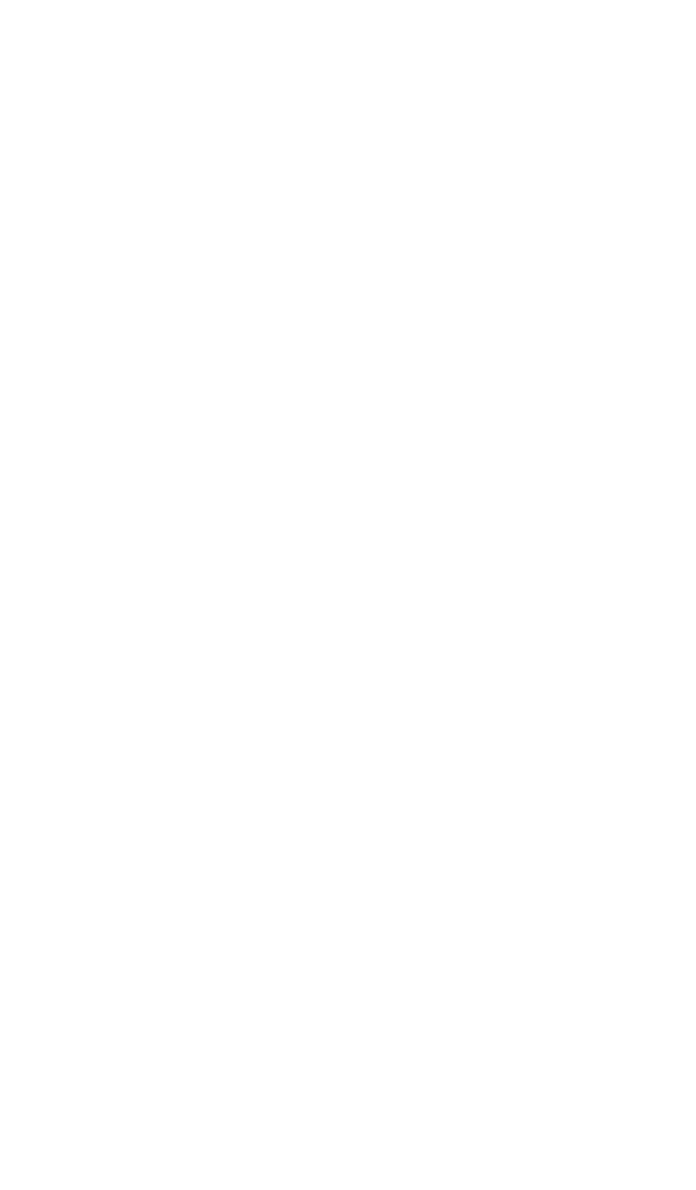
6 MANUFACTURING PROCESSES 227
application of melting principles. Melting practices may be classified as either
primary (the initial melt of elemental materials and/or scrap which sets the
composition) or secondary (remelt, often more than once, of a primary melt for
the purpose of controlling the solidification structure). The melt type or com-
bination of melt types selected depends upon the alloy composition, mill form
and size desired, properties desired, and sensitivity of the final component to
localized inhomogeneity in the alloy.
The principal method for the production of titanium electrodes and ingots
since commercial introduction of titanium alloys occurred in the 1950s has been
the use of vacuum arc remelting (VAR). The purity of the titanium alloys pro-
duced is a function of the purity of the starting materials. Control of raw ma-
terials is extremely important in producing titanium and its alloys because there
are many elements of which even small amounts can produce major, and at
times undesirable, effects on the properties of these metals in finished form. To
produce ingots of titanium or its alloys for commercial application, titanium
from sponge is commonly alloyed with pure other elements, master melt of
titanium plus alloy elements, and/or reclaimed titanium scrap (usually called
‘‘revert’’).
Because sponge is an uneven product consisting of a loose, granular mass, it
does not compact as well as might be desired in some instances. Compacting is
needed to make an electrode from which to melt the alloy. During melting, a
piece of the sponge might fall unmelted into the solidifying electrode. Perhaps
a chunk of revert or master melt might fall in. Whatever the situation, a gross
inhomogeneity would result. Depending on the type and size of the inhomoge-
neity, a major structural defect could exist. Consequently, after some significant
incidents in aircraft gas turbine engines about 30–40 years ago, second and then
third melts were instituted to provide almost certain homogenization of the alloy.
Defects have been a concern for titanium ingot metallurgy production since
the early days of the industry. Different types of defects were recognized, most
stemming from sponge handling, electrode preparation, and melt practice. The
principal characterization of these defects was as low-density inclusions (LDI)
and high-density inclusions (HDI). Over two dozen different defects have been
cataloged. Defects prompted strict process controls that were agreed upon jointly
by metal suppliers and customers alike. These controls have done much to attain
either reduced-defect or defect-free materials. Despite the controls, occasional
defects have been involved in significant events of titanium-alloy-related failures.
It is predicted that the introduction of cold-hearth technologies will further re-
duce the incidence of defects in titanium ingots. Electron beam and plasma arc
melting technologies are now available for the melting of titanium alloys or the
remelting of scrap. The use of these technologies permits the controlled hearth
melting (CHM) of titanium alloys. Studies on electron-beam cold-hearth melting
(EBCHM) and plasma arc melting (PAM) demonstrated the ability of hearth
melting to remove HDI with great confidence. LDI are also addressed by CHM.
6.3 Forging Titanium Alloys
Manufacturing processes such as die forging, hot and cold forming, machining,
chemical milling, joining, and sometimes, extrusion are all secondary fabrication
processes used for producing finished parts from billet or mill products. Each