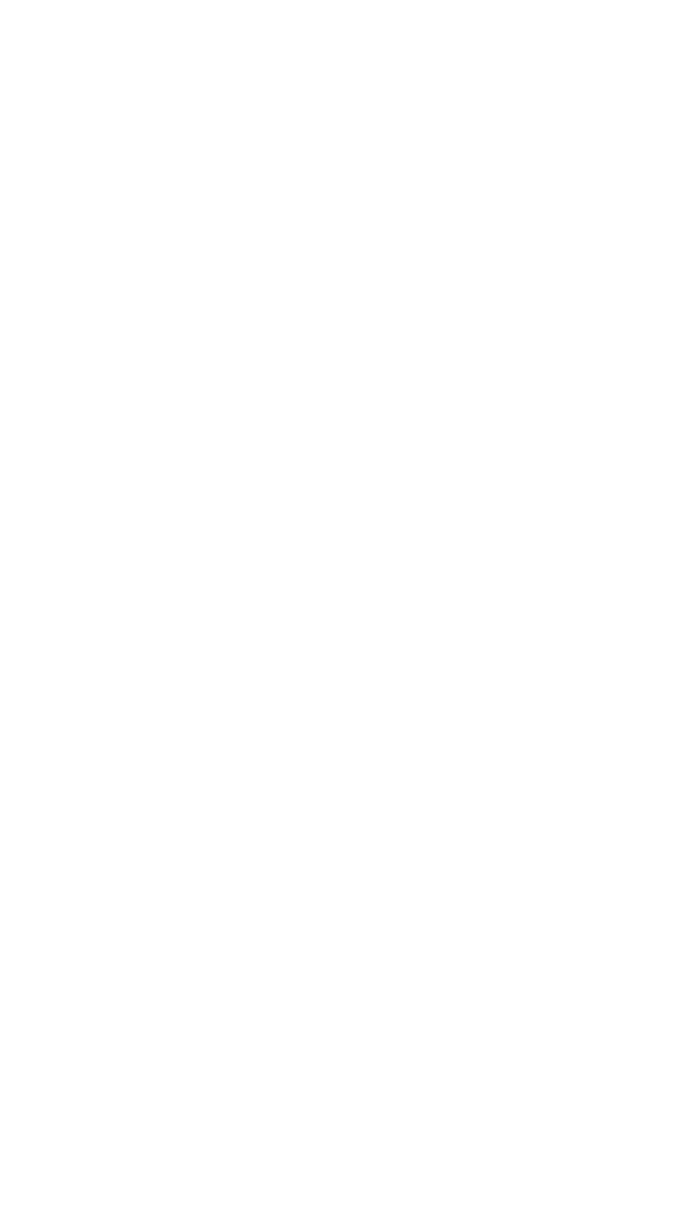
7 OTHER ASPECTS OF TITANIUM ALLOY SELECTION 231
For PAW, a filler metal may or may not be used for welding metal less than
12.7 mm (0.5 in.) thick.
Titanium and its alloys can be brazed. Argon, helium, and vacuum atmo-
spheres are satisfactory for brazing titanium. For torch brazing, special fluxes
must be used on the titanium. Fluxes for titanium are primarily mixtures of
fluorides and chlorides of the alkali metals, sodium, potassium, and lithium.
Vacuum and inert-gas atmospheres protect titanium during furnace and
induction-brazing operations. Titanium assemblies frequently are brazed in high-
vacuum, cold–wall furnaces. A vacuum of l0
⫺
3
torr, or more, is required to braze
titanium. Ideally, brazing should be done in a vacuum at a pressure of about
10
⫺
5
–10
⫺
4
torr or done in a dry inert-gas atmosphere if vacuum brazing is not
possible.
7 OTHER ASPECTS OF TITANIUM ALLOY SELECTION
7.1 Corrosion
Although titanium and its alloys are used chiefly for their desirable mechanical
properties, among which the most notable is their high strength-to-weight ratio,
another important characteristic of the metal and its alloys is titanium’s outstand-
ing resistance to corrosion. CP titanium offers excellent corrosion resistance in
most environments, except those media that contain fluoride ions. Unalloyed
titanium is highly resistant to the corrosion normally associated with many nat-
ural environments, including seawater, body fluids, and fruit and vegetable
juices. Titanium exposed continuously to seawater for about 18 years has un-
dergone only superficial discoloration. Titanium is more corrosion resistant than
stainless steel in many industrial environments, and its use in the chemical pro-
cess industry has been continually increasing. Titanium exhibits excellent resis-
tance to atmospheric corrosion in both marine and industrial environments.
The major corrosion problems with titanium alloys appear to be crevice cor-
rosion, which occurs in locations where the corroding media are virtually stag-
nant. Pits, if formed, may progress in a similar manner. Other problem areas are
with a potential for stress–corrosion, particularly at high temperatures, resulting
in hot-salt stress–corrosion cracking (HSSCC). HSSCC has been observed in
experimental testing and an occasional service failure. Stress–corrosion cracking
(SCC) is a fracture, or cracking, phenomenon caused by the combined action of
tensile stress, a susceptible alloy, and a specific corrosive environment. Another
important characteristic of SCC is the requirement that tensile stress be present.
Aluminum additions increase susceptibility to SCC; alloys containing more than
6% Al generally are susceptible to stress–corrosion.
HSSCC of titanium alloys is a function of temperature, stress, and time of
exposure In general, HSSCC has not been encountered at temperatures below
about 260
⬚C (500⬚F). The greatest susceptibility occurs at about 290–425⬚C
(about 550–800
⬚F) based on laboratory tests. Time-to-failure decreases as either
temperature or stress level is increased. All commercial alloys, but not unalloyed
titanium, have some degree of susceptibility to HSSCC. Alpha alloys are more
susceptible than other alloys.
7.2 Biomedical Applications
Titanium alloys have become standards in the orthopedic industry where hip
implants, for example, benefit from several characteristics of titanium: