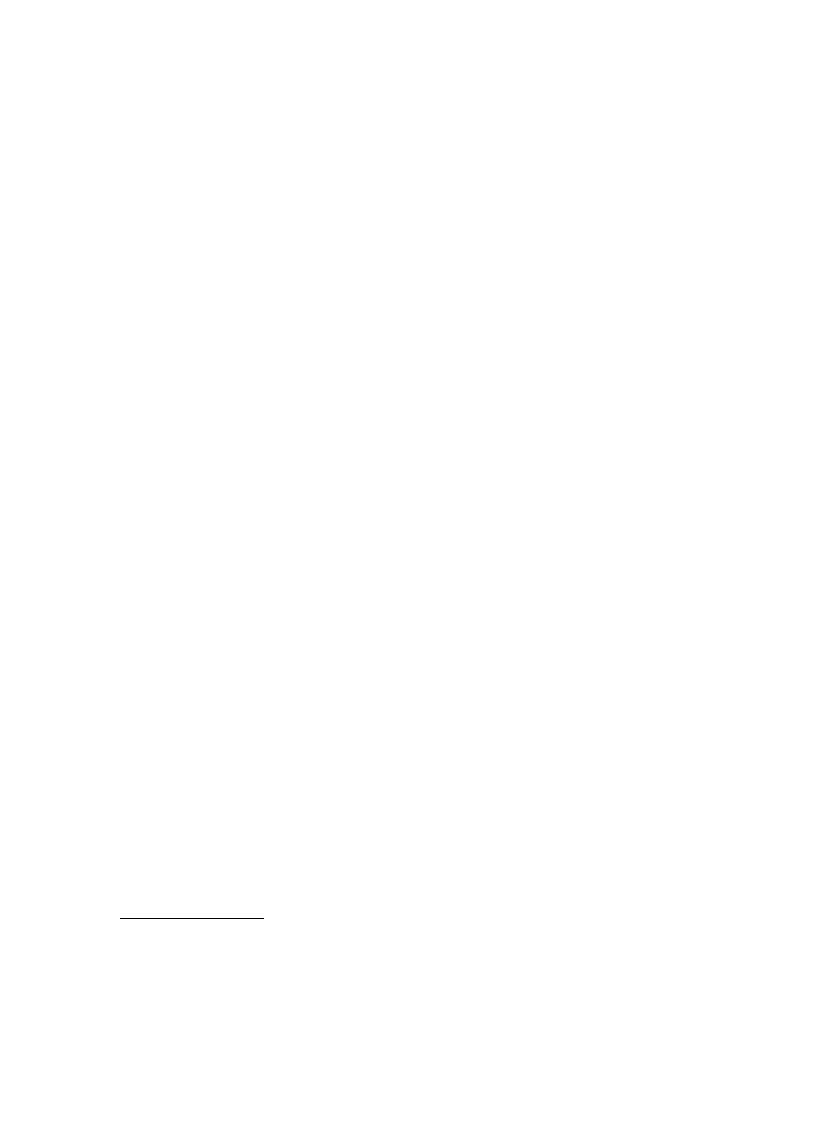
LITHIUM / IRON SULFIDE BATTERIES 41.11
Active additives CoS
2
and chalcopyrite (CuFeS
2
) reduced the cell area-specific-impedance
(ASI) significantly while providing nearly the same capacity as the FeS
2
removed in its
place. Chalcopyrite is favored over CoS
2
based on its abundance in nature and, hence, low
cost. ASI as a function of depth of discharge (DOD) is presented in Figs 41.9 to 41.11 for
cells with positive electrodes that consist of FeS
2
only, 12% CoS
2
additive, and 18% CuFeS
2
additive, respectively. Concern existed over the deposition of Cu in the separator from the
chalcopyrite. To test the impact of this, a 3-cm diameter bipolar cell with 25 mol % CuFeS
2
in the positive electrode was cycled for over 1000 cycles at a C/1 charge and discharge
current rate. The coulombic efficiency remained greater than 99% throughout the life of the
cell. A post-test analysis showed small particles of metallic Cu in the separator, but were
too dispersed to create a short circuit.
8
An optimum concentration of CoS
2
additive in the FeS
2
positive electrode was determined
to be approximately 12 mol %. The optimum concentration of CuFeS
2
additive was found
to be around 12 to 18 mol %. The effect of CoS
2
on the ASI is shown in Figure 41.12 over
the range of 0 to 100% with a salt concentration of 33-wt. % in the cold pressed positive
pellet. Two other data points with different salt concentrations were added to this Figure,
one at 28-wt. % salt in 12:88 molar ratio of CoS
2
: FeS2, and the other at 43-wt. % salt in
100-mol % CoS
2
. The more than doubling of the ASI at 12-mol % CoS
2
additive resulting
from the reduction of the salt concentration by only 5% overwhelms the relatively small
improvement from the CoS
2
additive. Similar comments can be made for the 43-wt. % data
point at 100-mol % CoS
2
.
The addition of CoS
2
required an increase in the concentration of salt in the cold pressed
pellet to prevent the electrode from being too electrolyte starved. This was due to the much
finer particle size and morphology of the synthetic CoS
2
relative to the ground-up naturally
occurring pyrite. These points stress the importance of establishing an optimum salt concen-
tration when operating near starved-electrolyte conditions. Too much electrolyte and the
electrode becomes too fluid (difficult to contain) and the energy density is reduced needlessly.
Not enough electrolyte in the positive electrode results in excessive ASI and poor utilization
of the active materials. Salt concentrations between 28 to 32-wt. % in the positive electrode
were found to be the most practical.
Improvements were made to the LiCl-rich LiCl:LiBr:KBr electrolyte by addition of small
amounts of LiI. The addition of LiF also provided an increase in rate capability of the
electrolyte, but not as much as the LiI.
5
The combination of increasing the electrolyte con-
centration from 28 to 32-wt.% and replacing the CoS
2
with CuFeS
2
had a marked improve-
ment in power capability for this cell technology, as can be seen from an inspection of Fig.
41.13, which is a plot of the specific energy that results from constant power level discharges.
LiI was added to each of these full-size 13-cm bipolar cells. The specific energy and power
levels shown in this figure are based on the total chemistry weight only; no hardware was
added to the weight basis. It was estimated that the hardware would constitute approximately
30-wt. % of the total battery weight. Thus, 160 Wh/kg on a chemistry weight basis would
correspond to approximately 112 Wh/kg on the total battery weight basis.*
*‘‘Total Chemistry Weight’’ is defined as the total weight of all chemicals in the cell
components (negative, separator, and positive), which includes active and inactive materials.
For this system, it is the sum of the LiAl, MgO, Al
5
Fe
2
, LiCl, LiBr, KBr, LiF, Lil, FeS
2
,
CoS
2
, and CuFeS
2
throughout the whole cell. The weight of any hardware or the weight of
the thermal management system are not included mostly because these were not fully de-
veloped but were expected to be approximately 30 percent of the total battery weight. Hence,
160 Wh /kg on a chemistry weight basis would correspond to approximately 112 Wh /kg on
a total battery weight basis as noted in Section 41.4.9. This 30 percent estimate is based on
a large multicell battery, such as in an all electric vehicle. The hardware and thermal man-
agement weight would be a much higher percentage of the battery weight for a battery with
only a few cells.