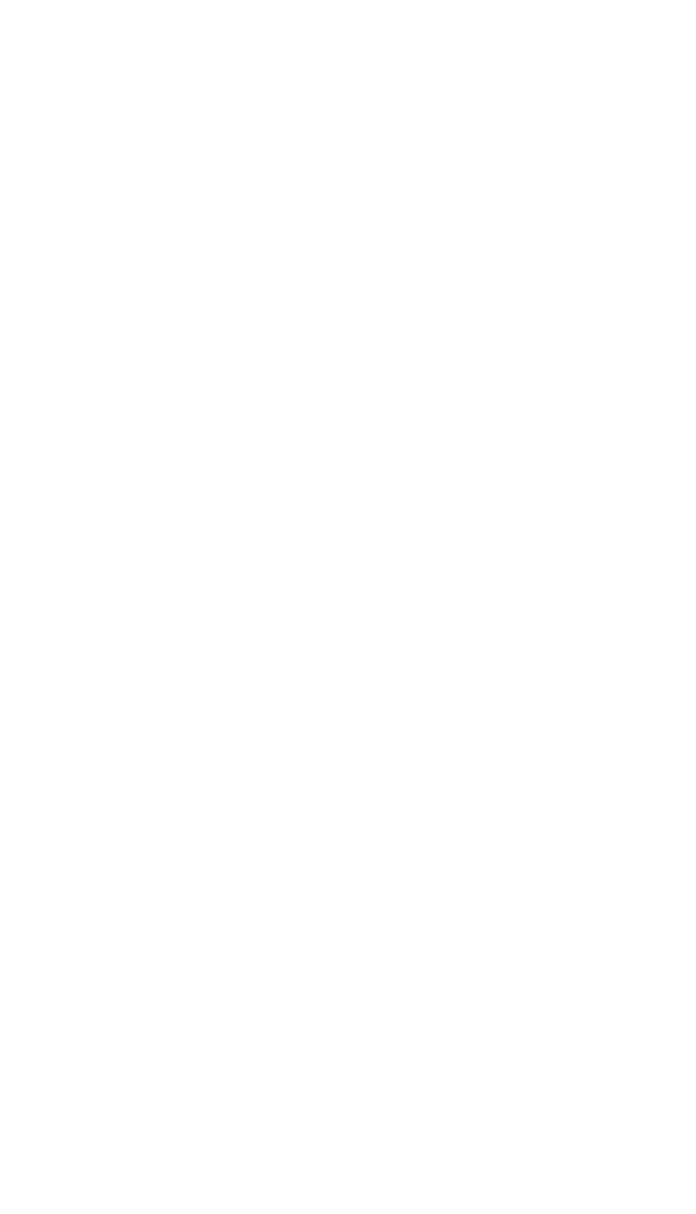
318 SELECTION OF SUPERALLOYS FOR DESIGN
superalloy is used in the same product form, process treatments may be used to
optimize one property over others. For example, an alloy such as Waspaloy was
made in wrought form for gas turbine disks. By adjustment of processing con-
ditions, principally heat treatment, substantial yield strength improvements were
achieved at the expense of creep-rupture strength.
4 EVOLUTION OF SUPERALLOYS
During the first quarter of the twentieth century, chromium was added at various
times to cobalt, nickel, and iron. The resulting products were remarkably resis-
tant to atmospheric (moisture-based) environments and to oxidation at high tem-
peratures. By World War II, some of these alloys, including other alloy elements,
had come into use for such applications as resistance wires, dental prostheses,
cutlery, and furnace and steam turbine components. With the development of
the gas turbine engine during the war, the need became apparent for corrosion-
resistant materials to operate in demanding mechanical load conditions at high
temperatures. At this point, the fledgling superalloy industry began to expand.
By modifying the stainless steels, higher strengths were achieved without the
need for special high-temperature strengthening phases. Phases such as
(a
nickel–titanium compound) or
␥
⬘ (a nickel–aluminum compound) had been in-
troduced into the nickel –chromium families of alloys just prior to the war to
produce high strength at high temperatures. The increasing temperatures forced
alloy developers to include these phases (
and
␥
⬘) in the iron-base alloys to
take the high-temperature strength characteristics beyond those of the modified
stainless steels such as 19-9DL. Alloys were invented in Germany and, after
modification, made their way to the United States as A-286 or V-57 and are still
in use today.
Nevertheless, the need for creep-rupture strength continually increased. Some
of this need was met in the early years by adapting a cobalt-base corrosion-
resistant alloy (vitallium) for use in aircraft engine superchargers and, later, to
airfoils in the hot sections of gas turbines. Similar cobalt-base superalloys are
still in use today. However, creep-rupture requirements for aircraft gas turbine
applications soon outstripped those of the iron-nickel-base superalloys and the
cobalt-base superalloys, and so nickel-base superalloys, modified to provide
more of the hardening phase
␥
⬘, became increasingly used.
4.1 Improvement of Superalloys by Chemistry Control
The production of superalloy components initially consists of some sort of melt-
ing process. The melting produces ingots that are either remelted, converted to
billet, converted to powder for subsequent consolidation to a component, or
investment cast. Remelting is used to produce an ingot that can be processed to
billet for forging or to mill forms (e.g., bar stock). Until the start of the second
half of the twentieth century, melting of superalloys was conducted in air or
under slag environments. The properties of modern superalloys derive principally
from the presence of many elements that are reactive with oxygen and so were
being lost to some degree in the customary melting and casting processes of the
time. When vacuum melting techniques were introduced to commercial produc-
tion of articles, they were pioneered by superalloys. Vacuum melting enabled
the production of superalloys containing higher amounts of the hardeners alu-
minum and titanium. Furthermore, the concurrent reduction in gases, oxides, and