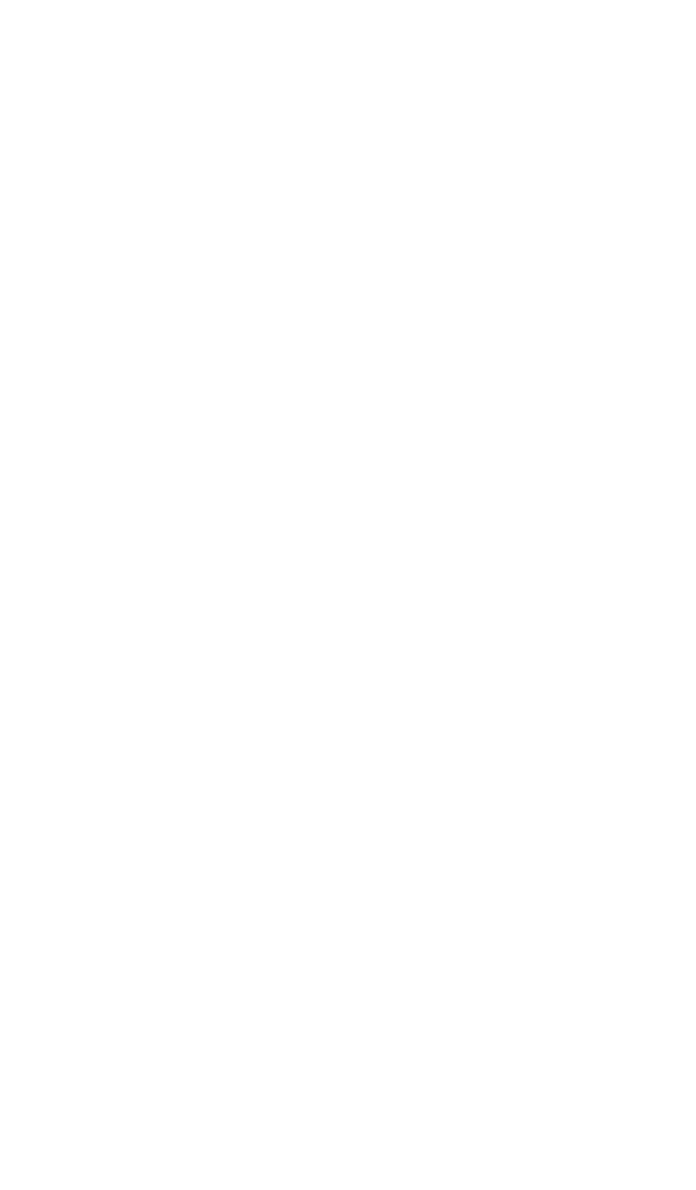
276 CORROSION AND OXIDATION OF MAGNESIUM ALLOYS
Usually, corrosion concentrates at regions adjacent to second-phase particles and
boundaries. Some grains or particles might be undermined and fall out, resulting
in higher mass losses than solely due to electrochemical dissolution; this partly
explains the so-called negative difference effect observed during anodic polari-
zation of Mg.
27
As a naturally passive metal, Mg may suffer pitting corrosion. AZ91 in
chloride-containing environments exhibits a variety of localized forms of cor-
rosion, including pitting at the outset (initiation sites are few and associated with
intermetallic particles), filiform corrosion at early stages of propagation, and a
cellular type of attack in the terminal stage.
33–35
The occurrence of filiform cor-
rosion on uncoated surfaces of AZ91, which is not the case for unalloyed, bare
Mg,
36
suggests the presence of a more resistant air-formed oxide on the alloy.
Pure Mg is resistant to stress–corrosion cracking (SCC). However, alloying
with Al and Zn promotes SCC, which increases with increasing Al content.
1
Thus, Mg–Al–Zn alloys have the greatest susceptibility to SCC. Alloys con-
taining Zr are essentially free from the phenomenon. SCC in Mg alloys
15,37,38
is
usually transgranular occurring along twin boundaries or various crystallographic
planes. There is general agreement that hydrogen embrittlement is the dominant
mechanism. Since hydrogen cannot penetrate the passive film unless it is already
damaged, pitting is likely to be the first step on SCC. Therefore, solutions that
are nonactive to Mg (such as diluted alkalies, concentrated HF, and chromic
acid) or in which general corrosion predominates do not induce SCC. High-
humidity content, dissolved oxygen, and seawater accelerate SCC; heavy metal
content does not seem to influence it. SCC was studied mainly in Mg–Al systems
and information is still lacking for other Mg alloys, in particular for new emerg-
ing alloys, e.g., glassy alloys or those containing RE.
3.3 Environment and Surface Film
Owing to the very active electrochemical character of Mg, the corrosion behavior
of its alloys reflects the protective qualities of the surface film in various envi-
ronments. As discussed in Section 2.1, in natural environments with low hu-
midity a stable MgO film [or a mixture of MgO and Mg(OH)
2
] forms on
magnesium and protection is essentially perfect. Atmospheric corrosion is a
threat only in the presence of humidity that leads to condensed water. The cor-
rosion rate of magnesium during exposure to humid air is less than 10
⫺
5
mm/
yr in the absence of condensation, while it becomes greater than 1.5
⫻ 10
⫺
2
mm/yr when water condenses on the surface.
39
Hence, for indoor service Mg
alloys serve well without any further protection.
Although stable and dense, the air-formed film is permeable to water and
soluble Mg species. Exposure to humid air rapidly causes hydration of the oxide
and formation of thicker films (e.g., 100–150 nm after 4 days) with a duplex
structure.
11,12
The outer layer of the film (20–40 nm) is amorphous and similar
to the film formed in dry air (see Fig. 2), but an additional hydrated layer is
formed adjacent to the metal. The hydrated layer reduces the passivity of the
metal surface by allowing Mg dissolution. This layer is quite sensitive to electron
irradiation and develops a cellular structure in the microscope; continued ex-
posure to the electron beam causes release of water and formation of nanocrys-
talline fcc MgO. Immersion in water leads to the formation at the outermost