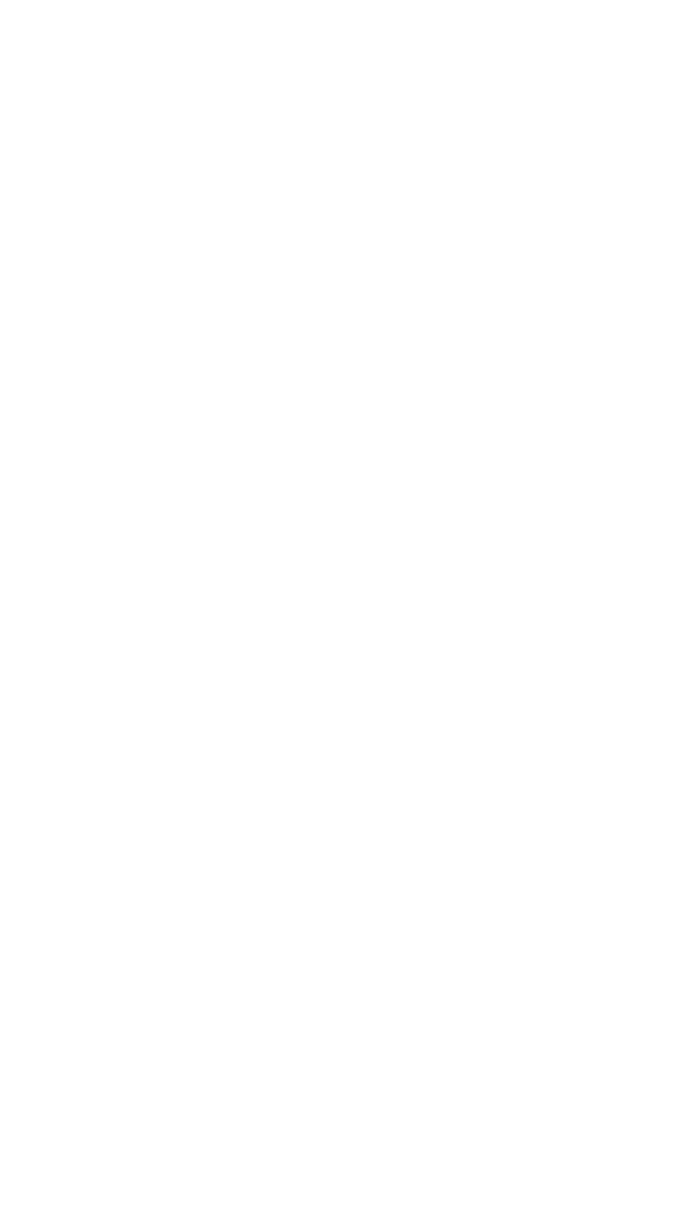
288 CORROSION AND OXIDATION OF MAGNESIUM ALLOYS
HAE process, however, a chromate sealant is necessary to obtain acceptable
corrosion resistance.
Tagnite
85
and Magoxid-Coat
86
are anodic spark processes carried out at higher
voltages (final voltage up to about 400 V AC). These anodic coatings are more
protective and not based on chromates. The Tagnite process uses a hydroxide–
silicate–fluorid electrolyte and the thickness of the coating can be varied be-
tween 2 and 30
m depending on current density and time. Magoxid-Coat is
formed in a slightly alkaline electrolyte and results in a partially amorphous
oxidic layer based on Mg, Al, and P. The coating consists of a thin barrier layer,
a virtually nonporous intermediate ceramic layer responsible for the good cor-
rosion resistance and a very porous outermost ceramic layer. The coating builds
up to an optimal thickness of 15–25
m. Probably, the amorphous nature of the
coating contributes toward its improved corrosion behavior. Codeposition of
transition metal oxides and organic materials is used to produce additional char-
acteristics, e.g., colored coatings.
Painting of Mg parts may be used to apply a decorative finish or as a mean
of protection against corrosion and tarnish. Organic coating can vary from simple
oils or waxes to multipaint coatings. If the environment is severe, primers should
be based in alkali-resistant vehicles as, e.g., vinyl, epoxy, polyvinyl butyral,
acrylic resins, or baked phenolic resins, and contain inhibitive pigments with a
slightly soluble chromate.
Following the recent developments of surface engineering, a variety of new
surface modification technologies, including ion implantation, chemical vapor
deposition/physical vapor deposition (CVD/PVD), and laser surface alloying/
melting, can be used to develop more effective and environmental friendly coat-
ings.
87
Hydride coatings were recently proposed as an alternative to chromate
coatings.
88
A magnesium hydride or hydrogen-rich layer with thickness of 1–2
m is created on the Mg surface by cathodic electric charging in aqueous so-
lution. The hydride coating promotes pseudo-passivation of Mg. It can be used
either as a stand-alone protective coating or as an effective paint base. Implan-
tation of N
2
⫹
ions on AZ91D surfaces enhances corrosion resistance; an optimal
dose of 5
⫻ 10
16
ions/cm
2
results in a corrosion rate approximately 15% of that
for the unimplanted alloy.
89
4 OUTLOOK
Whereas oxidation resistance of Mg alloys is generally considered to be suffi-
cient, at least in the temperature range of typical application, corrosion can still
be a problem. Further trends to improve corrosion properties of Mg alloys in-
clude: (1) Control of heavy metal content, (2) alloying with elements that sta-
bilize the surface oxide, e.g., RE, and with Mn that improves corrosion behavior
due to iron control effect, (3) use of RS techniques, and (4) coating and painting.
Heavy metal impurity control is the key action in the design of highly cor-
rosion resistant Mg alloys. These impurities enhance corrosion by orders of
magnitude and only their accurate control gives the indispensable basis for a
successful application of all other corrosion protection measures.
In marked contrast to Al and its alloys, Mg does not form a dense protective
oxide. The films naturally formed on Mg, although stable in dry environments,
are rapidly undermined in the presence of water and contaminants. The useful-
ness of Mg alloys can be successfully increased by improving the oxide layer