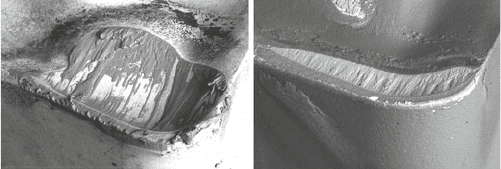
82 3 Fundamentals of Cutting
after these sample halves were grinded and buffed, the distribution of elements
was analysed with a microprobe perpendicularly to the contact surface cutting tool
material/material.
As the quantitative line scans in Fig. 3.40 show, diffusion phenomena take place
under the selected annealing parameters between the uncoated cemented carbide
and the austenitic steel material here selected. On the side of the steel material,
there is a diffusion of iron, chrome and nickel into the cutting tool material. In t he
opposite direction (i.e. from the cutting material into the material) tungsten and
cobalt diffuse.
The dissolution of tungsten carbide, the bearer of hardness and wear resistance,
caused by the diffusion of iron into the cemented carbide leads to a weakening
of the structure and lowers the resistance of the cemented carbide substrate against
abrasion. The consequence of this is the formation of distinct crater wear (Fig. 3.41).
Since diffusion phenomena depend on temperature, the cutting speed influences on
an elementary level the speed with which crater wear develops. Uncoated cemented
carbides can thus only be used at relatively low cutting speeds (v
c
< 100 m/ min).
The cemented carbide substrate also has a serious effect on crater formation. Mixed
carbides on the basis of titanium and tantalum/niobium have, in comparison to WC,
a much higher chemical stability towards iron. Mixed carbides reduce the diffusion
of iron into the cobalt binder phase, thus increasing the resistance of the cutting tool
material to crater wear and increasing its heat wear resistance quite substantially.
The most eff ective way to reduce crater wear is coating the cemented carbide
substrate. Cemented carbide layers seal the substrate surface. This prevents direct
contact between the substrate and the material, thus reducing or suppressing diffu-
sion phenomena. As the line scans of annealing tests in Fig. 3.42 show, diffusion
processes between the cemented carbide substrate and the material can by all means
still occur in the case of TiN or TiCN layers. In contrast, no more diffusion takes
place in the case of the coated cemented carbide with Al
2
O
3
as an intermediate layer.
The aluminium oxide layer thus functions as a diffusion barrier. The elements iron,
nickel and chrome are found in the ZrN surface layer, while tungsten and cobalt are
in the TiN boundary layer (Fig. 3.42). In the aluminium oxide intermediate layer
Coated cemented carbide, t
c
= 20 min
Uncoated cemented carbide, t
c
= 40s
v
c
= 120 m/min, f = 0.32 mm, a
p
= 2 mm v
c
= 200 m/min, f = 0.2 mm, a
p
= 2 mm
Material: X6CrNiMoTi17–12–2
Fig. 3.41 Formation of crater wear on an uncoated and a coated cemented carbide, acc. to
G
ERSCHWILER [Gers04]