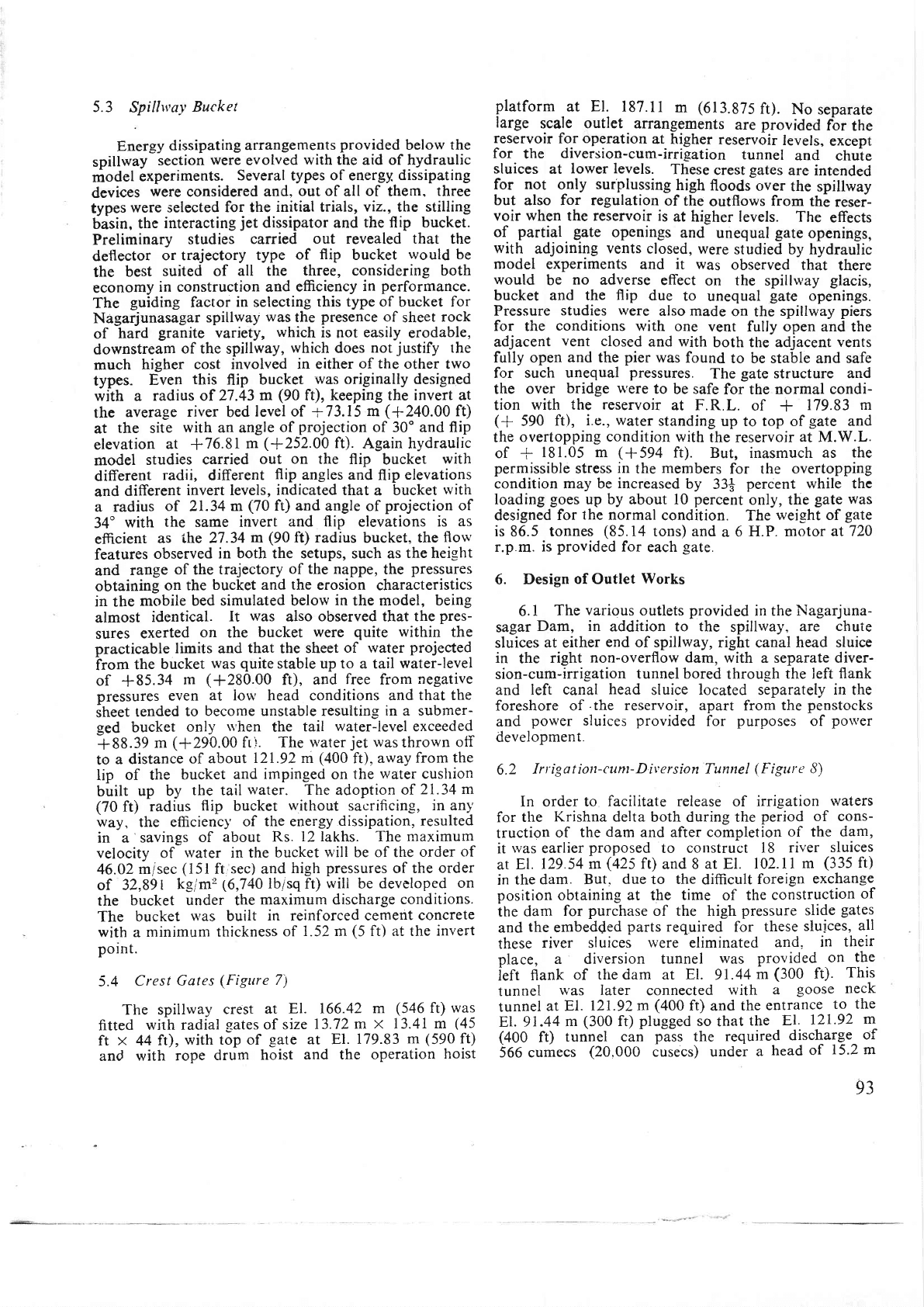
5.3
Spillv'ay
Bucket
Energy
dissipating
arrangements
provided
below
the
spillway
section
were
evolved
with the aid of hydraulic
model
experiments.
Several
types
o[
energy
dissipating
devices
were
considered
and.
out
of
alt
of
them,
three
types
were selected
for the
initial trials,
viz.,
the
stilling
basin,
the
interacting
jet
dissipator and
the
flip
bucket.
Preliminary
studies
carried
out revealed that the
deflector
or trajectory
type
of
flip
bucket
would
be
the
best
suited of
all the
three, considering both
economy
in construction and
efficiency
in
perflormance.
The
guiding
factor
in
selecting
this type of
bucket
for
Nagarjunasagar
spillway
was
the
presence
of
sheet
rock
of
hard
granite
variety,
which
is
not
easily
erodable,
downstream
of the
spillway,
which
does
not
justify
the
much
higher cost involved
in either
of the
other
two
types.
Even
this
flip
bucket
was originally designed
with a
radius of 27.43
m
(90
ft), keeping the invert at
the
average
river
bed
level of
+73.15
m
(+240.00
f0
at
the
site
with
an angle
of
projection
of 30"
and
flip
elevation
at
+76.81
m
(+252.00
ft).
Again
hydraulic
model
studies
carried
out
on the
flip
bucket
with
different
radii,
different
flip
angles and
flip
elevations
and
different
invert levels,
indicated
that
a
bucket
rvith
a radius
of
2I-34
m
(70
ft) and angle
of
projection of
34"
with
the
same invert
and flip
elevations
is
as
efficient
as ihe 27.34
m
(90
ft) radius
bucket,
the
flow
features
observed
in both the setups, such as
the height
and
range
of
the
trajectory
of the
nappe,
the
pressures
obtaining
on
the
bucket and
the
erosion
characteristics
in
the
mobile bed
simulated below
in
the model,
being
almost
identical.
