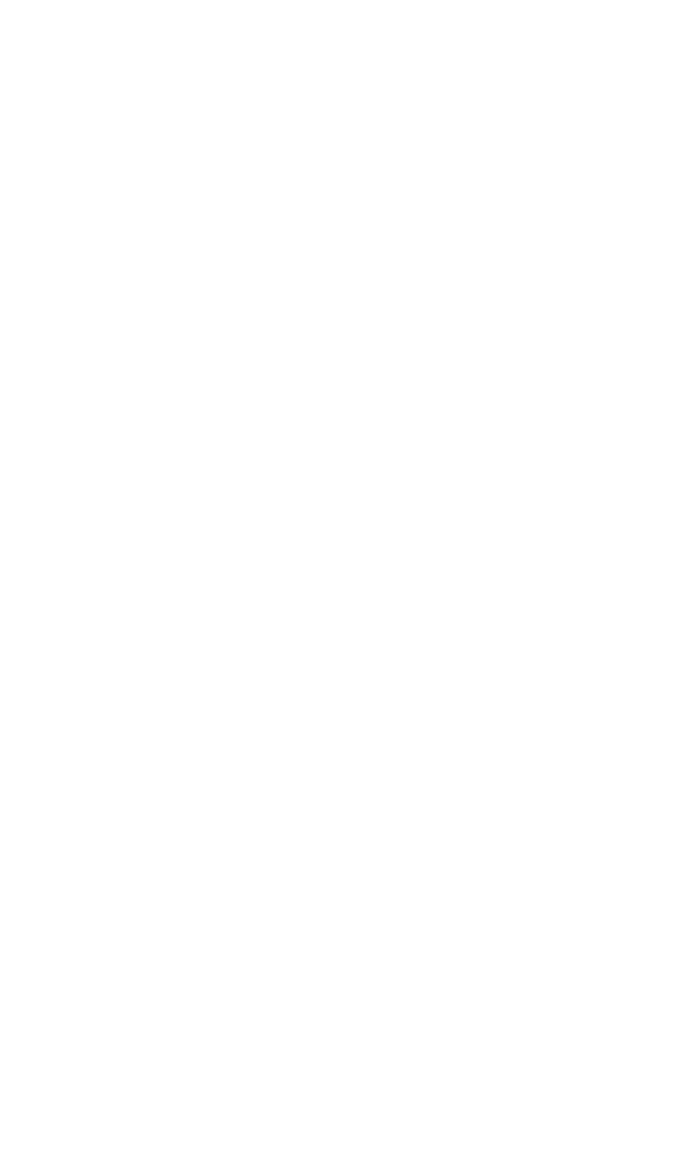
1248 MATERIALS IN ELECTRONIC PACKAGING
this heat must be shunted away to prevent cracking and other deterioration. The
material also shrinks up to 10% by volume during cure, thus having an impact
on the configuration of the mold. The addition of fillers, pigments, and lubricants
may also be used to control shrinkage.
The allyl polymer family is characterized by good dimensional stability, hav-
ing electrical insulation properties, the ability to withstand elevated temperatures,
and good moisture resistance. A commonly used allyl includes glass-filled diallyl
phthalate, which is dimensionally stable and is used to make inserts in con-
nectors, electronic parts, housings, and to form insulating standoff posts.
Epoxy materials adhere well and are used as adhesives as well as for potting,
casting, and encapsulation purposes. The properties may be varied from flexible
to rigid. The final weight, strength, thermal conduction, and thermal expansion
may be modified by inclusion of filler materials. Epoxies are used to encapsulate
circuits such as microcircuit chips in multichip modules (MCM), chips-on-board
(COB), and conventional components in cordwood array packaging. Epoxy res-
ins are used with glass fabrics and phenolic laminates to fabricate printed circuit
boards; they also are used for conformal coating, encapsulation, adhesives, and
in forming durable paints and finishes.
Phenolic materials are used for high-temperature, high mechanical strength
(relative to other plastics), and low-cost applications. Phenolics are used to fab-
ricate knobs, handles, connectors, chip carriers, and in laminate form are used
to build small enclosures. Phenolics are not elastic and may fracture upon bend-
ing or impact loading.
Polyimide materials exhibit low outgassing, good radiation resistance, and
have very good high- and low-temperature performance. They must be used with
care because they are sensitive to moisture and are degraded by organic acids
and alkalis. Applications include bearings, seals, insulators, flexible cable, tapes,
sleeving, moldings, wire enamel, chip carriers, and laminates.
Polyurethane materials are often used as paints, wire enamels, conformal coat-
ings, embedding compounds and foam dielectric and thermal insulation. Some
polyurethane materials may be poured and used as encapsulants to protect cir-
cuits from the environment. They exhibit elastomeric properties and have tear
resistance, abrasion resistance, and unusual toughness. They can be degraded by
strong acids and bases. The operating temperature range is limited and should
not exceed 120
⬚C.
Silicone-based materials have a wide range of general-purpose applications
in electronic equipment. They may be formulated as sealants, elastomers, ad-
hesives, paints, conformal coatings, and encapsulants. They have a broad tem-
perature range (
⫺40 to ⫹250⬚C), have excellent arc resistance, are nonburning,
and are water resistant when fully cured.
A commonly used silicone family is known as the room temperature vulca-
nizing (RTV) adhesives and sealants, which are often used to waterproof a com-
ponent or electrical joint. These products polymerize with water when curing
and in the process release acetic acid in some formulations or ethyl alcohol in
other formulations. In applications where the presence of acetic acid vapor would
degrade circuit elements such as switch and relay contacts, the RTV should be
allowed to fully cure before sealing RTV within an electronic enclosure. Alter-