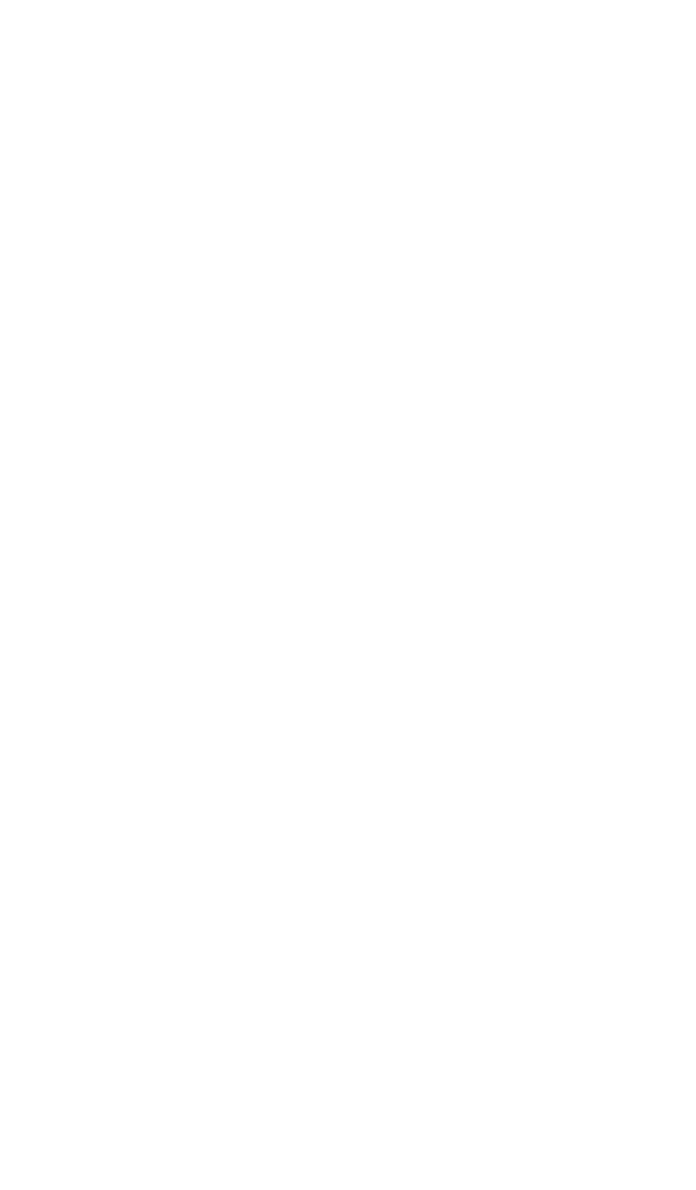
5 BASICS OF WEAR MATERIALS 1279
deposition parameters, using additives, changing substrate selection, and varying
the seeding and nucleation method.
5 BASICS OF WEAR MATERIALS
Wear materials tend to be one of two types: (1) bulk solids or (2) coatings, films,
and surface treatments. A bulk wear material will typically provide long-term
wear surface use. There is more of a wear part available for continued use
provided that significant dimensional changes have not affected the actual per-
formance of the tool. However, the lack of availability of a wear material in
bulk form or difficulty or expense in its manufacture can force the use of coatings
or films instead. Likewise, coatings or films can enable the use of a material
that is unsuitable in the bulk form but has very good performance when com-
bined with other materials in a multicomponent wear system. The trade-off in
the use of bulk and film materials is the possibility of enhanced performance of
a coated tool versus the cost and effort required to make the coated tool. Other
factors such as increased tool lifetime and length of time between tool changes
may make a coated wear system attractive with respect to an inexpensive bulk
material system. Cost and availability are two factors that strongly govern the
selection of a bulk material or a surface treatment for a particular wear appli-
cation.
The following references provide a rich resource for review and further ex-
ploration of the properties and behavior of wear materials: Buckley and Rabi-
nowicz (1986), Apachitei and Duszczyk (2000), Bull and Matthews (1992), Bull
et al. (1988), Formanek et al. (1993), Jackson and Mills (2000), Joost and
Schwedes (1996), Karja et al. (1993), Foroulis (1984), Dobrzanski (2001), John
(1984).
The general application of wear materials in varied situations are addressed
in a number of the following references: Ball and Ward (1985), Balon and
Aizinbud (1989), Berns (1995), Bull et al. (2000), Burkle et al. (1995), Cooper
et al. (1992), Franklin and Beuger (1992), Franklin and Dijkman (1995), Gagg
(2001), Gandhi and Agrawal (1994), Garbar (1995), Gates and Eaton (1993),
Geiger (1992), Hsu et al. (1991), Hsu and Shen (1996), Jang and Kim (1996),
Jilbert and Field (1998), Jones (1997), Jung (2000), Klocke and Krieg (1999),
Korsunsky et al. (1995), Kuljanic (1992), Kurzynski (1996), Larsen-Basse
(1990), Lempert (1988), Llewellyn (1996), Lohmann and Van Valkenhoef
(1989), Lyons (1998), Mainwaring (1994), Manning et al. (1984), Margus and
Comerford (1994), Martinella (1993), Medley (1992), Meyerrodenbeck et al.
(1992), Mikhailin et al. (1985), Nuttall (1985), Onate et al. (1998), Paller (1991),
Pascheto and Behnood (1997), Pejryd et al. (1995), Penlington et al. (1995),
Phillips and Knapp (1995), Ramalingam and Zheng (1995), Reinhard and Volz
(1983), Robinson et al. (1993), Rozenberg et al. (1987), Sare and Arnold (1995),
Sessler et al. (1993), Sexton et al. (2001), Stack (1997), Stewart (1997), Stokes
and Cooley (1985), Suchanek et al. (1999), Thompson (1994), Uma Devi and
Mohanty (1998), Voronenko (1992), Ward et al. (1996a), Wassell et al. (1997),
and Wendl and Wupper (1991).
Hardness is related to wear in that if it is very difficult to break one bond,
then the chances of breaking many bonds (wear) will be low. A related series
of references deal with the use of hard materials in wear applications: Bulloch