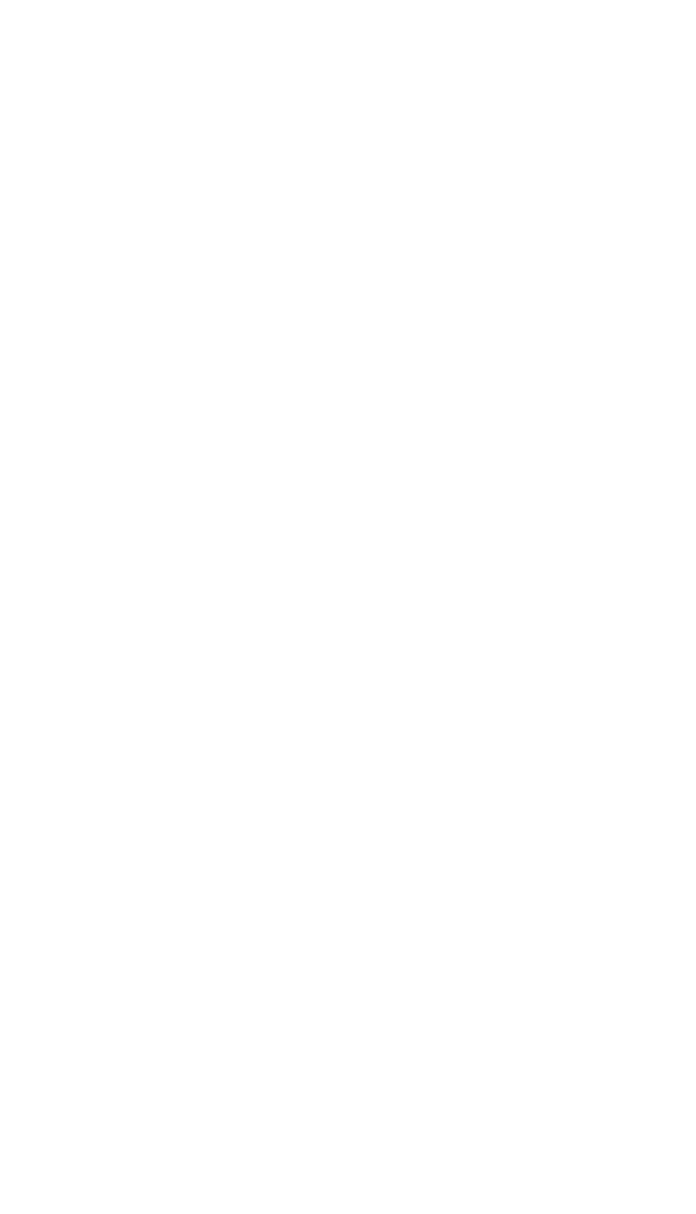
1234 MATERIALS IN ELECTRONIC PACKAGING
of, for relay rack-mounted devices, passing two or more bolts through holes in
the equipment front panel into threaded fasteners in the rack frame. For equip-
ment used in aircraft, ships, and vehicles, ARINC standard modular ATR cases
are placed on an equipment self and secured thereto. The ATR module secure-
ment usually consists of an engagement device in the rear of the module and
brackets with retained thumbscrews or latching hook arrangements at the lower
edge at the front of the module, including a device fastened to the shelf into
which the screws or latches engage. Larger equipment used in moving vehicles,
such as tanks, battleships, and trucks, where the equipment must be protected
from higher levels of vibration and shock loading, often involves bolting the
equipment to a frame, which incorporates energy-absorbing dampers, and bolting
the frame to the structure of the vehicle. For consumer goods applications (car
radios and CD players, motorcycle and bicycle electronics, etc.), a variety of
mounting configurations are employed; some feature quick release of the at-
tached equipment.
Each of the applications place similar requirements on the materials used for
attachment. The dominant considerations are strength, wear resistance, corrosion
avoidance, temperature range, and fatigue resistance. The materials are usually
selected from the steel family to achieve a favorable strength-to-weight ratio.
For mounting bolts used to fasten commercial goods and other equipment used
in relatively benign environments, cadmium- or nickel-plated steel hardware is
used. If the mechanical loads are severe, higher strength SAE-grade steels must
be used. For more corrosive environments, stainless steel (usually passivated) is
employed. For aggressive high-stress applications where corrosion and wear are
a concern, fastening devices and brackets are made from the precipitation-
hardened stainless steels that are passivated.
5.2 Equipment Racks, Frames, and Mounting Structures
Equipment racks, frames, and mounting structures such as an equipment shelf
are designed to bear the weight of electronic equipment mounted thereto. The
dominant considerations are strength, wear resistance, corrosion, electrical con-
ductivity, and corrosion avoidance. The materials of preference include heat-
treated high-strength aluminum (such as 6061-T6) and mild steel materials. The
aluminum materials are almost always either anodized or treated (chromate dip
or similar) and painted for appearance and protection from the elements. Steel
materials are protected from rust by nickel, zinc, or other electroplated finish
and often by a rust-resistant paint. Stainless steel parts are passivated to improve
resistance to corrosion.
5.3 Equipment and Module Enclosures
Enclosures are the cases or boxes that house electronic equipment. Dominant
considerations include operating temperature range, electromagnetic and electro-
static shielding, magnetic shielding, strength, wear resistance, thermal conduc-
tivity, appearance, corrosion resistance, and perhaps chemical inertness.
Materials used for enclosures vary with the application and end-user market.
They include both metal and plastic materials. Cost containment, ease of fabri-
cation, and appearance are often the overriding considerations.
When electromagnetic, electrostatic, and magnetic shielding protection is not
required, plastics materials are often used to fabricate enclosures. Aluminum and