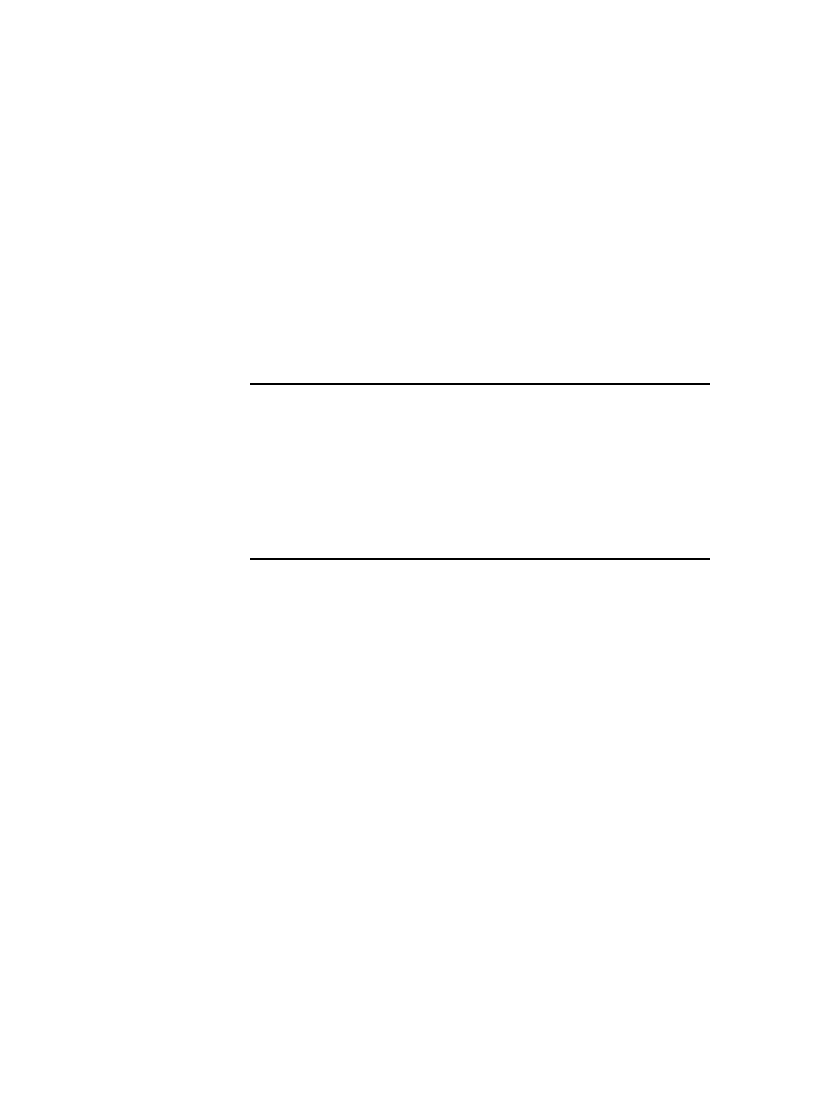
39.14 CHAPTER THIRTY-NINE
In the United States, a team at the University of California, Davis, installed a Powercell
30 kWh Zinc-Flow
battery in a Geo Prizm with a Dolphin drive system for the Endura
project.
31
The battery consisted of two stack towers, each containing two 54 cell bipolar
stacks connected in series, two electrolyte tanks and associated pumping systems, and control
and cooling systems. Selected battery specifications are given in Table 39.5. At 391 V, this
is the highest voltage zinc /bromine battery used in an electric vehicle, and the team claims
the Endura is one of the few electric vehicles that is capable of travelling in the high speed
lane of the Los Angeles freeway system. The Endura travelled 175 miles on a single charge,
and the vehicle was capable of accelerating from zero to 100 kilometers (62 miles) per hour
in 15 seconds, and of reaching a velocity of 125 kilometers (78 miles) per hour.
32
The gross
vehicle weight was 1595 kg with a front to rear weight distribution of approximately
50/ 50.
TABLE 39.5 Selected Specifications for the Powercell Endura
Electric Vehicle Battery
Open circuit voltage @ 100% SOC 391 V
Maximum power @ 50% SOC
⬃40 kW
Charge method Constant current
Nominal charge rate 30 amps DC
End of charge voltage 432 V
Nominal charge power 12 kW
Nominal charge time 5 hours (0 to 100% SOC)
Battery specific energy @ C/ 3 rate 65.8 Wh /kg
Source: From Swan, et al.
31
After an extensive safety review,
33
the Endura was entered into several competitions with
successful results. The team placed third in the 1994 Arizona Public Service Electric 500,
first in the 1994 World Clean Air Rally, second in the 1994 American Tour de Sol, and first
in the 1995 Arizona Public Service Electric 500.
31,33
Powercell GmbH asserts that the zinc /bromine technology will be one of the most af-
fordable for electric vehicles.
32
In direct comparison using the same test vehicle fitted with
lead-acid batteries versus Zinc-Flow
batteries, Powercell has been able to show that the
test vehicle will havea2to3fold greater range when fitted with a Zinc-Flow
battery due
to this technology’s reduced weight and higher energy density.
Toyota Motor Corporation has also been developing zinc /bromine batteries for electric
vehicles.
35,39
A concept urban transportation vehicle, called the EV-30, has been designed
for use with Toyota’s zinc/ bromine battery and has been displayed at motor shows in Japan.
This two-seater vehicle would transport people in buildings, shopping centers, small com-
munities, and to and from train stations—a ‘‘horizontal elevator’’ concept. The front-wheel-
drive system uses an AC induction motor built by Toyota Motor Corporation. The battery
system is modular zinc/bromine at 106 V and 7 kWh.
39.7.2 Energy Storage Applications
The use of zinc/ bromine batteries in energy storage applications is also being demonstrated.
A study by Sandia National Laboratories rated the zinc/bromine battery as excellent for
these four utility applications: storage of energy generated by renewable sources, transmis-
sion facility deferral, distribution facility referral, and demand peak reduction.
36