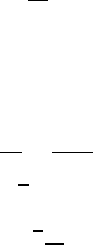
5.3. WET MAGNETIC SEPARATION 397
where T
y
is the volumetric flow rate (in [m
3
/s]) and V is the cross-sectional area
of the matrix (in [m
2
]).
The mean flow velocity of the slurry within the matrix is the interstitial
velocity y, which is related to the superficial velocity by
y =
y
0
(5.14)
where is the porosity of the matrix bed.
The eective length of a particle trajectory is greater than the matrix length
O, because the slurry travels a tortuous path O
w
. The velocity y
0
along the
tortuous path is
y
0
= y
O
w
O
=
y
0
O
w
O
(5.15)
If Karman’s assumption O
w
/O =
s
2 is used [S65], we obtain
y
0
=
s
2
y
0
(5.16)
The eect of flow velocity on separation e!ciency
An increase in flow velocity results in a decrease in the probability of particle
collision with matrix, as illustrated by Fig. 3.35. At the same time, the hy-
drodynamic drag on particles already retained on the matrix increases. The
increase in flow velocity, therefore, results in a deterioration in the e!ciency of
magnetic filtration as shown in Fig. 5.71, which illustrates filtration of PWR
cooling water. Removal of magnetite (- 16 m) from an industrial waste water,
as a function of flow rate, is shown in Fig. 5.72.
A similar trend applies to the removal of impurities from mixtures of materi-
als. The lower the slurry flow velocity, the greater is the removal of magnetizable
particles from a mixture. This eect is shown in Fig. 5.73 for coal desulphuriza-
tion by HGMS. Similarly, in kaolin purification, the concentration of magnetic
impurities in the product increases, as is shown in Fig. 5.74, and brightness de-
creases with increasing flow rate, as shown in Fig. 5.75. In contrast to magnetic
filtration, the flow rate must be specified with due regard for product recovery,
and a compromise must be reached between product quality, product recovery
and throughput of a separator.
The selection of the slurry flow velocity in the application of matrix sepa-
ration to concentration of minerals is dictated by whether the main emphasis
is to be placed on the recovery or on the quality of the magnetic product. An
inverse relationship between product grade and recovery implies that in order
to achieve a high recovery, low flow rates should be used, while a high grade can
be obtained at high flow rates. Magnetic separators can, therefore, be run in a
regime of maximum recovery or in a regime of maximum grade of the concen-
trate, or any regime in between. Typical dependences of the recovery and grade
upon the flow velocity are shown in Figs. 5.76 and 5.77.
The rate of decrease in recovery and increase in grade with increasing flow
velocity are determined by the size distribution and dierences in the values of