It
was
also
observed that the
pres-
sures
exerted
on
the
bucket
were
quite
within
the
practicable
limits and
that
the
sheet
of rvater
projecteQ
from
the
bucket
was
quite
stable up to a tail
water-level
of
+85.34
m
(+280.00
ft),
and
free
from
negative
pressures
even
at low head conditions and
that the
sheet
tended
to
become unstable resultin-e
in a submer-
ged
bucket
only
u'hen
the
tail
water-level
exceeded
+88.39
m
(*290.00
fil.
The
water
jet
was
thrown
off
to
a distance
of
about
12I.92 m
(400
ft).
away
from the
lip
of the
bucket
and impinged
on
the
water
cushion
built
up by
the tail
water.
The
adoption
of
21.34
m
(70
ft)
radius
flip
bucket
without
sacrificin-e,
in any'
way,
the
efficiency'
of
the energy
dissipation,
resulted
in a'savings
of
about
Rs.
12 lakhs. The
maximum
velocity of
rvater
in the
bucket
will
be
of the
order
of
46.O2
m/sec
(l5l
ft
sec)
and
high
pressures
of the
order
of
32,891
k,eim2
(6,740lb1sq ft)
will
be developed
on
the
bucket under the
maximum discharge
conditions.
The
bucket
was
built
in
reinforced
cement
concrete
with
a
minimum thickness
of
1.52 m
(5
ft) at the
invert
pornt.
5.4
Crest
Gates
(Figure
7'1
The spillway
crest
at
El. 166.42
m
(546
ft)
was
fitted
with
radial
.eates
of size
13.72
m x 13.41
m
(45
ft
x
44
ft),
with top of
-sate
at
El.
179.83
m
(590ft)
and
with
rope
drum
hoist
and the
operation
hoist
platform
at El, 187.11
m
(613.875
ft).
No
separate
large
scale
outlet
arrangements
are
provided
fbr
the
reservoir
for
operation
at higher
reservoir
levels,
except
for
the
diversion-cum-irrigation
tunnel
and chute
sluices
at
lower levels.
These
crest
gates
are
intended
for
not
o-nly
surplussing
high
floods
over
the
spillway
but also for regulation
of the
outflows
from
the
reser-
voir
when
the reservoir is
at higher levels. The
effects
of
partial
gate
openings
and
unequal
gate
openings,
with
adjoining
vents
closed,
were
studied by hydraulic
model
experiments
and
it was
observed
that
there
would
be
no
adverse
effect
on
the
spillway
glacis,
bucket
and the
flip
due
to
unequal
gate
openings.
Fressure
studies
were
also
made
on
the
spillway
piers
for
the
conditions
with
one
venr fully open
and the
adjacent
vent
closed
and with
both the adjacent
vents
fully open
and
the
pier
was
found
to be stable and
safe
for such
unequal
pressures.
The
gate
structure
and
the
over
bridge
were
to
be safe
for
the
normal condi-
tion
with
the reservoir
at F.R.L.
of
+
179.83
m
(+
590
ft),
i.e., water
standing
up to top of
gate
and
the
overtopping
condition
with
the
reservoir
at M.W.L.
of
+
181.05 m
(+594
ft).
But,
inasmuch
as
the
permissible
stress
in
the
members
for the
overtopping
condition may be
increased
by
33+
percent
while the
loading
goes
up by about
l0
percent
only, the
gate was
designed
for
the normal
condition.
The
rvei_eht of
gate
is
86.5
tonnes
(85.14
tons) and
a
6
H.P. motor
at720
r.p.m. is
provided
for
each
_qate.
6.
Design
of
Outlet
Works
6.1
The various
outlets
provided
in the
Nagarjuna-
sagar
Dam, in
addition to the
spillway.
ate
chute
sluices
at either
end
of spillway,
right canal
head sluice
in
the
right
non-overflow dam, with
a separate diver-
sion-cum-irrigation
tunnel bored
through
the Ieft
flank
and left
canal
head
sluice located separately
in
the
foreshore
of
.the
reservoir, apart
from
the
penstocks
and
power
sluices
provided
for
purposes
of
porver
development.
6.2
lrr\atiort-cum-Dit'ersion
Tunnel
(
Figure 8)
In
order to
facilitate
release of
irrigation
waters
for
the
Krishna
delta
both during the
period
of cons-
truction
of
the
dam
and after completion
of
the
dam,
it
rvas
earlier
proposed
to construct
18
river
sluices
at
E[.
129
54
m(a25 ft)
and 8
at
El.
l02.ll
m
(335
ft)
in
the
dam. But.
due
to
the
difficult
foreign
exchange
position
obtaining
at
the
time
of
the construction
of
the
dam
for
purchase
of the high
pressure
slide
gates
and
the
embedded
parts
required
for
these
sluices,
all
these
river
sluices
were
eliminated
and.
in
their
place, a diversion
tunnel
was
provided
on
the
left
flank
of
ttredam at
El.
91.44
m
(300
f0'
This
tunnel
was later
connected
with
a
goose neck
tunnel
at El.
121.92
m
(400
ft)
and
the
entrance
to
the
El.
91.44
m
(300
ft)
plugged
so
that
the
El.
121.92
m
(400
f0
tunnel can
p-ass
the
required
disclarg-e
of
i66..t*."s
(20.000
Cusecs)
undei
a
head
of
15.2 m
93